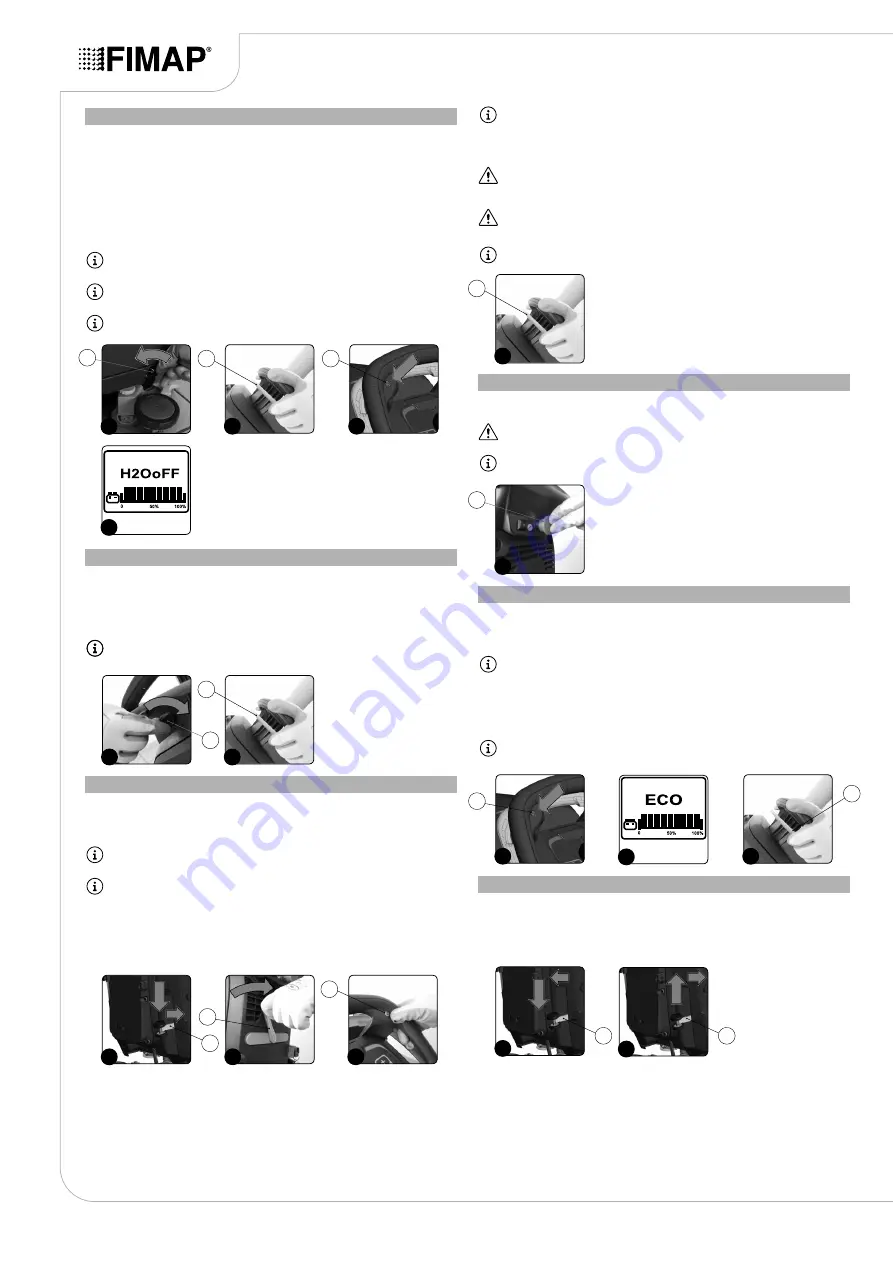
ADJUSTMENT OF THE DETERGENT SOLUTION FLOW
To adjust the flow of detergent solution during work, proceed as follows:
1. Make sure the detergent solution tap is fully open, rotating the knob (1) in the direction of
the arrow (
Fig.1
). As the knob is rotated, the flow of detergent in the machine water circuit is
increased.
2. By pushing the dead man's lever (2) the brush motor will start operating and the solenoid valve
will distribute detergent solution to the brush (
Fig.2
).
3.
