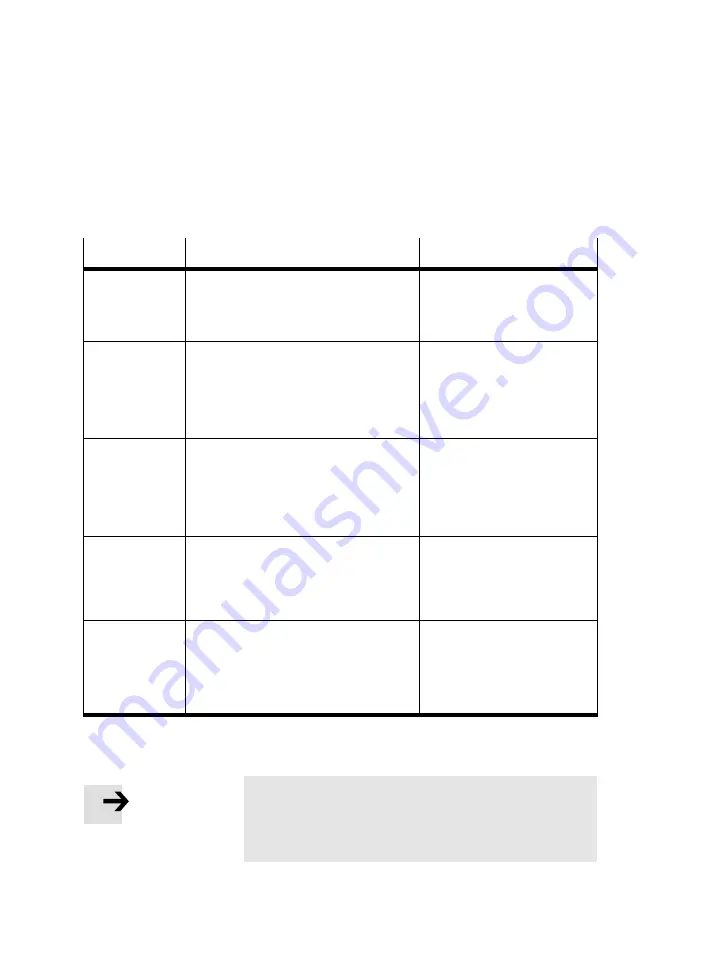
1. System summary
1−18
Festo P.BE−SBO−Q−EN en 0702a
Use the following light sources or lighting techniques:
Light source
Properties
Detection of
Backlighting
Illuminates the inspection part from the
opposite side. The light which shines around
or through the inspection part indicates the
shape of the inspection part.
Contours of (transparent)
inspection parts
Levels of colourless fluids in
transparent containers
Dome light
Throws indirect light toward the inspection
part from different directions and produces
a soft, diffuse and uniform light. Inspection
parts with irregular shapes or curved
surfaces are lighted uniformly. Apertures
can be avoided.
Labels on aluminium packaging
Coating defects on or holes in
inspection parts with curved
surfaces
Stains on uneven or curved
surfaces
Rod light
Produces uniform, direct light on long
inspection parts. The light which hits at an
angle produces diffuse reflection which
allows slight differentiations to be made. For
glossy surfaces, a polarization filter is
recommended.
Faulty contact galvanization
Edges of thin, transparent
inspection parts
Wide−angle light
Throws direct light at a wide angle onto the
edges of the inspection parts (angled
illumination of the surface edges). This
clearly accentuates the edges of the
inspection part and surface defects.
Split−offs on weak−contrast
surfaces and edges
Thickness deviations and
surface defects
Coaxial−vertical
light
Illuminates the inspection part along the
same axis on which the lens is located.
Reflecting light from shiny surfaces is
amplified, and dark diffused light is
scattered. This increases the contrast
between dark and light areas.
Punches/Stamps
Indentations on moulded parts
Defects on the bottoms of
deep−drawing parts
Tab.1/8: Light sources
Note
·
Use backlight preferably if it allows the type of detection.
This usually allows reliable images and results to be pro
duced even if there are disturbances by extraneous light.
Summary of Contents for SBO Q Series
Page 2: ......
Page 8: ...Contents and general instructions VI Festo P BE SBO Q EN en 0702a ...
Page 19: ...System summary 1 1 Festo P BE SBO Q EN en 0702a Chapter 1 ...
Page 37: ...Fitting 2 1 Festo P BE SBO Q EN en 0702a Chapter 2 ...
Page 45: ...Installation 3 1 Festo P BE SBO Q EN en 0702a Chapter 3 ...
Page 60: ...3 Installation 3 16 Festo P BE SBO Q EN en 0702a ...
Page 61: ...Commissioning 4 1 Festo P BE SBO Q EN en 0702a Chapter 4 ...
Page 114: ...4 Commissioning 4 54 Festo P BE SBO Q EN en 0702a ...
Page 115: ...Diagnosis and error treatment 5 1 Festo P BE SBO Q EN en 0702a Chapter 5 ...
Page 122: ...5 Diagnosis and error treatment 5 8 Festo P BE SBO Q EN en 0702a ...
Page 123: ...Technical appendix A 1 Festo P BE SBO Q EN en 0702a Appendix A ...
Page 146: ...A Technical appendix A 24 Festo P BE SBO Q EN en 0702a ...
Page 147: ...Index B 1 Festo P BE SBO Q EN en 0702a Appendix B ...
Page 148: ...B Index B 2 Festo P BE SBO Q EN en 0702a Contents B Index B 1 B 1 Index B 3 ...
Page 156: ...B Index B 10 Festo P BE SBO Q EN en 0702a Z Zoom 1 14 ...