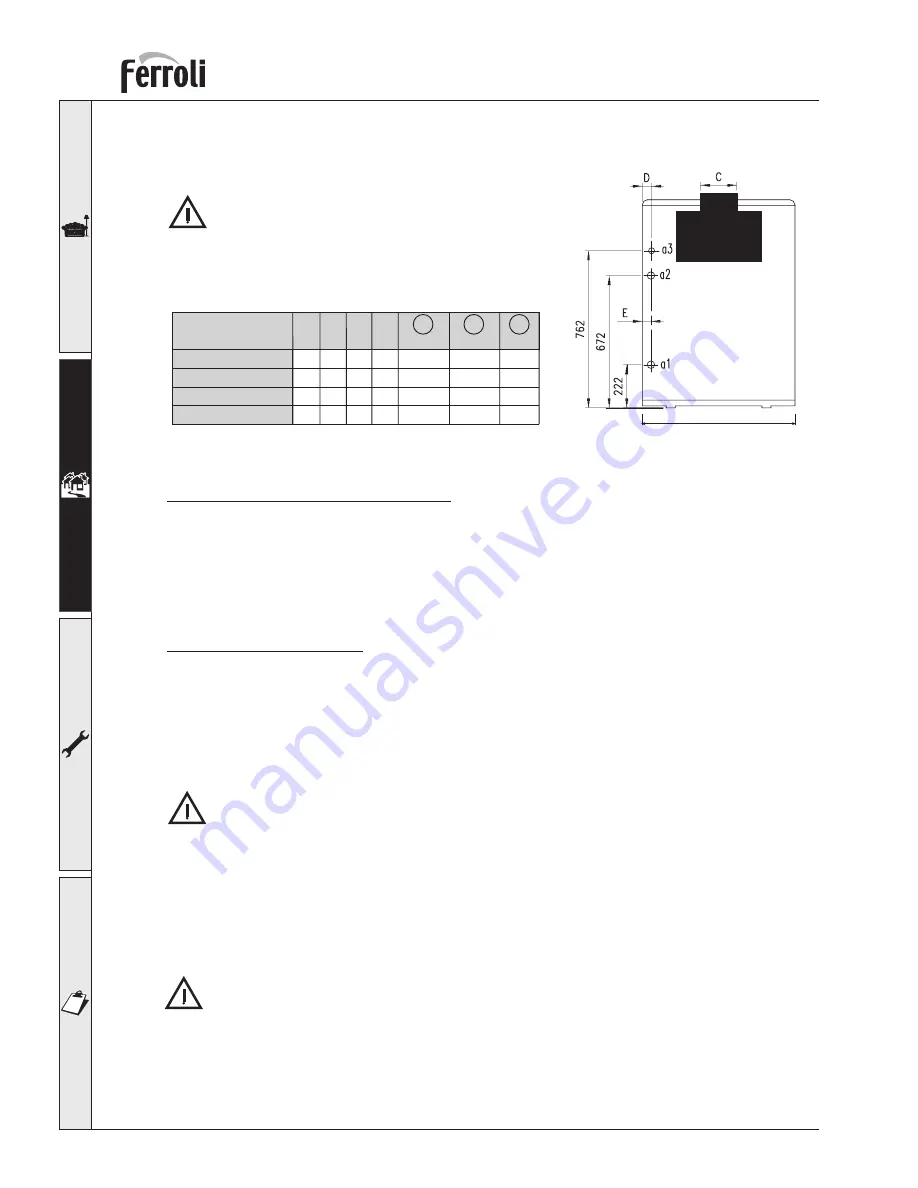
Pegasus F2 N T
10
It is advisable to install on-off valves between the boiler and
heating system allowing the boiler to be isolated from the
system if necessary.
Make the boiler connection in such a way that its internal
pipes are free of stress.
Fig. 5
B
Characteristics of the water system
In the presence of water harder than 25° Fr, we recommend the use of suitably conditioned water in order
to avoid possible scaling in the boiler, caused by hard water, or corrosion produced by aggressive water.
It should be remembered that, because of its low thermal conductivity, even scaling of just a few mm thick
causes signifi cant overheating of the boiler walls with consequent serious problems.
Water treatment is indispensable in the case of very large systems (containing large amounts of water) or
with frequent introduction of replenishing water in the system. If partial or total emptying of the system
becomes necessary under these conditions, it is advisable to refi ll it with treated water.
Filling boiler and system
The fi lling pressure with system cold system must be about 1 bar. If, during operation, the system
pressure falls (caused by evaporation of gas dissolved in the water) to a value below the minimum
described above, the user must bring it back to the initial value. For correct operation of the boiler,
when hot, its pressure must be about 1.5
÷
2 bar.
2.4 Gas connection
Before making the connection, ensure that the unit is arranged for operation with the type of
fuel available and carefully clean all the pipes of the gas system to remove any residues that
could affect good functioning of the boiler.
The gas must be connected to the relative connector (see Fig. 5) in conformity with current standards,
with rigid metal pipes or with continuous fl exible s/steel wall tubing, placing a gas cock between the
system and the boiler. Make sure that all the gas connections are tight.
The capacity of the gas meter must be suffi cient for the simultaneous use of all equipment connected
to it. The diameter of the gas pipe leaving the boiler does not determine the diameter of the
pipe between the unit and the meter; it must be chosen according to its length and loss of head,
in conformity with current standards.
Do not use the gas pipes to earth electrical appliances.
Pegasus F2 N 51 T
Pegasus F2 N 68 T
Pegasus F2 N 85 T
Pegasus F2 N 102 T
550
640
720
800
B
180
180
200
200
C
43
46
44
42
D
35
38
36
34
E
Type and model
3/4
3/4
3/4
3/4
a3
Gas inlet
1 1/2
1 1/2
1 1/2
1 1/2
a2
Heating
delivery
1 1/2
1 1/2
1 1/2
1 1/2
a1
Heating
return
Rear view