During the first few meters check that the amount of solution is sufficient to wet the floor, but not
excessive to exit the splash guard.
4. If the amount of chemical that comes out is not suitable, it can be controlled via the knob (1) on
the rear left-hand side of the machine (
Fig.1
).
NB
:
If you wish to stop the delivery of detergent solution completely when working, press the
button (3) on the control handlebars (
Fig.3
).
NB
:
When the button (3) on the control display is pressed, the word “H2O STOP” will appear
intermittently(
Fig.4
).
NB
:
To reactivate the delivery of the detergent solution, press the button (3) again (
Fig.3
).
REGULATING THE FORWARD SPEED
This machine is equipped with electronic traction control. To adjust the forward speed during work,
proceed as follows:
1. Turn the main switch (1) to "I", making a quarter turn of the key in the direction of the arrow
(
Fig.1
).
2. Press the dead man's levers (2) underneath the control handlebars (
Fig.2
).
NB
:
The forward speed of the machine can be adjusted by varying the pressure on the dead
man's lever (2). The more it is pressed, the more the forward speed will increase.
REVERSE
This machine is equipped with electronic traction control. To reverse, proceed as follows:
1. Raise the brush head body and fully depress the "BRUSH HEAD CONTROL" pedal (1) at the
rear of the machine (
Fig.1
).
NB
:
to lock the brush head in the raised position, depress the pedal (1) fully and then move it
towards the right-hand side of the machine (
Fig.1
).
NB
:
if the brush head body is left in contact with the floor, the gearmotor will continue
functioning but the solenoid valve will stop dispensing detergent solution on the brush.
2. Raise the squeegee body and turn the squeegee control lever (2) in the direction of the arrow
(
Fig.2
). The lever is located on the back of the machine.
3. Press the “REVERSE ACTIVATION - DEACTIVATION” button (3) on the control handlebars
(
Fig.3
).
NB
:
As soon as the button (3) is pressed, the word “BACK” will appear on the control display
(
Fig.4
).
4. Activate the dead man's levers (5) on the handlebars (
Fig.4
) to start moving the machine in
reverse mode.
WARNING
: the reverse speed is lower than the forward speed to comply with current health
and safety standards. If the potentiometer is adjusted while reversing, the adjustment of the
forward speed will be automatically changed.
WARNING
: it is impossible to reverse if the squeegee body touches the floor. In order to
reverse, lift the squeegee body from the floor using the relevant lever on the back of the
machine.
NB
: to disable reverse movement, press the button (4) on the control handlebars again.
EMERGENCY BUTTON
This machine is equipped with an emergency switch. To activate it, just press the button (1) on the
back of the control handlebars (
Fig.1
).
WARNING
: this control interrupts the electrical circuit between the batteries and the machine
system.
NB
: after stopping and resolving the problem, turn the key to “0”, set the button (1) to the
standard position and turn the key to “I” to resume the work.
ECO MODE
This machine has an Eco-Mode function for reducing the noise generated by the vacuum motor, and for
reducing the energy used by the machine.
To activate or deactivate this function, just press the button (1) on the instrument panel for at least
three seconds (
Fig.1
).
N.B.
: When the Eco-Mode function is active, the word “ECO” will flash on the control display
(
Fig.2
).
Just press the button (1) on the control panel to deactivate the "Eco-Mode" function (
Fig.1
).
If the dead man's lever (2) is released when performing a scrubbing with drying operation in Eco-
Mode (
Fig.3
), both the traction motor and the brush motor, along with the solenoid valve, will stop
working, while the vacuum motor will continue to function until it is raised off the floor.
NB
:
To recommence work, simply press the dead man's lever (2) and the traction motor will
start immediately; the brush motor; the solenoid valve.
EXTRA BRUSH HEAD PRESSURE
This machine can increase the pressure exerted on the brush during the work cycle. To do this:
1. Check that the brush head body is in contact with the ground; if not, detach the "BRUSH HEAD
CONTROL" pedal (2) at the rear of the machine from the plate retainer (
Fig.1
).
2. Raise the brush head pedal and engage it in the “EXTRA PRESSURE” position (
Fig.2
).
18
1
1
2
2
4
4
1
1
2
3
2
3
1
4
1
1
1
2
2
3
3
1
1
2
3
2
1
1
2
1