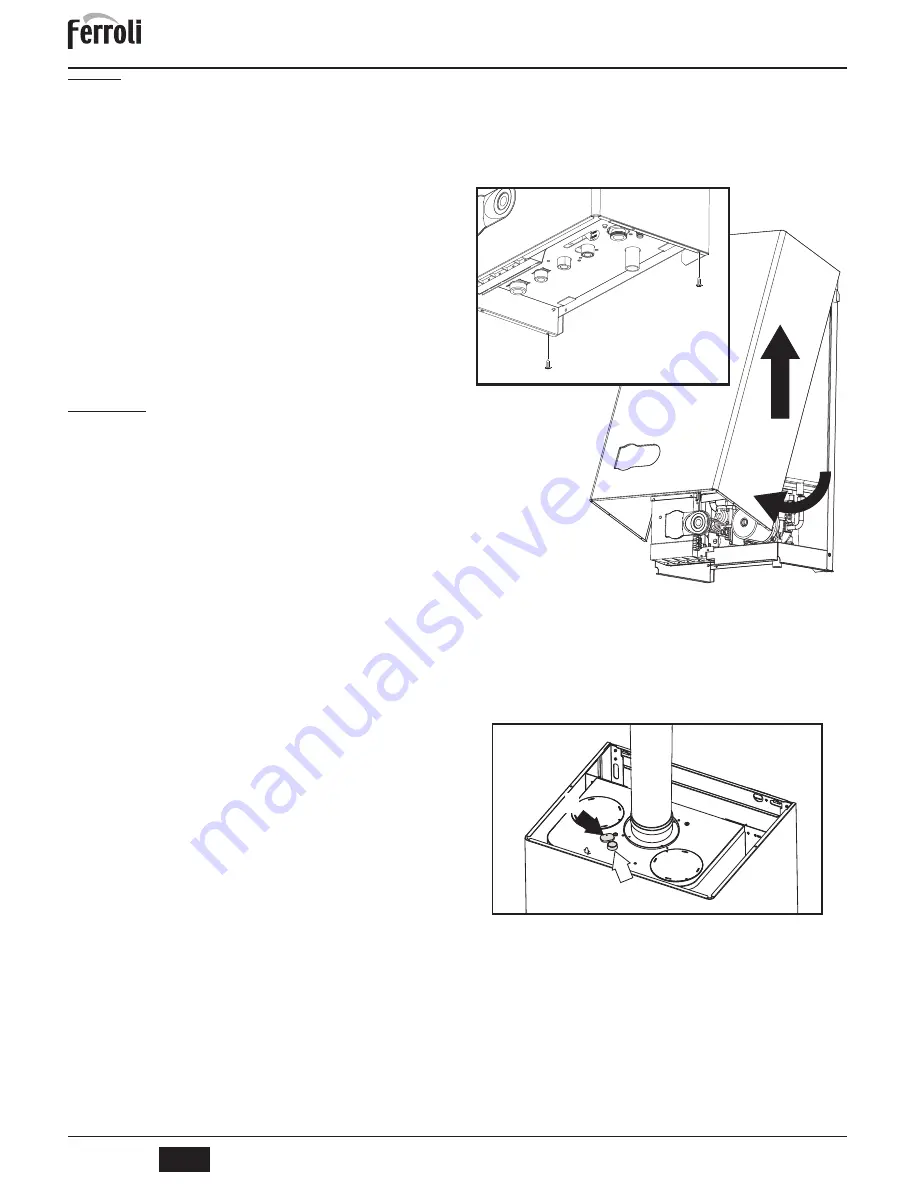
DIVAPROJECT F24
28
EN
cod. 3541F161 - Rev. 00 - 05/2014
4.2 Startup
Before lighting the boiler
•
Check the seal of the gas system.
•
Check correct prefilling of the expansion tank.
•
Fill the water system and make sure all air contained in the boiler and the system
has been vented.
•
Make sure there are no water leaks in the system, DHW circuits, connections or boiler.
•
Check correct connection of the electrical system and efficiency of the earthing system.
•
Make sure the gas pressure for heating is that required.
•
Make sure there are no flammable liquids or materials in the immediate vicinity of
the boiler
Checks during operation
•
Switch the unit on.
•
Check the tightness of the fuel circuit and water systems.
•
Check the efficiency of the flue and air/fume ducts while the boiler is working.
•
Make sure the water is circulating properly between the boiler and the systems.
•
Make sure the gas valve modulates correctly in the heating and domestic hot water
production stages.
•
Check correct boiler lighting by performing various tests, turning it on and off with
the room thermostat or remote control.
•
Make sure the fuel consumption indicated on the meter matches that given in the
technical data table in cap. 5.
•
Make sure that with no demand for heating, the burner lights correctly on opening a
hot water tap. Check that in heating mode, on opening a hot water tap, the heating
circulating pump stops and there is regular production of hot water.
•
Make sure the parameters are programmed correctly and carry out any required
customisation (compensation curve, power, temperatures, etc.).
4.3 Maintenance
Periodical inspection
To ensure proper operation of the unit over time, have qualified personnel carry out a
yearly inspection, providing for the following checks:
•
The control and safety devices (gas valve, flow switch, thermostats, etc.) must func-
tion correctly.
•
The fume exhaust circuit must be perfectly efficient.
(Sealed chamber boiler: fan, pressure switch, etc. - The sealed chamber must be
tight: seals, cable glands, etc.)
(Open chamber boiler: anti-backflow device, fume thermostat, etc.)
•
The air/fume terminal and ducts must be free of obstructions and leaks
•
The burner and exchanger must be clean and free of deposits. Do not use chemical
products or wire brushes to clean.
•
The electrode must be properly positioned and free of deposits.
•
The gas and water systems must be tight.
•
The pressure of the water in the system when cold must be approx. 1 bar; otherwise,
bring it to that value.
•
The circulating pump must not be blocked.
•
The expansion tank must be filled.
•
The gas flow and pressure must match that given in the respective tables.
A
The casing, control panel and aesthetic parts of the boiler can be cleaned with
a soft damp cloth, possibly soaked in soapy water. All abrasive detergents and
solvents should be avoided.
Opening the casing
To open the boiler casing:
1.
Undo the screws A (see fig. 12).
2.
Turn the casing (see fig. 12).
3.
Lift the casing.
B
Before carrying out any operation inside the boiler, disconnect the power supply
and turn off the gas cock upstream.
fig. 12 - Opening the casing
Combustion analysis
Two sampling points have been provided at the top of the boiler, one for fumes and the
other for air. To take samples:
1.
Open the air/fume sampling point cap;
2.
Insert the probes as far as the stop;
3.
Check that the safety valve is connected to a drain funnel;
4.
Activate TEST mode;
5.
Wait 10 minutes for the boiler to stabilise;
6.
Take the measurement.
fig. 13 - Fume analysis
1 =
Fumes
2 =
Air
3
2
A
A
1
1
2
Summary of Contents for DIVAPROJECT F24
Page 85: ......
Page 86: ......
Page 87: ......
Page 88: ...FERROLI S p A Via Ritonda 78 a 37047 San Bonifacio Verona ITALY www ferroli it ...