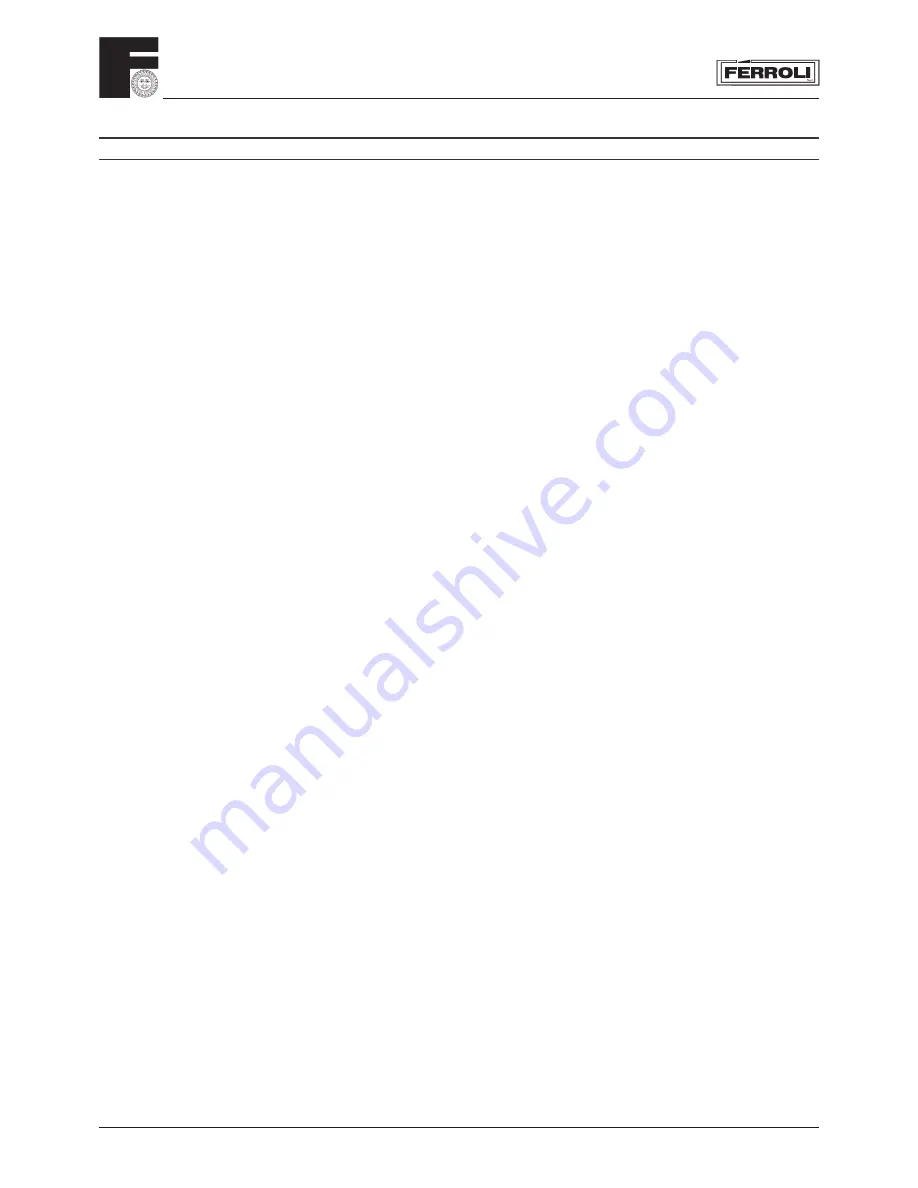
FERROLI F30
28
6. MAINTENANCE AND CLEANING
The following operations must be carried out by Corgi registered engineers only.
6.01 Annual Servicing
The following should be checked at least once a year:
• Water pressure in the central heating system when cold should be about 1 bar. If this is not the case,
bring it back to this value.
• Check control and safety devices (gas valve, fl ow meter, thermostats, etc) are functioning correctly.
• The burner and heat exchanger must be clean. To avoid damage, always clean them with a soft brush or
compressed air. Never use chemical products.
• The expansion vessel must be checked (precharge 1 bar).
• Check there are no leaks in the gas and water circuits.
• Check the air-fl ue gas duct terminal is free from obstructions and sound.
• The electrodes must be free from corrosion build up and correctly positioned.
• Gas fl ow and pressure must correspond to the values given in the Technical Data (page 5).
• The pump must be free to rotate.
6.02 Cleaning the boiler and burner
The boiler should be serviced annually. The heat exchanger and burner must never be cleaned with chemical
products or steel brushes. Particular attention must be paid to all seals and fixings associated with the
room-sealed compartment (gaskets, grommets, etc). Air leakage would cause pressure inside the compartment
to drop, possibly tripping the differential pressure switch and thus shutting down the boiler. After cleaning
particular attention should also be paid to checking stages of start-up and operation of the thermostats,
gas valve and pump.
6.03 Servicing procedure
1. Visually check boiler for correct intallation and fl ueing.
2. Isolate electricity check fuse is 3amp.
3. Remove case by undoing the two screws locate at the bottom rear corners, lift slightly and pull forward.
4. Carry out preliminary electrical checks at boiler junction box. This is located in the centre of the boiler
at the bottom and can be accessed be the removal of a single screw. Any faults found must be rectifi ed
before proceeding.
5. If electrical checks prove O.K. replace cover and secure with screw.
6. Attach a manometer to the boiler gas inlet test point, turn on electricty and fi re boiler for hot water, check
inlet pressure. This should be 20mbar
minimum
for NG and 37mbar for LPG. If this is not the case there is a
supply problem and this will need to be remedied.
7. If inlet pressure is O.K. shut down boiler and remove manometer from gas inlet pressure test point and attach
it to the boiler burner pressure test point. Reseal inlet pressure test point.
8. Fire boiler for hot water and check that the maximum pressure is 13.0mbar for NG and 35.5mbar for LPG.
Turn off tap. Turn P3 on the main circuit board to minimum and fi xe the boiler for heating, check that the
burner pressure reads 2.5 mbar for NG and 7.0mbar for LPG. Turn P3 back to max position. Shut down boiler,
remove manometer, seal test point and re-attach modureg lead. If the pressures are not as specifi ed they will
need to be adjusted on the gas valve (see page 23 - installation manual).
10. Remove fan by undoing the two fan securing screws tilt the front of the fan upwards to detach it from the
securing pin and withdraw it from the boiler, disconnect the wires and air pressure switch tubes.
11. Take off the combustion chamber cover by removing the three securing screws.
12. Lift off fl ue hood and fl ue baffl e plate.
13. Pull off the ignition and fl ame rectifi cation leads from their respective electrodes.
14. Undo the gas union in the centre of burner rail and take out the two securing screws. Remove the burner
rail and clean rail and injectors.
15. Remove two screws securing the burner assembly and remove the assembly. Clean burners.
Summary of Contents for Domina 102
Page 47: ......