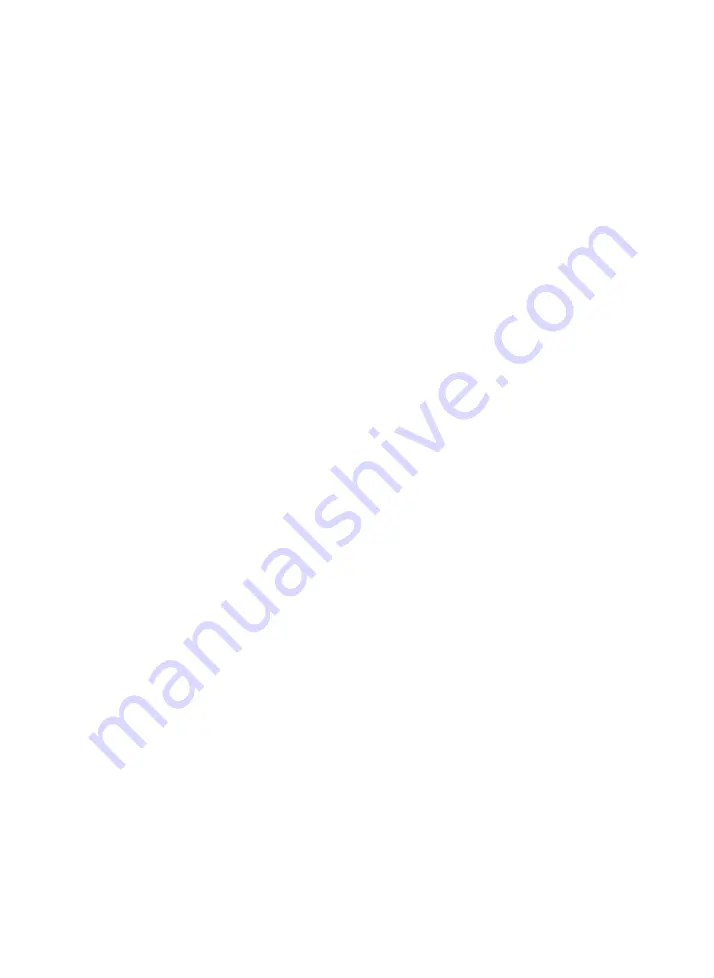
3. Installation
3−6
Festo P.BE−MPA−EN en 0802c
Setting the lubricator:
with the machine running (typical operating status) 0.2 to
max. 1 drop/min. or 0.5 to 5 drops/1000 l air.
Checking the setting:
the procedure described below can be used for checking the
setting of the lubricator.
Proceed as follows:
·
Check the service units in respect of condensate and
lubricator setting twice a week.
1. Ascertain the cylinder which is furthest from the
lubricator.
2. Ascertain the valve terminal which controls this cylinder.
3. Remove the silencer, if fitted, from connection 3/5.
4. Hold a piece of white cardboard 10 cm in front of the
exhaust port.
5. Let the system run for a short period.
There must be only a slight yellow colouring on the
cardboard. If oil drops out, this is an indication that
too much oil has been used.
Another indication of over−lubrication is the colouring or the
condition of the exhaust air silencer. A distinctly yellow
colouring of the filter element or drops of oil on the silencer
indicate that the lubricator setting is too high.
Summary of Contents for MPA-ASI Series
Page 2: ......
Page 4: ...Contents and general instructions II Festo P BE MPA EN en 0802c...
Page 8: ...Contents and general instructions VI Festo P BE MPA EN en 0802c...
Page 18: ...Contents and general instructions XVI Festo P BE MPA EN en 0802c...
Page 19: ...Summary of components 1 1 Festo P BE MPA EN en 0802c Chapter 1...
Page 55: ...Fitting 2 1 Festo P BE MPA EN en 0802c Chapter 2...
Page 71: ...Installation 3 1 Festo P BE MPA EN en 0802c Chapter 3...
Page 106: ...3 Installation 3 36 Festo P BE MPA EN en 0802c...
Page 107: ...Commissioning 4 1 Festo P BE MPA EN en 0802c Chapter 4...
Page 128: ...4 Commissioning 4 22 Festo P BE MPA EN en 0802c...
Page 129: ...Maintenance and conversion 5 1 Festo P BE MPA EN en 0802c Chapter 5...
Page 169: ...Technical appendix A 1 Festo P BE MPA EN en 0802c Appendix A...
Page 186: ...A Technical appendix A 18 Festo P BE MPA EN en 0802c...
Page 187: ...Supplementary component summary B 1 Festo P BE MPA EN en 0802c Appendix B...
Page 201: ...Index C 1 Festo P BE MPA EN en 0802c Appendix C...
Page 202: ...C Index C 2 Festo P BE MPA EN en 0802c Contents C Index C 1...