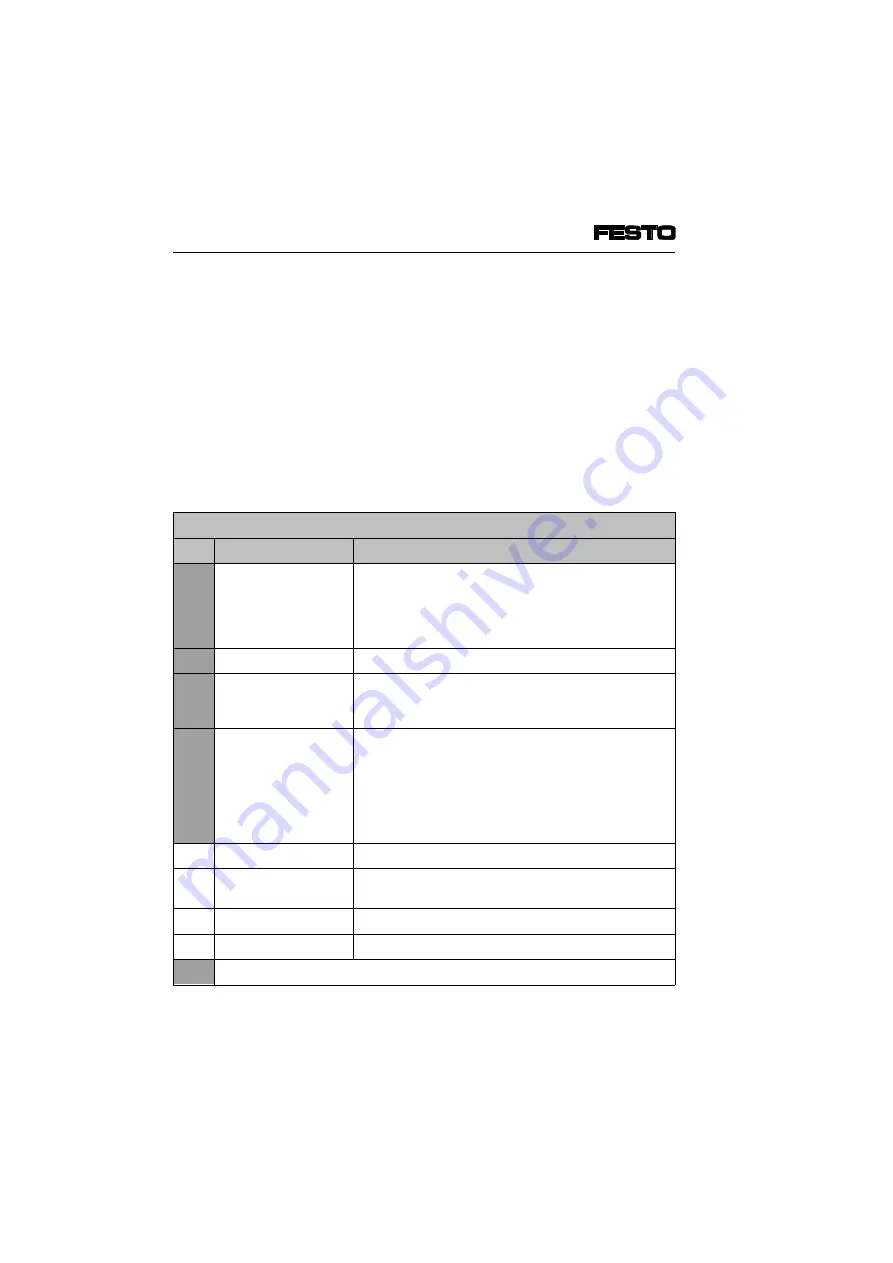
3.3.2 Diagnostic information
The following diagnostic information can be requested
by the DP master from the CP system with the function
Slave_Diag. The CP system replies with an octet string
of length 15.
The procedure for reading out this diagnostic informa-
tion with a SIMATIC S5/S7 system is described in chap-
ter 3.4.2.
Structure of station status 1
Octet 1: Station status_1
Bit
Meaning
Explanation
0
Diag.Station_
Non_Existent
CP system can no longer/cannot yet be addressed.
Possible causes:
– operating voltage not applied
– data cable interrupted
– interference in data cable
1
Diag.Station_Not_Ready
CP system not yet ready for exchange of data
2
Diag.Cfg_Fault
The configuration data received from the master do not
correspond to those ascertained
by the CP system.
3
Diag.Ext_Diag
There is a device-related diagnosis.
Possible causes:
– cable interrupted at I/O module
– short circuit/overload at electrical outputs
– V
valves
< 20.4 V
– V
outputs
<
10
V
– V
sensor
< 10 V
4
Diag.Not_Supported
logic "1": Function not supported by CP system
5
Diag.Invalid_
Slave_Response
Always logic "0" (set by CP system)
6
Diag.Prm_Fault
Last parametrizing telegram faulty
7
Diag.Master_Lock
Always logic "0" (set by CP system)
Valve terminal related bits
Fig. 3/4: Diagnostic bits of station status_1
3. Diagnosis
3-12
CP FB13-E 9904b
Summary of Contents for Compact Performance CP-FB9-E
Page 12: ...Chapter 1 Installation 1 Installation CP FB13 E 9904b 1 1 ...
Page 30: ...Chapter 2 Commissioning 2 Commissioning CP FB13 E 9904b 2 1 ...
Page 70: ...Chapter 3 Diagnosis 3 Diagnosis CP FB13 E 9904b 3 1 ...
Page 95: ...3 Diagnosis 3 26 CP FB13 E 9904b ...
Page 96: ...Appendix A Technical specifications A Technical specifications and index CP FB13 E 9904b A 1 ...