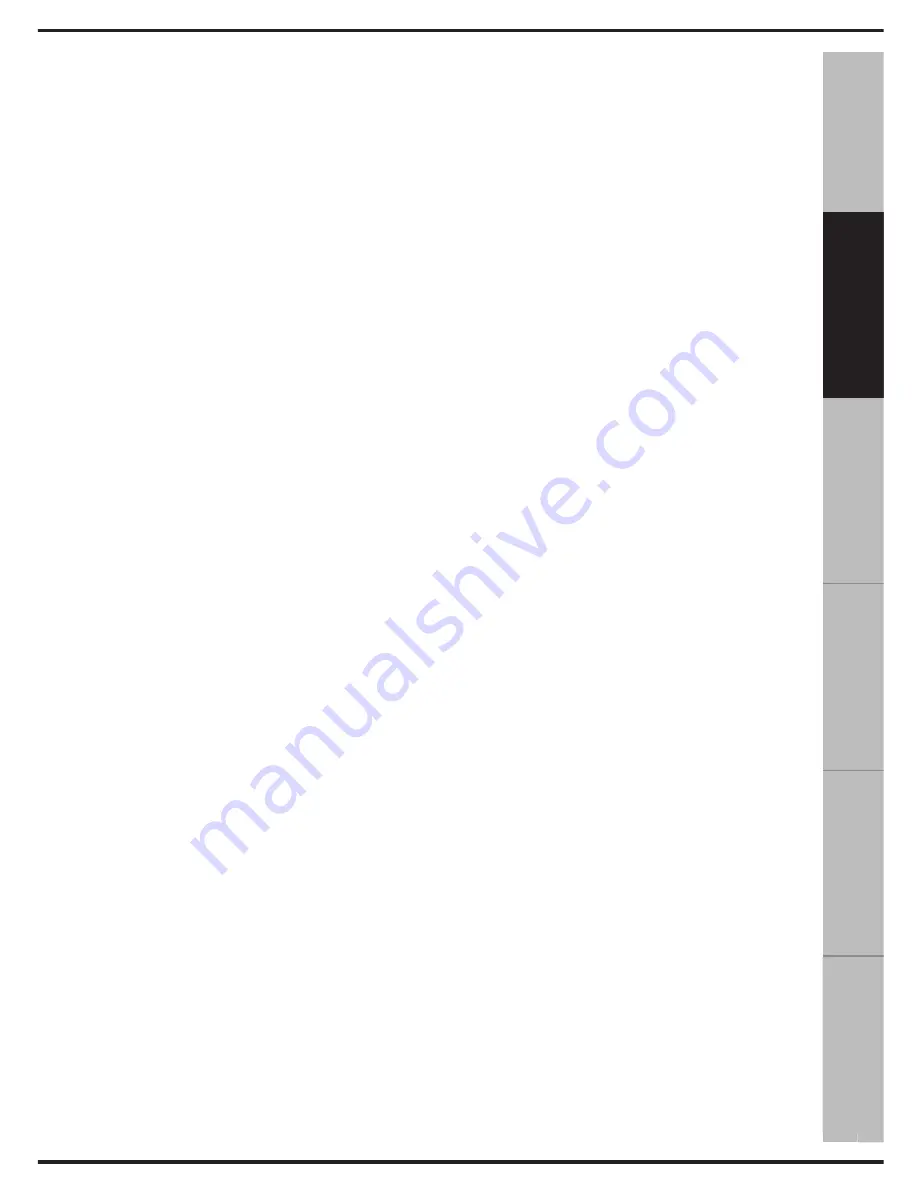
17
IT
AL
IA
NO
1. MIG WELDING
In MIG welding, a metal electrode consist-
ing of a wire is melted in a weld pool. The
wire electrode is continuously fed by a
welding torch at a constant and controlled
speed. The torch is connected to the posi-
tive pole, while the ground cable is con-
nected to the negative pole. When the wire
is fed and touches the workpiece, an elec-
tric arc is produced. The arc melts the wire
which is then deposited on the workpiece.
MIG welding uses a special metallic wire as
an electrode and an inert gas (CO2,
CO2/Argon mix or pure Argon) to protect
the weld pool. Welding with continuous
feeding of the wire allows using a higher
current density than that used in welding
with coated electrodes. This allows increas-
ing the weld penetration and reducing the
number of passes required to fill the joint.
The welding unit consists of a DC power
source, a wire feeder, a torch and a ground
clamp. Each welder has two switches (
13
and 14 of Fig. 1
) used to regulate the weld-
ing current (the
TM 230
and
TM 260
models
only have Switch
13
for this purpose) and
two potentiometers (
1 and 9 of Fig. 1
) to
respectively regulate the welding time and
wire speed. The welding current and wire
speed must be regulated taking into consid-
eration the thickness of the workpiece to be
welded. Thicker pieces require a higher
welding current and higher wire speed. The
wire speed can be adjusted during welding
to obtain better results.
IMPORTANT:
The welding machine must
only be used by trained personnel.
All the TM welding machines are wire
welders produced with advanced technolo-
gy that makes them extremely reliable. In
fact, minimal maintenance is required to
ensure long life of the equipment without
any problems.
The user-friendliness of the welding
machine allows for rapid interchangeability
of operators.
For an excellent welding performance, it is
recommended to use a welding spray. This
will increase the sealing capacity and
reduce weld spatter.
2. POWER SUPPLY CONNECTION
Before connecting the machine, check the
voltage, number of phases and power fre-
quency. The admissible power supply volt-
age
is
reported
in
the
“Technical
Specifications” section of this manual and
in the machine’s rating label. Make sure
there is sufficient power to run the
machine. The “Technical Specifications”
section of this manual contains information
on the type of line protection devices to
use. The machine comes with a specific
power cord which should not be extended.
If an extension cord is necessary, use one
that has the same or a larger cross section
than the machine’s cord depending on the
length of the cord.
3. OUTPUT CONNECTIONS
The welding cables are connected with a
quick coupling system that uses special con-
nectors. The ground cable must first be con-
nected to its connector (
15 or 16 of Fig.1
) and
then the torch cable (
19 di Fig. 1
). This con-
nector also allows connecting the electrical
contacts of the torch and the hose that carries
the welding gas to the torch.
Refer to the following sections for more infor-
mation on the connections to be carried out
before proceeding with the welding.
ES
PA
ÑO
L
FR
AN
ÇA
IS
DE
UT
SC
H
EN
G
LI
SH
РУ
СС
КИ
Й