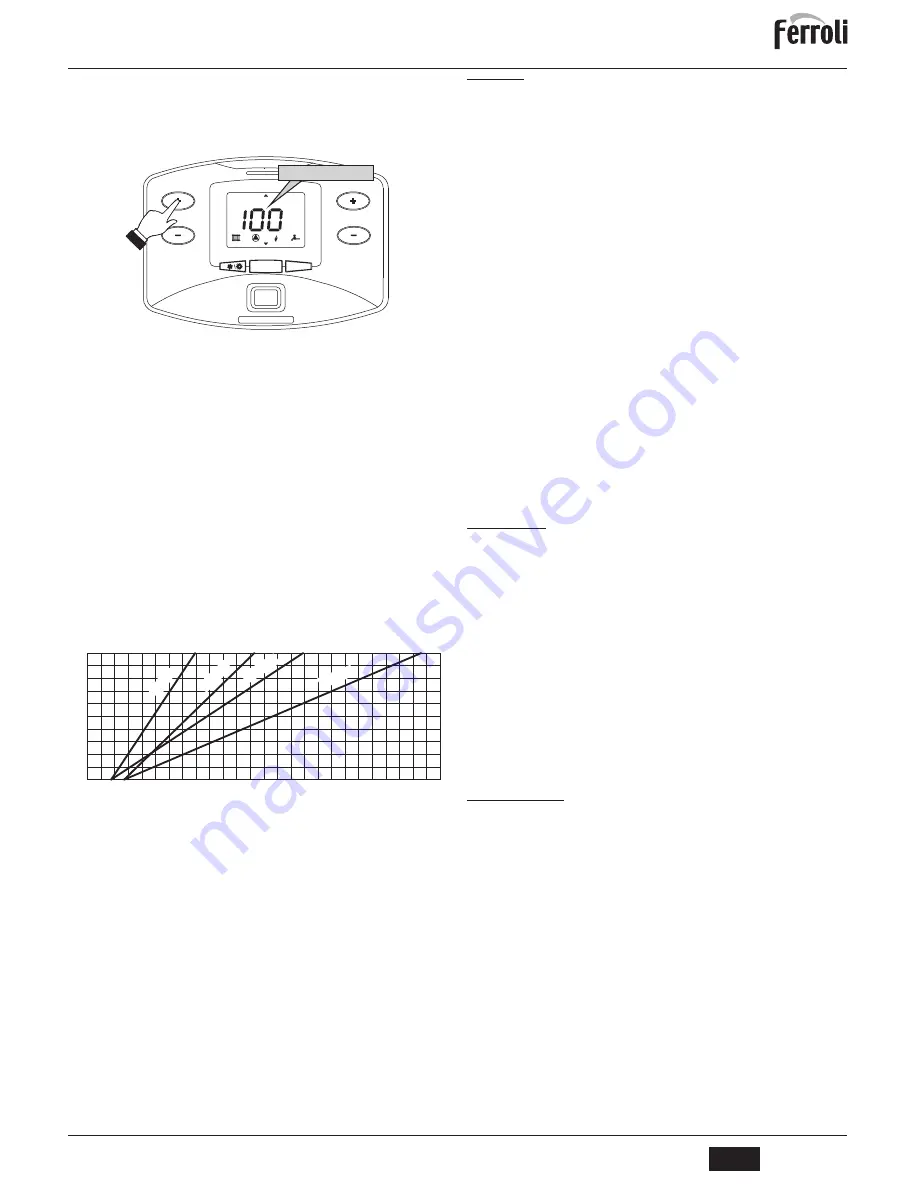
ENERGY TOP B
73
EN
cod. 3540S738 - Rev. 00 - 01/2014
TEST mode activation
Press the heating buttons
+/-
(details 3 and 4 - fig. 1) together for 5 seconds to activate
TEST
mode. The boiler lights at the maximum heating power (Range Rated) set as de-
scribed in the following section.
The heating symbol (detail 13 - fig. 1) and DHW symbol (detail 9 - fig. 1) flash; the heat-
ing power will appear alongside.
fig. 55 - TEST mode (heating power = 100%)
To deactivate Test mode, repeat the activation sequence.
The TEST mode is automatically disabled in any case after 15 minutes.
Only for model ENERGY TOP B 160 - 250
In TEST mode, press the button (detail 7 - fig. 1) to obtain the following operation:
•
Top boiler shell on; bottom boiler shell off.
•
Top boiler shell off; bottom boiler shell on.
•
Top boiler shell on; bottom boiler shell on.
Heating Capacity Adjustment (RANGE RATED)
A
This is a
“RANGE RATED”
boiler (according to EN 483) and can be adjusted
to the system's thermal requirement by setting the maximum heating capacity
for operation in heating mode, as follows:
•
Put the boiler in TEST mode (see sec. 4.1).
