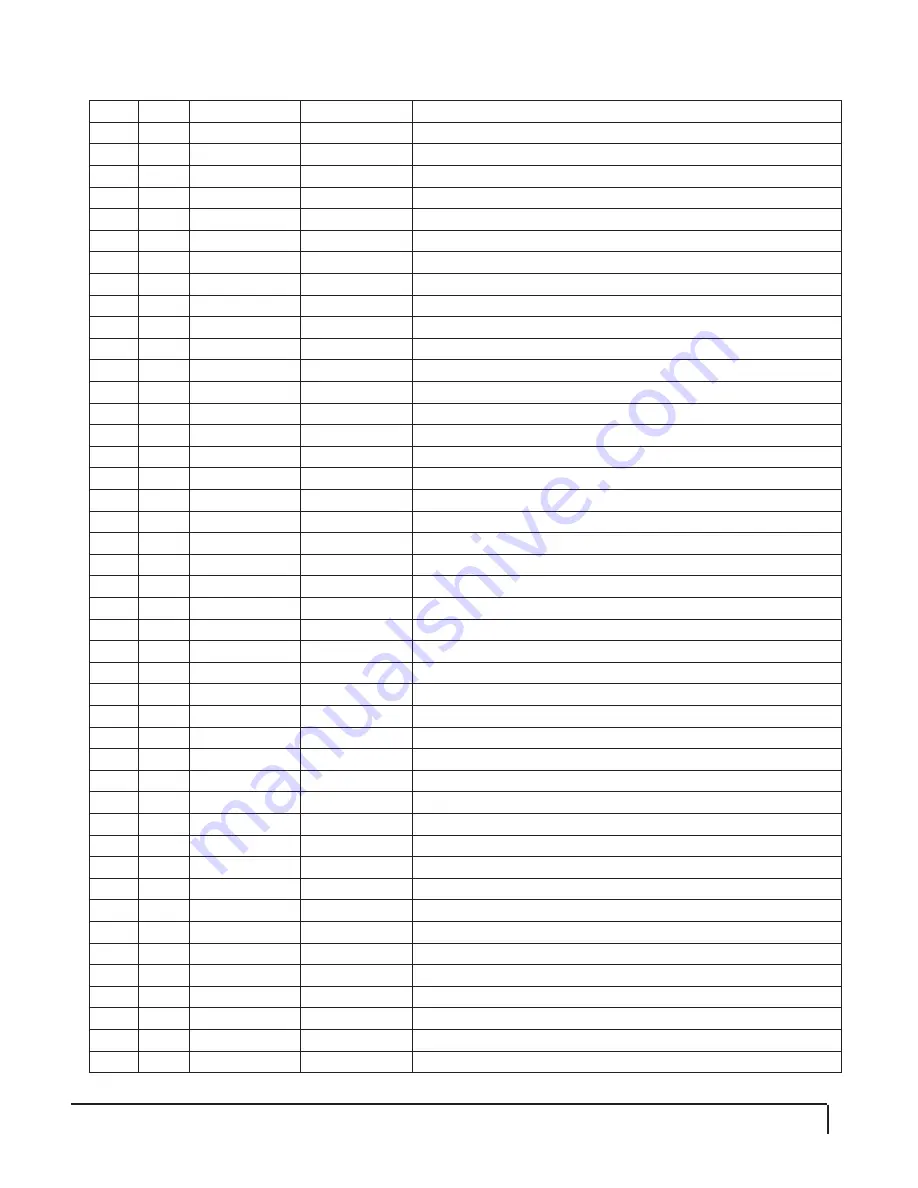
2/19/09
MR15554
19
BOX SCRAPER PARTS LIST
ITEM
QTY.
13884
13888
DESCRIPTION
1
2
07-10058
Shoulder Screw .63" X .75" (.5"-13) Zinc Plated
2
2
LAF3871
07-10163
Reversible Cutting Edge .63" X 8" Curved with Square Holes
3
10
07-10187
Tube Round 1.244" X 1.010" X .75" Hardened
4
1
07-10188
Pin Cat II Top Link 1" X 5.38" Usable
5
2
07-10189
Pin Top Link 1" X 3" Usable
6
1
13-50343
Lift Linkage Weldment
7
1
13-53235
13-52719
Main Frame Weldment
8
1
13-53236
13-52721
Scarifier Tube Weldment
9
1
n/a
13-53195
Bolt-On End Plate Right
10
1
n/a
13-53229
Bolt-On End Plate Left
11
4
LAF3857
Tube Round 1.369" X 1.125" X .75" Hardened
12
2
LAF3858
Lockout Link
13
8
LAF3859
Scarifier Lock
14
1
LAF3867
Lift Linkage Pivot Pin 1” x 8.5”
15
2
LAF3870
Tube Round 1.125” x .640” x .81"
16
2
LAF3883
Lift Linkage Bar
17
1
LAF3886
Latch Hook
18
8
LAF3896
Ripper Shank (with Shank Point Attached)
19
2
3434
Hydraulic Elbow 90° #6 Male JIC x #6 Male O-Ring
20
2
LAF4460
Hydraulic Hose .25" x 48.5” #6 Female JIC x #6 Female JIC Fittings
21
1
LAF4639
Hydraulic Cylinder 3” Piston x 6” Stroke x 1.75 Shaft
22
1
LAF9401
Split Sleeve 1.25" x 1" x 2" with Ext. Grease Groove
23
2
LAF9798
Cylinder Pin 1” x 7.5”
24
3
1047
Hex Head Cap Screw .38” x 2” Grade 5
25
1
1116
Hex Head Cap Screw ,63" x 2” Grade 5
26
varies
(14)
(26) 10150
Plow Bolt .63” x 2” Grade 8
27
10
n/a
1528
Flat Washer SAE .63” Grade 5
28
6
1706
Flat Washer SAE 1" Grade 8 Yellow
29
5
RHW5973
Machinery Bushing 2” x 1” x 0.048”
30
10
n/a
1506
Lock Washer .63” Grade 5
31
3
1837
Locknut .38” Center Dent Grade 5
32
varies
(15)
(17) 1839
Locknut .63" Center Dent Grade 5
33
10
n/a
RHW7651
Hex Nut .63” Grade 8
34
1
1793
Cotter Pin .19” x 2” Grade 2
35
7
RHW8064
Lynch Pin .44" x 1.63" Usable Large Ring
36
1
RHW8075
Hairpin Cotter Pin .12” x 2.38”
37
1
6616
Grease Zerk .25” with 28 TPI Self-Tapping
38
8
RHW8114
Rue Ring Cotter Pin .38” Shaft
39
1
RHW8207
Allen Shoulder Screw .63" x 4" Alloy
40
2
RHW8209
Cat II Pin 1.115" x 6.31" Usable Zinc Plated
41
1
RHW8216
Clevis Pin 1” x 4” Usable Zinc Plated
42
1
RHW8218
Clevis Pin .63” x 1.5” Usable Zinc Plated
43
8
RHW8225
Clevis Pin .38” x 1.5” Usable Zinc Plated
44
3
RHW8601
Locknut .5” Flanged Top Lock High Strength Grade 8
NOTE: All parts are the same as the 13888 except for those parts numbered under the other model.