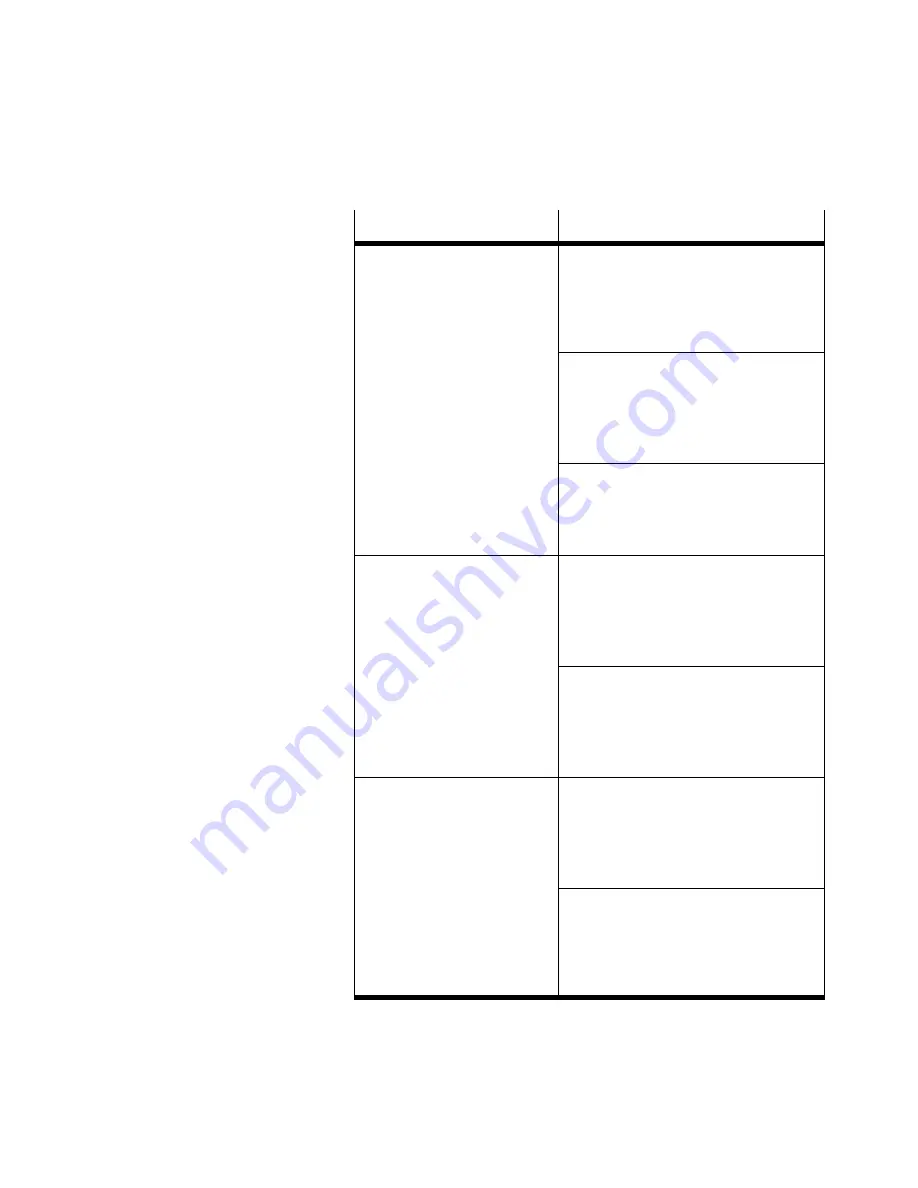
B. Accessories
B−31
Festo P.BE−VIFB11−03−EN en 0503g
Manufacturer
Addresses
Turck
United States
TURCK Inc.
3000 Campus Drive
USA−Plymouth,
MN 55441−2656
England
MTE TURCK Ltd.
Stephenson Road
GB−Leigh−on−Sea,
Essex SS9 5LS
Germany
Hans Turck Gmbh & Co.KG
Witzlebenstraße 7
D−45472 Mülheim an der Ruhr
Philips
Netherlands
PMA Nederland
Gebouw TQIII−4
Postbus 80025
NL−5600 JZ Eindhoven
Germany
Philips Industrial Electrionics
Deutschland
Miramstraße 87
D−34123 Kassel
Selectron
Switzerland
Selectron Lyss AG
Industrielle Elektronik
Bernstrasse 70
CH−3250 Lyss
Germany
Selectron System GmbH
Schupfer Strasse 1
Postbox 31 02 62
D−90202 Nürnberg
Summary of Contents for IFB11-03
Page 2: ......
Page 4: ...Contents and general instructions II Festo P BE VIFB11 03 EN en 0503g...
Page 18: ...Contents and general instructions XVI Festo P BE VIFB11 03 EN en 0503g...
Page 19: ...Summary of components 1 1 Festo P BE VIFB11 03 EN en 0503g Chapter 1...
Page 28: ...1 Summary of components 1 10 Festo P BE VIFB11 03 EN en 0503g...
Page 29: ...Fitting 2 1 Festo P BE VIFB11 03 EN en 0503g Chapter 2...
Page 39: ...Installation 3 1 Festo P BE VIFB11 03 EN en 0503g Chapter 3...
Page 71: ...Commissioning 4 1 Festo P BE VIFB11 03 EN en 0503g Chapter 4...
Page 89: ...4 Commissioning 4 19 Festo P BE VIFB11 03 EN en 0503g Fig 4 4 I O configuration DLC 100...
Page 122: ...4 Commissioning 4 52 Festo P BE VIFB11 03 EN en 0503g...
Page 123: ...Diagnosis and error treatment 5 1 Festo P BE VIFB11 03 EN en 0503g Chapter 5...
Page 144: ...5 Diagnosis and error treatment 5 22 Festo P BE VIFB11 03 EN en 0503g...
Page 145: ...Technical appendix A 1 Festo P BE VIFB11 03 EN en 0503g Appendix A...
Page 159: ...Accessories B 1 Festo P BE VIFB11 03 EN en 0503g Appendix B...
Page 206: ...B Accessories B 48 Festo P BE VIFB11 03 EN en 0503g...
Page 207: ...Index C 1 Festo P BE VIFB11 03 EN en 0503g Appendix C...
Page 208: ...C Index C 2 Festo P BE VIFB11 03 EN en 0503g C Index C 1...
Page 214: ...C Index C 8 Festo P BE VIFB11 03 EN en 0503g...