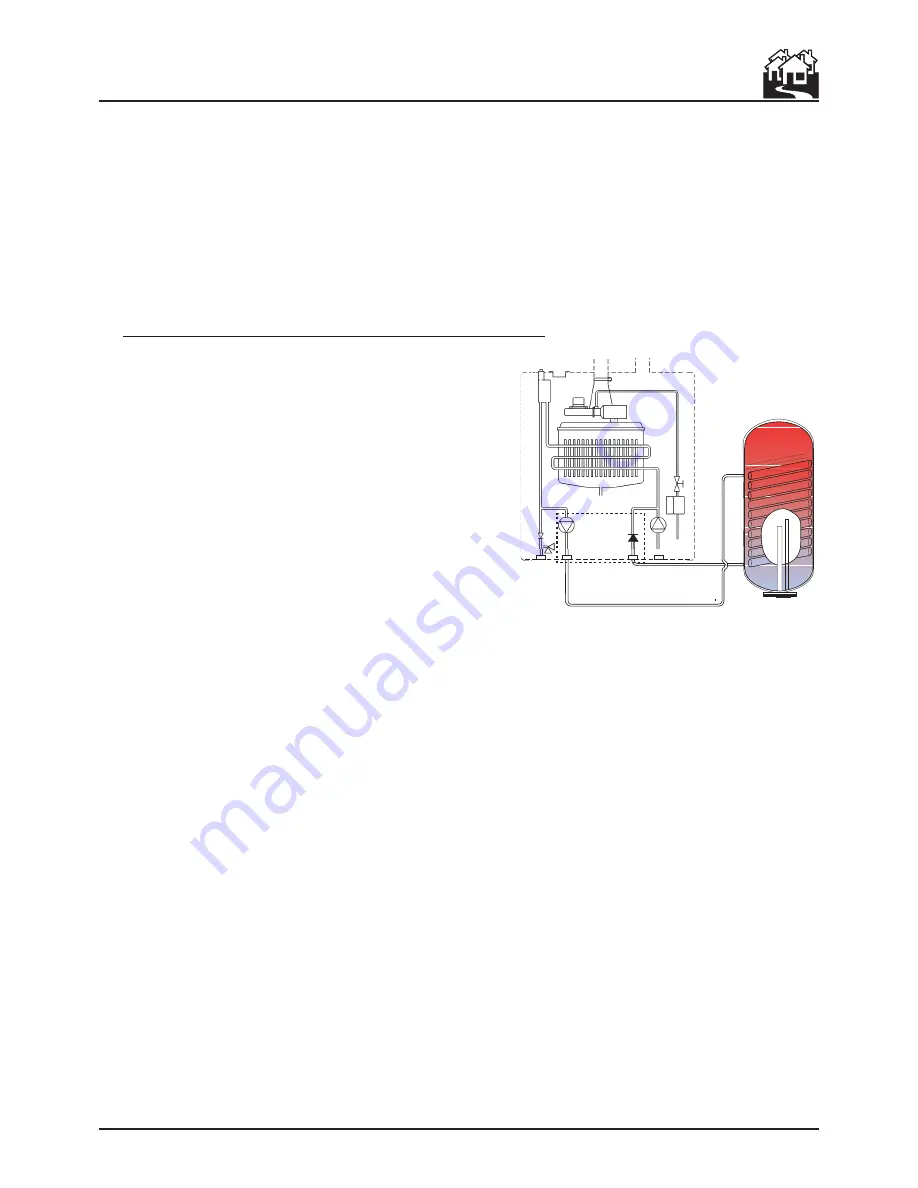
Econcept 50 A
11
a
aaa
aaa
Kit 1KWMH17A
Cylinder not supplied
Fig. 4
DHW calorifier connection(Optional kit 1KWMH17A)
The optional kit 1KWMH17A is available for connection
with an external cylinder. The kit, which includes circulator,
cylinder feeler and hydraulic pipe fittings, has to be mounted
inside the cylinder, according with instruction contained in
the kit itself. Then the connections have to be joined to the
cylinder.
2.4 Connection to the gas system
If necessary the local Gas supplier should be consulted, at
the installation planning stage, in order to establish the
availability of an adequate supply of gas.
An existing service pipe must
not
be used without prior
consultation with the Local Gas supplier.
A gas meter can only be connected by the Local Gas
supplier, or by a Local Gas suppliers Contractor.
Installation pipes should be fitted in accordance with
BS6891.
Appliance inlet working pressure must be 20mbar MINIMUM, for NG and 37 mbar minimum for LPG.
Pipework from the meter to the boiler must be of an adequate size.
Do not use pipes of a smaller size than the boiler inlet gas connection.
The complete installation must be tested for gas soundness and purged as described in BS6981. All pipework
must be adequately supported. An isolating gas valve should be fitted on the boiler gas inlet. Please wait
10 minutes when lighting from cold before checking gas rate. Gas pressures should be checked after the
boiler has operated for 10 minutes to ensure thermal equilibrium.
Make Up Water
Provision must be made for replacing water lost from the sealed system. Reference should be made to
BS6798, for methods of filling and making up sealed systems. There must be no direct connection between
the boiler's central heating system and the mains water supply. The use of mains water to charge and
pressurise the system directly, is conditional upon the Local Water Byelaws. Again any such connection must
be disconnected after use.
Always connect and filling device to the return pipework