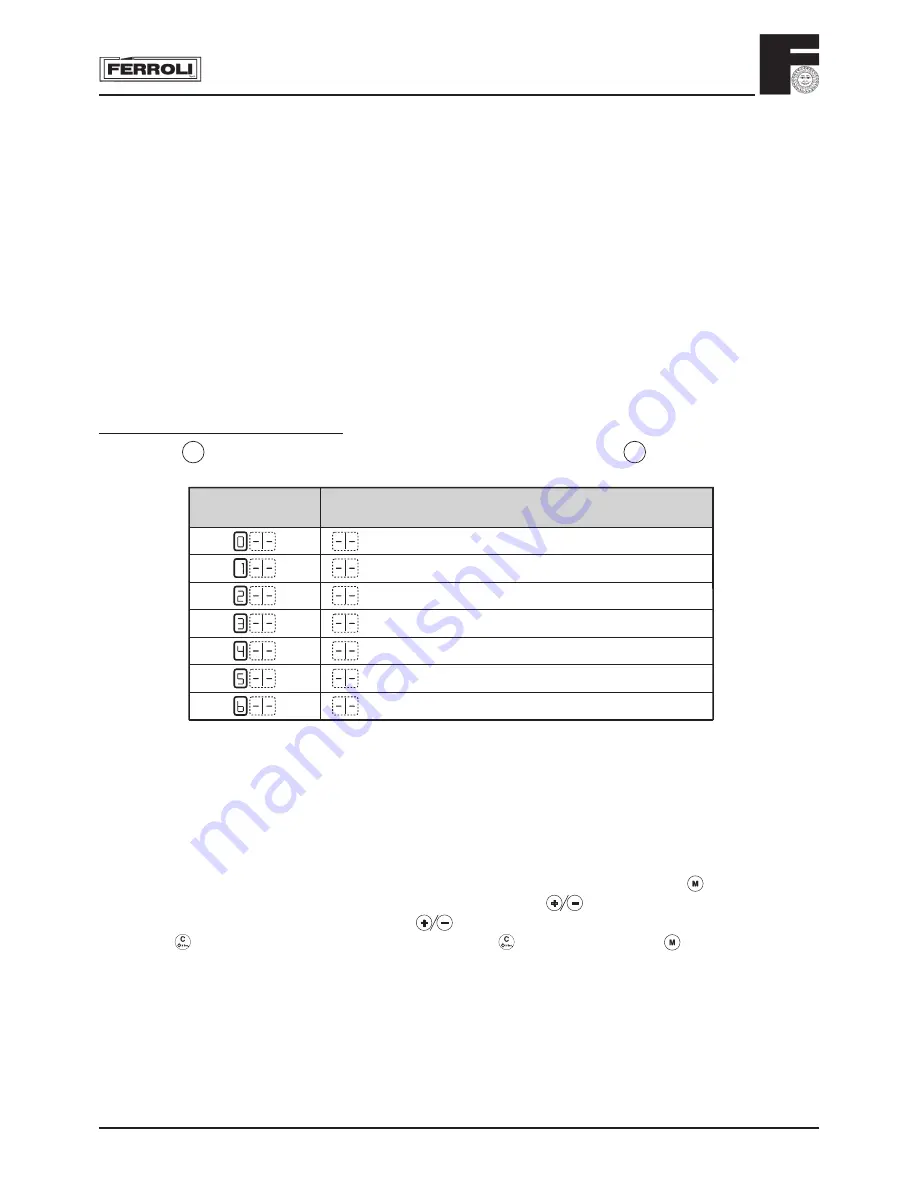
DOMINA N 80 DGT
43
10.02 Ignition
Check than any shut-off valves in the heating system and domestic hot water circuit outside of the boiler
are open. Open the gas cock upstream from boiler and press the main switch. The boiler will perform an
self-test cycle lasting approximately one minute, at the end of which it is ready for operation. The ignition and
shut-down of the burner assembly are completely automatic operations, which depend on the requirements of
the heating system or domestic hot water circuit.
10.03 Shut-down
In the event of extended periods of inactivity close the gas cock upstream from the boiler and disconnect the
electrical power supply to the appliance. In this case, the boiler antifreeze protection function is also disabled; this
function switches on the burner assembly when the heating system temperature falls below 5°C. For extended
periods of inactivity during the winter months, in order to avoid damage due to freezing, all the water should be
drained from the boiler, both the domestic hot water and the heating system; alternatively, drain only the domestic
hot water and introduce the special antifreeze into the heating system.
10.04 Accessing the operating menu
Pressing the M - mode button once accesses the operating menu. Pressing the M mode button again dislays
the following parameters and information in sequence.
Summer (0) / Winter (1) selection
CH outlet temperature view and setting
Domestic hot water temperature
External temperature
-
Domestic hot water flow rate
Compensation curve setting
DISPLAY D1
DISPLAY D2/D3
10.05 Setting the heating system temperature
Set, using the room thermostat or remote control, the desired temperature inside the rooms. When acting on the
room thermostat, the boiler is turned on and the heating system water is brought to the central heating outlet set
temperature or calculated temperature (with temperature scrolling active). On reaching the required temperature
inside the rooms, the generator will switch off.
If no room thermostat or remote control is installed, the boiler will maintain the heating system temperature
at the central heating outlet setpoint.
To set the central heating outlet temperature, access the operating menu, and using the button
display parameter
1 – central heating outlet temperature. On pressing one of the buttons
the display will start to fl ash, showing
the outlet temperature setpoint. Use the buttons
to set the required value. To activate the new value, press
the button
. To cancel the setting, do not press the button
, and press the button
.
10.06 Setting the domestic hot water temperature
Set, using the control boiler panel, the required domestic hot water outlet temperature. On opening a hot water
tap, the system regulates itself to supply water at the set temperature, according to the fl ow rate of delivery
and the temperature of the cold water supplied to the boiler. If in terms of delivery or temperature difference
between the inlet and outlet, the thermal capacity of the generator is exceeded (refer to the technical data), the
outlet temperature will be proportionally lower than the setpoint.
Summary of Contents for DOMINA N 80 DGT
Page 12: ...DOMINA N 80 DGT 12 3 01 Boiler Mounting Plate 149 178 131 Fig 13 ...
Page 46: ......
Page 47: ......