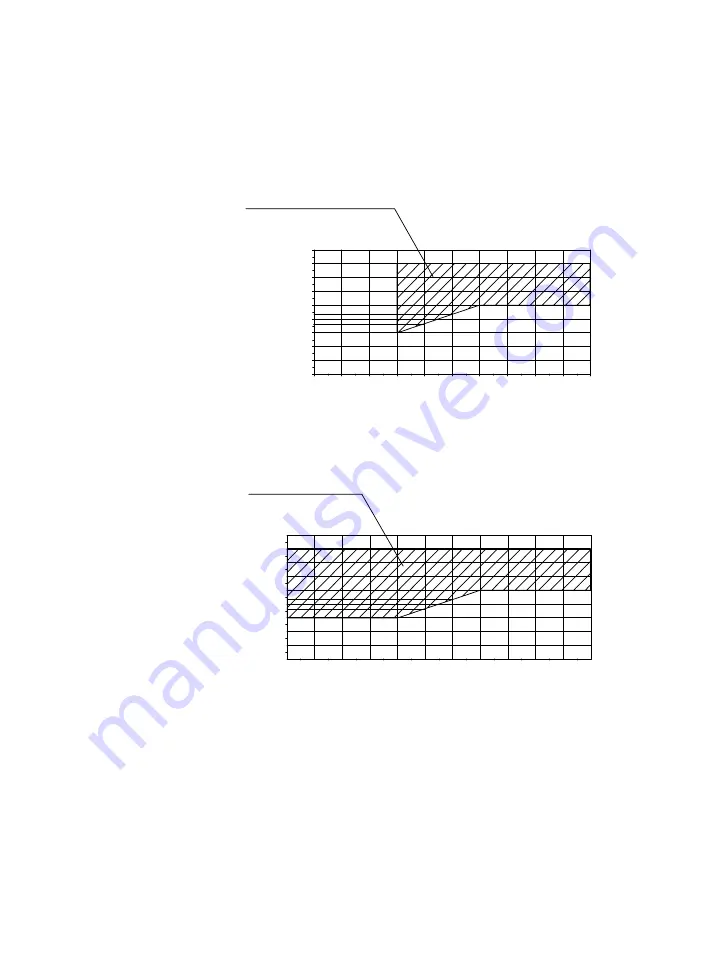
A. Technical appendix
A−6
Festo P.BE−MPA−EN en 0302NH
1
Pilot pressure 12
bar [14 bar]
2
Work range for
valves with exter
nal auxiliary pilot
air
3
Work pressure P1
[bar]
0
1
2
3
4
5
6
7
8
9
10
0
1
2
3
4
5
6
7
8
9
1
2
3
Fig.A/1:
Diagram: Pilot pressure with external auxiliary pilot air for valve plates with
Ident. code N, K, H and D
1
Pilot pressure
12/14 [bar]
2
Work range for
valves with exter
nal auxiliary pilot
air
3
Work pressure P1
[bar]
0
1
2
3
4
5
6
7
8
9
10
1
2
3
4
5
6
7
8
9
−1
0
1
2
3
Fig.A/2:
Diagram: Pilot pressure with external auxiliary pilot air for valve plates with
Ident. code M, J, B, E, G and X
Summary of Contents for VT32 Series
Page 2: ......
Page 4: ...Contents and general instructions II Festo P BE MPA EN en 0302NH ...
Page 8: ...Contents and general instructions VI Festo P BE MPA EN en 0302NH ...
Page 17: ...Summary of components 1 1 Festo P BE MPA EN en 0302NH Chapter 1 ...
Page 30: ...1 Summary of components 1 14 Festo P BE MPA EN en 0302NH ...
Page 31: ...Fitting 2 1 Festo P BE MPA EN en 0302NH Chapter 2 ...
Page 47: ...Installation 3 1 Festo P BE MPA EN en 0302NH Chapter 3 ...
Page 74: ...3 Installation 3 28 Festo P BE MPA EN en 0302NH ...
Page 75: ...Commissioning 4 1 Festo P BE MPA EN en 0302NH Chapter 4 ...
Page 93: ...Maintenance and conversion 5 1 Festo P BE MPA EN en 0302NH Chapter 5 ...
Page 122: ...5 Maintenance and conversion 5 30 Festo P BE MPA EN en 0302NH ...
Page 123: ...Technical appendix A 1 Festo P BE MPA EN en 0302NH Appendix A ...
Page 133: ...Supplementary overview of components B 1 Festo P BE MPA EN en 0302NH Appendix B ...
Page 142: ...B Supplementary overview of components B 10 Festo P BE MPA EN en 0302NH ...
Page 143: ...Index C 1 Festo P BE MPA EN en 0302NH Appendix C ...
Page 144: ...C Index C 2 Festo P BE MPA EN en 0302NH Contents C Index C 1 C 1 Index C 3 ...