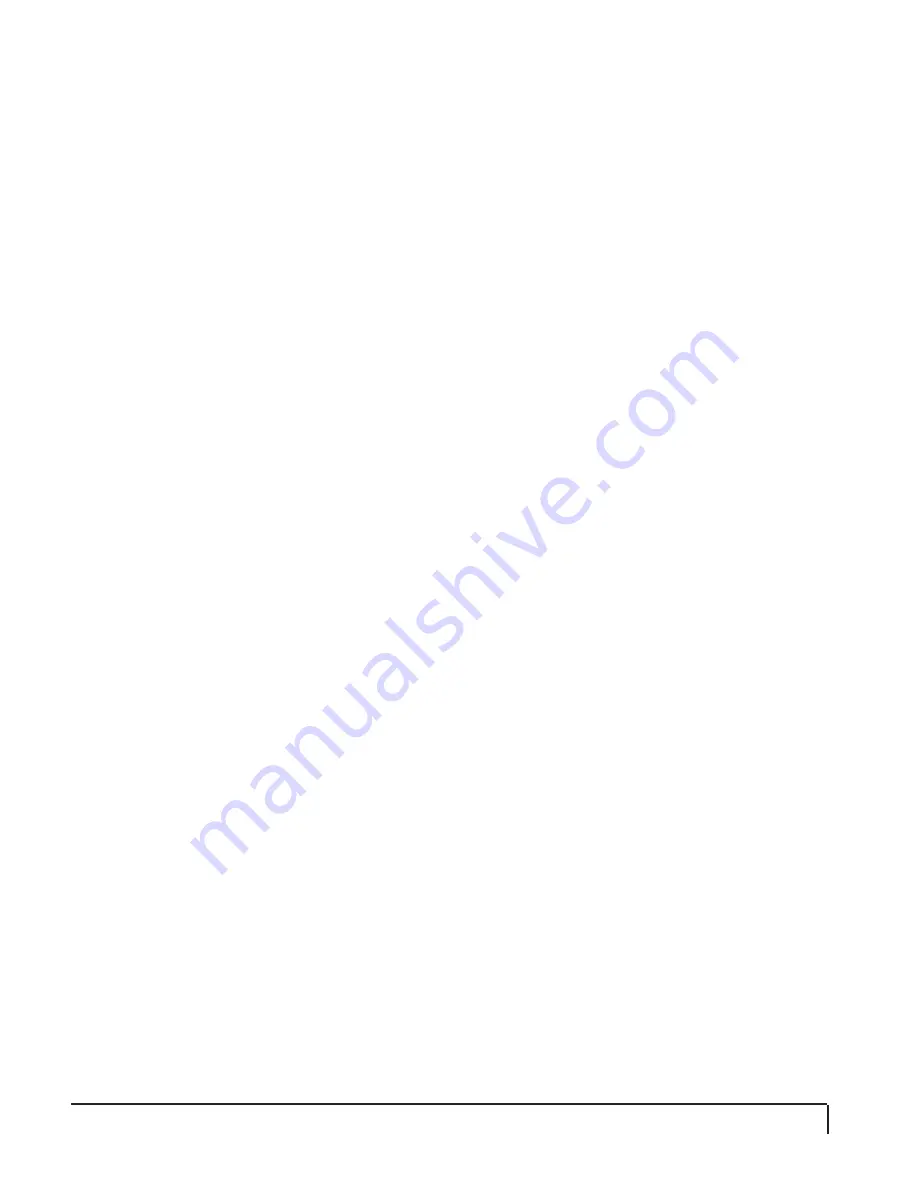
2/16/09
MR25607
13
BALE GRAPPLE MOUNTING
10.
