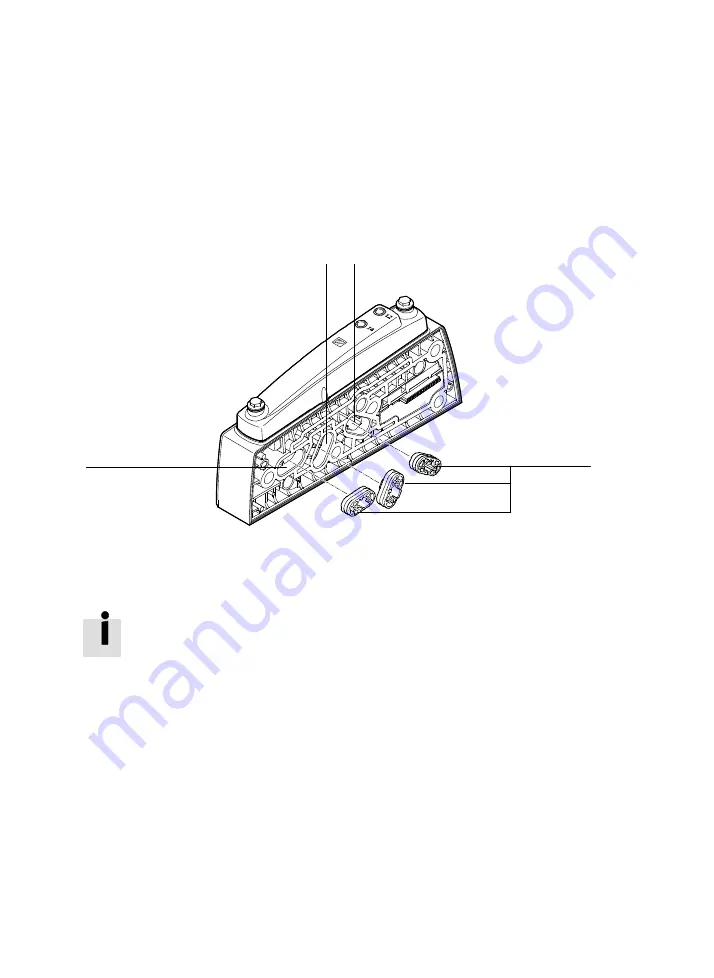
2
Product overview
18
Festo – MPAC-VI-EN – 2017-12a – English
2.4.9
Pressure zone separation
The valves can be supplied with different pressures by creating pressure zones. Separation of the pres
sure zones is achieved through special plugs in the ducts (1), (3) or (5) (
è
valve mounted to the right of the separator belongs to the next (following on to the right) pressure
zone, which is the valve mounted on the manifold sub-base with separator in the current pressure zone.
Installation of the separators is described in chapter 7.5.
2
1
3
4
1
Exhaust duct (3)
2
Supply duct (1)
3
Exhaust duct (5)
4
Separators VMPAC-TE-1-3-5
Fig. 2.6
Pressure zone separators
Pressure zone separation of the pilot duct (12/14) is not provided, since, with the valve
terminal, the pilot air supply for the pilot control of the valves is supplied centrally via
the right end plate.