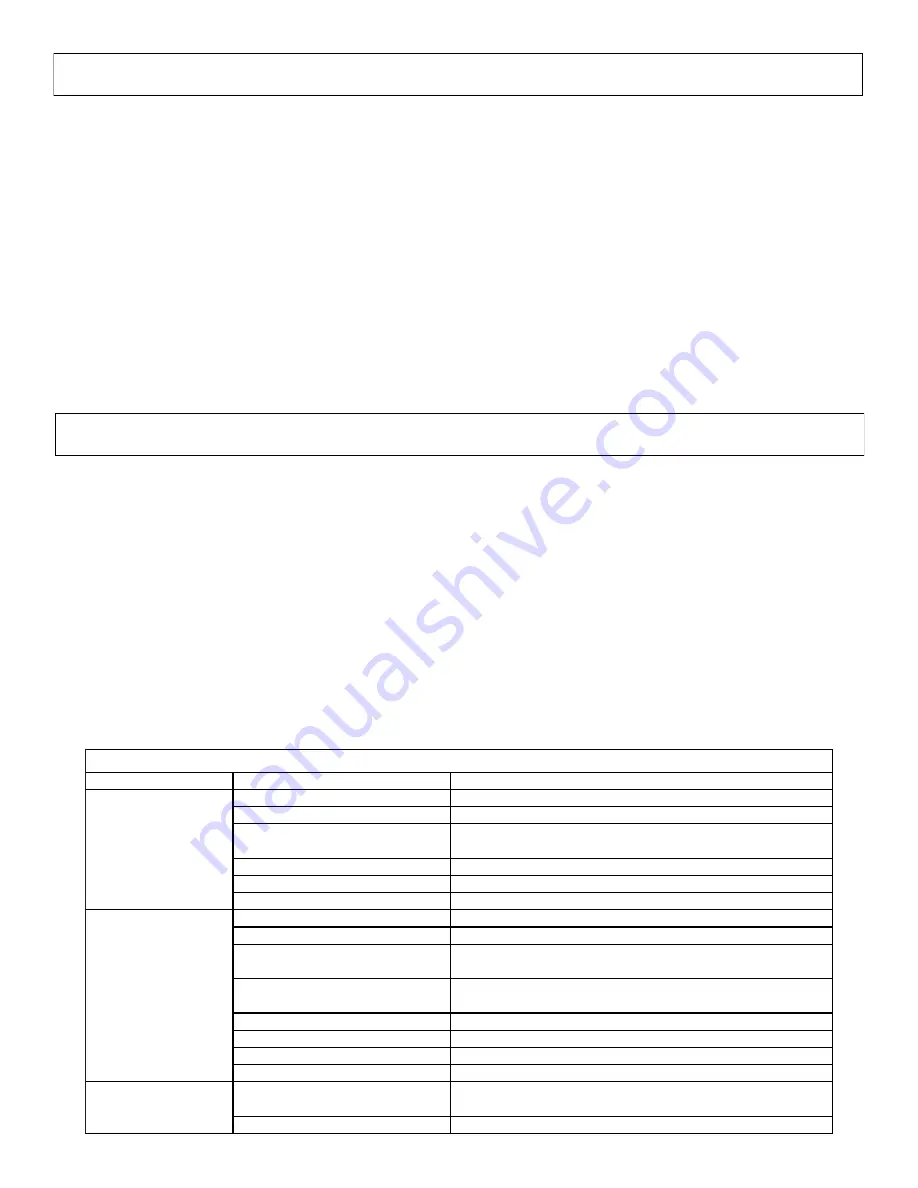
Page 11
1. Use a pressure relief device on the discharge side of the
pump to prevent damage from pressure buildup when the
pump discharge is blocked or otherwise closed and the pow-
er source is still running.
2.
WARNING:
Never pump flammable or explosive fluids such
as gasoline, fuel oil, kerosene, etc. Never use in explosive
atmospheres. The pump should be used only with liquids
compatible with the pump component materials. Failure to
follow this warning can result in personal injury and/or prop-
erty damage and will void the product warranty.
