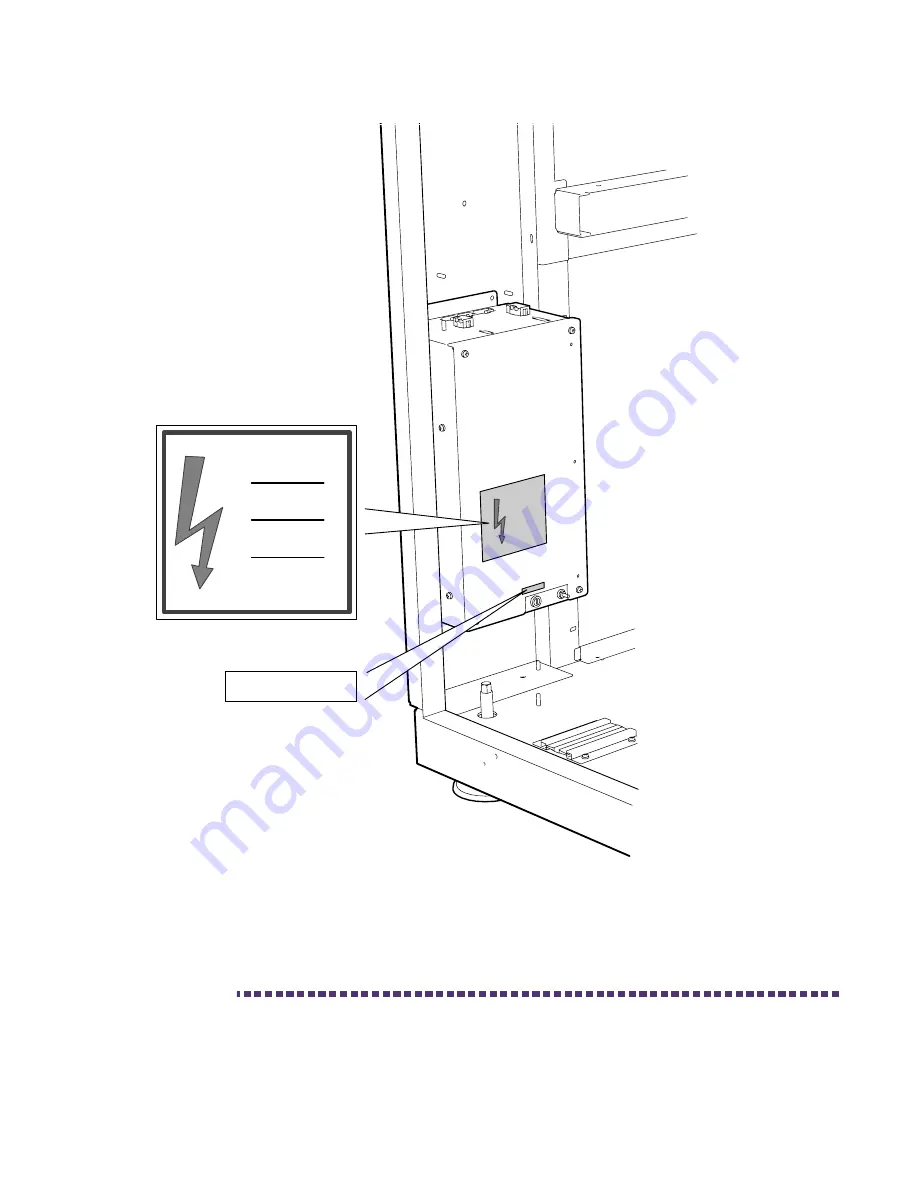
ALINTE
4
PAGE
I
NSTALLATION
G
UIDE
2-11
Figure 2.9 Interlock box: high-tension warning label
2.2.7 Interlock Warning Labels
Figure 2.10 on page 2-12
(entry level) and
Figure 2.11 on page 2-13
shows the areas of laser beam risk to the engineer when the inter-
locked covers are opened and the interlocks are defeated.
Hochspannung
haute tension
Precaucion!
caution!
orsicht!
high tension
Attention!
V
Pre
é
ó
alta tensio
ó
n
T2A H 250V
Summary of Contents for alinte4page
Page 1: ......
Page 12: ...PRELIMINARIES...
Page 29: ...ALINTE4PAGE INSTALLATION GUIDE 2 7 Figure 2 5 Autofeeder elevator warning label...
Page 40: ...2 18 SAFETY ON THE ALINTE4PAGE Figure 2 13 Location of interlock covers alinte4page SAL 2 1...
Page 48: ...2 26 SAFETY ON THE ALINTE4PAGE...
Page 56: ...3 8 UNPACKING AND HANDLING...
Page 98: ...4 42 INSTALLING ALINTE4PAGE EQUIPMENT AND SOFTWARE Figure 4 32 Removing transit fixing view 2...