Install the two Hydraulic Cylinders with the barrel ends down, the rod ends up, and the hose
connection ports rotated toward the center of the bucket. Secure the cylinders with the
Hydraulic Cylinder / Mounting Tube Connection Pin (Item 19) (4.75” Long) and the Hydraulic
Cylinder / Extension Tube Connection Pin (Item 20) (4.25” Long). Secure each of the two pins
with a .25” Dia. x 2” Long Grade 8 Hex Head Cap Screw (Item 21) and a .25” Dia. Center Dent
Locknut (Item 25) tightened to 12.4 ft. lbs. + or – 0.9 ft. lbs.
11.
Partially install (3) Cross Tube Mounting Plates (Item 15) on each Extension Tube by placing
(2) .5” Dia. x 5.5” Long Grade 8 Hex Head Cap Screws (Item 24) and (2) .5” SAE Grade 8 flat
washers (Item 35) on one edge of each mounting plate. These bolts should also go through
the lower two holes in the end plate of one Extension Tube and the outer two holes in the end
plate of the other Extension Tube. Secure each bolt with a .5” SAE Grade 8 flat washer (Item
35) and a .5” top lock flanged Grade 8 nut (Item 34) installed finger tight plus a half turn. Slide
the mounting plates away from the tube as far as the bolts will allow.
12.
Carefully pick up the Cross Tube (Item 18) with the tooth lugs pointed away and down from
the Extension Tube. Slide one end of the Cross Tube between the Cross Tube Mounting Plates
with (1) mounting plate against the extension tube and where the bolts have been installed on
the outer edge. With that end fully inserted, lay the other end of the Cross Tube between the
other Cross Tube Mounting Plates, also with (1) mounting plate against the other extension
tube and where the bolts have been installed on the lower edge. Securing that end with a third
.5” Dia. x 5.5” Long Grade 8 Hex Head Cap Screw, (2) .5” SAE Grade 8 flat washers, and a .5”
Dia. Locknut. Be sure to steady the Cross Tube in place while installing the third bolt so that
the Cross Tube does not slide out of position and fall. Center the Cross Tube between the two
Extension Tube, install the other three bolts, flat washers, and locknuts, and evenly tighten all
eight locknuts a small amount at a time until a torque of 84 ft. lbs., + or – 6.0 ft. lbs., is attained.
13.
Insert a Grapple Tooth (Item 16) between each pair of the tooth lugs on the Cross Tube and
secure the rear of each tooth with a .5" Dia. x 2” Long Grade 5 Hex Head Cap Screw (Item 23)
and a .5" Dia. Center Dent Locknut (Item 27) finger tightened. Pull up on the Cross Tube
enough to permit the second bolt to be installed in each tooth. Tighten all eight locknuts to 84 ft.
lbs., + or – 6.0 ft. lbs.
NOTE: If your loader’s auxiliary hydraulics are on the left loader arm, reverse the left/right
instructions
below.
14.
Install (2) .75" SAE Grade 8 flat washers (Item 33) and (1) Grapple spacer (Item 32) between
each grapple tooth, while inserting a stiffener rod (Item 36) through the upper holes in the
grapple teeth. Repeat this process for the lower holes. Install (1) .75" SAE Grade 8 flat washer
and (1) .75" top lock Grade 8 flange nut (Item 31) on each end of both stiffener rods. Tighten
each rod’s nuts to 300 ft. lbs. +/- 10 ft. lbs. making sure that the thread of the rods extend
outside of each nut.
15.
Install the four 90° Male-Male Hydraulic Elbows (Item 6) on the Hydraulic Cylinder ports. Three
of the elbows should be installed with the leg of the elbow pointed down toward the base of
the cylinder barrel. The fourth elbow (i.e. the elbow on the lower port of the right cylinder)
should be installed with the leg pointed up toward the top of the cylinder rod. For each elbow:
(1) Insert the O-ring end of the elbow into a port and fully tighten the elbow. (2) Back the elbow
off until the leg of the elbow points the correct direction. (3) Tighten the captive jamb nut to 27
ft. lbs., + or - 2.0 ft. lbs. to hold the elbow in position.
(Continued on the next page)