3. Never pump acids (i.e. acid fertilizer) with Super Rollers!
4. Never run the pump faster than maximum recommended
speed.
5. Never pump at pressures higher than the maximum recom-
mended pressure.
6. Never pump liquids at temperatures higher than the recom-
mended maximum temperatures (140°F/60°C).
7. Make certain that the power source conforms to the require-
ments of your equipment.
8. Provide adequate protection in guarding around the moving
parts such as the shaft and pulleys.
Roller Pump General Safety Information
9. Disconnect power before servicing.
10. Release all pressure within the system before servicing any
component.
11. Drain all liquids from the system before servicing any com-
ponent.
12. Check all hoses for weak or worn condition before each use.
Make certain that all connections are tight and secure.
13. Periodically inspect the pump and the system components.
Perform routine maintenance as required.
14. Never operate a gasoline engine in an enclosed area. Be
sure the area is well ventilated.
15. Use only pipe, hose and fittings rated for the maximum psi
rating of the pump.
16. Never use pump for pumping water or other liquids for hu-
man or animal consumption.
WARNING: Never pump corrosive or abrasive liquids as these
will cause rapid wear or deterioration of the body, rotor, shaft and
seals in the pump. The pump should be used on with liquids
compatible with pump component materials. Never exceed maxi-
mum specified rpm and pressure. Never run pump dry. Failure to
follow this warning will void the product warranty.
Priming the Pump:
To help prime the pump, keep the inlet or suction line as short as
possible with a minimum of bends, elbows and kinks. Make sure
all connections are tight and do not leak air. Make sure line
strainer is free of debris. If pump does not self-prime, disconnect
suction hose, fill with water and reconnect to liquid source. Often
a squirt of oil into the ports of the pump will seal clearance and
help priming.
Care of the Pump:
Proper care and maintenance will keep your pump wear at a
minimum and will keep it running smoothly and trouble-free for a
long time.
Roller Pump Operation & Maintenance
Flush the Pump After Each Use
One of the common causes of faulty pump performance is
“gumming” or corrosion inside the pump. This prevents
rollers from moving freely in their rotor slots. Flush the
pump with a solution that will neutralize liquid pumped, mix
according to manufacturer’s directions.
To Prevent Corrosion:
After cleaning pump as above, flush it with a 50-50 solution of
permanent-type automotive antifreeze (containing a rust inhibitor)
and water. A rust inhibitor can also be squirted into the ports of
the pump. Turn shaft several times to draw protective liquid
through pump and coat entire inner surface. Drain pump and
plug ports to keep out air during storage. For short periods of
idleness, noncorrosive liquids may be left in the pump, but air
must be kept out. Plug ports or seal port connections.
Symptom
Probable Cause(s)
Corrective Action
Leak in suction line
Check hose and fittings for leaks and correct
Obstruction in suction line
Inspect hose for debris or loose inner liner in hose
Suction hose sucked to
bottom or side of tank
Cut a notch or "V" in end of suction hose
Rollers stuck in pump
Disassemble pump and inspect rollers
Pump seals leaking air
Replace seals
Clogged suction strainer
Check strainer and clean it regularly
Kinked or blocked suction hose
Inspect suction hose and repair as necessary
Air leak in inlet side plumbing
Check hose and connections for leaks
Use pipe joint sealant and retighten connections
Relief valve setting too low
or weakened spring
Check relief valve and correct setting
Faulty Gauge
Replace gauge
Pump seals leak air
Replace seals
Nozzle orifices worn
Replace nozzles
Pump worn
Repair pump
Corrosion (rust), scale or residue
Loosen endplate bolts. Squirt oil into ports to help free rotor.
Retighten bolts.
Solid object lodged in pump.
Disassemble pump and remove objects
Troubleshooting
Pump Does Not Prime
Loss of Pressure
Pump will not turn