•
Press the
heating buttons
(details 3 and 4 - fig. 1) to increase or decrease the power (min.
= 00 - max. = 100). See the diagram “Heating Capacity Adjustment” (fig. 56).
•
Press the
reset button
(detail 8 - fig. 1) within 5 seconds and the maximum heating
capacity will remain that just set. Exit TEST mode (see sec. 4.1).
A
THE HEATING CAPACITY ADJUSTMENT THUS SET ENSURES KEEPING
OF THE EFFICIENCY VALUES DECLARED ON cap. 5.4
Heating power adjustment diagram
A =
kW -
B =
Electronic Board Parameter
fig. 56
4.2 Start-up
B
Checks to be made at first lighting, and after all maintenance operations that
involved disconnection from the systems or an operation on safety devices or
parts of the boiler:
Before lighting the boiler
•
Open any on-off valves between the boiler and the systems.
•
Check the tightness of the gas system, proceeding with caution and using a soap
and water solution to detect any leaks in connections.
•
Check correct prefilling of the expansion tank (ref. sec. 5.4).
•
Fill the water system and make sure all air contained in the boiler and the system
has been vented, by opening the air vent valve on the boiler and any vent valves on
the system.
•
Fill the condensate trap and check correct connection of the condensate elimination
system.
•
Make sure there are no water leaks in the system, DHW circuits, connections or boiler.
•
Check correct connection of the electrical system and efficiency of the earthing system
•
Make sure the gas pressure value for heating is that required.
•
Make sure there are no flammable liquids or materials in the immediate vicinity of
the boiler
Checks during operation
•
Turn the unit on as described in sec. 2.3.
•
Make sure the fuel circuit and water systems are tight.
•
Check the efficiency of the flue and air-fume ducts while the boiler is working.
•
Check the correct tightness and functionality of the condensate elimination system
and trap.
•
Make sure the water is circulating properly between the boiler and the systems.
•
Make sure the gas valve modulates correctly in the heating and domestic hot water
production phases.
•
Check proper boiler lighting by doing several tests, turning it on and off with the room
thermostat or remote control.
•
Using a combustion analyser connected to the boiler fume outlet, check that the
CO
2
content in the fumes, with the boiler operating at max. and min. output, corre-
sponds to that given in the technical data table for the corresponding type of gas.
•
Make sure the fuel consumption indicated on the meter matches that given in the
technical data table on sec. 5.4.
•
Check the correct programming of the parameters and carry out any necessary cus-
tomization (compensation curve, power, temperatures, etc.).
4.3 Maintenance
Periodical check
To keep the unit working properly over time, it is necessary to have qualified personnel
make an annual check that includes the following tests:
•
The control and safety devices (gas valve, flow meter, thermostats, etc.) must func-
tion correctly.
•
The fume extraction circuit must be fully efficient.
•
The airtight chamber must be sealed
•
The air-fume end piece and ducts must be free of obstructions and leaks
•
The condensate evacuation system must be efficient with no leakage or obstructions.
•
The burner and exchanger must be clean and free of scale. When cleaning, do not
use chemical products or wire brushes.
•
The electrode must be free of scale and properly positioned.
•
The gas and water systems must be airtight.
•
The water pressure in the cold water system must be about 1 bar; otherwise, bring
it to that value.
•
The circulation pump must not be blocked.
•
The expansion tank must be filled.
•
The gas flow and pressure must correspond to that given in the respective tables.
A
The boiler casing, panel and aesthetic parts can be cleaned with a soft damp
cloth, possibly soaked in soapy water. Do not use any abrasive detergents and
solvents.
4.4 Troubleshooting
Diagnostics
The boiler is equipped with an advanced self-diagnosis system. In case of a boiler fault, the
display will flash together with the fault symbol (detail 20 - fig. 1) indicating the fault code.
There are faults that cause permanent shutdown (marked with the letter "
A
"): to restore
operation just press the
RESET
button (detail 8 - fig. 1) for 1 second or RESET on the
optional remote timer control if installed; if the boiler fails to start, it is necessary to firstly
eliminate the fault.
Other faults (marked with the letter “
F
”) cause temporary shutdowns that are automati-
cally reset as soon as the value returns within the boiler's normal working range, except
for fault
F37
which is reset by turning the unit off and then on again with button
14
of
fig. 1.
!"!#
!$%
$%&'% #
EANH,.EA-,6
IIIIIII
IIII
III
III
IIII
IIIIIIIIIII
IIIIIIII
IIII
100
90
80
70
60
50
40
30
20
10
0
0
20
40
60
80
100
120
140
160
180
200
220
240
260
!
80
"#
$
12
5"
#$
16
0"
#$
250
"#$
Summary of Contents for ENERGY TOP B 125
Page 23: ......
Page 24: ......
Page 25: ...FERROLI S p A Via Ritonda 78 a 37047 San Bonifacio Verona ITALY www ferroli it ...