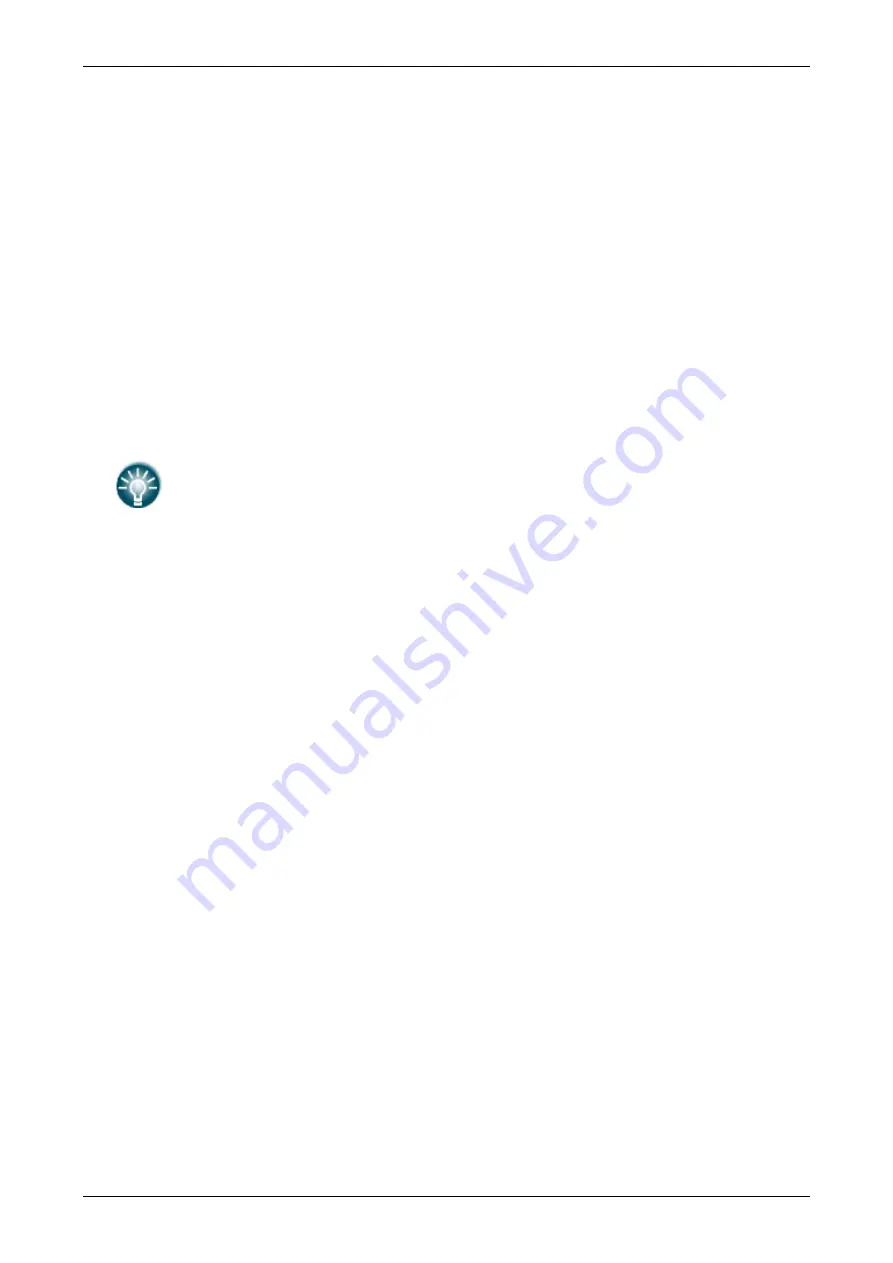
FES BATTERY PACK GEN2 14S, Version 1.23 September 2019
Page 14 of 26
4. Before flight
Valid for FES Self-launchers:
For self-launching FES battery packs must be always recharged, so that maximum power
for good climb rate is available. This is especially important for:
- cold batteries, when voltage drop under high power load is bigger
- short runways
- high altitude runways
- hot summer conditions
Valid for
FES Self-sustainers:
Before each flying day, battery packs should be recharged, especially if motor was
significantly used during previous flights, and long cross-country flight is planned; so that
maximum energy will be available when needed.
Note:
It is recommended to recharge Battery packs just a day or two before
flight is planned. However, plan charging so that there will be enough time for
properly completed charging process!