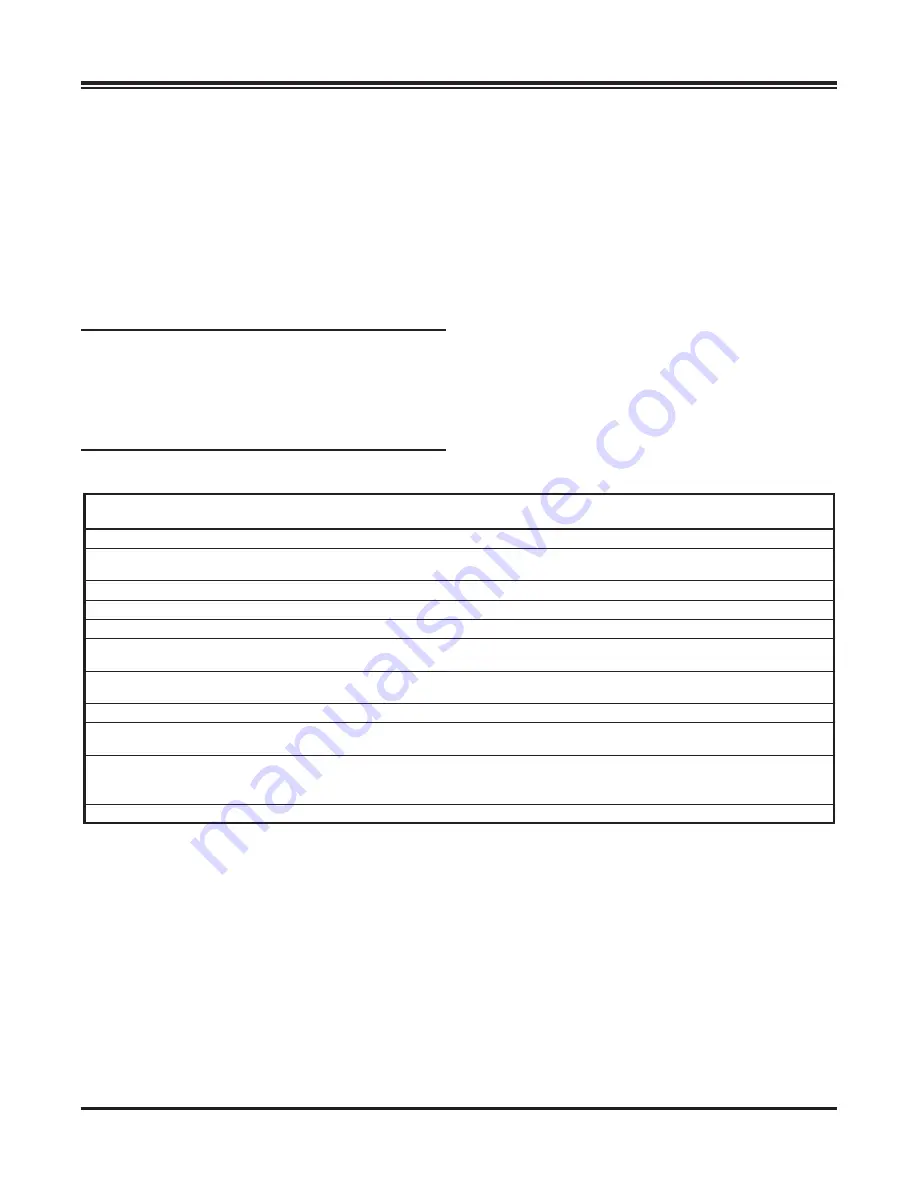
Lit. No. 94196/94197/94198, Rev. 05
16
November 1, 2010
OPERATING THE SPREADER – CAB CONTROL
DIAGNOSTIC INDICATOR LIGHT AND
AUDIO BEEP
The diagnostic indicator light located to the right of
the START/BLAST button remains dark unless a
problem with the motor or wiring is detected. The light
will
fl
ash in coordination with an audio beep a number
of
fl
ashes/beeps in a row, pause, then repeat. Count
the
fl
ashes/beeps to determine the nature of the
malfunction and refer to diagnostic chart below.
NOTE: Always close the lids on the hopper to
prevent moisture buildup. Do not let spreader sit
idle with material in the hopper for an extended
period of time. This can cause material to
compact, reduce or stop the
fl
ow of material and
cause permanent hopper body deformation.
# of
Flashes/Beeps
Problem
Possible Cause
0
No Error
–
1
No Communication
Loss of communication between spreader module and cab control. Vehicle
cable assembly is disconnected or faulty.
2
Empty Hopper
Spreader is empty or material has bridge in the hopper.
3
Conveyor Over Current Over 70 amps for up to 3 seconds. Conveyor Chain is stalled.
4
No Power
Battery fuse is blown or vehicle cable assembly is disconnected or faulty.
5,8
Over Temp
Motor is OFF due to spreader module overheating from high-current draw
over a long period of time.
6
Battery Saver
Reduced spreader performance due to vehicle voltage drop. Spreader will
function at reduced output until vehicle voltage increases.
7
Spinner Over Current Over 32 amps for up to 3 seconds. Spinner is stalled.
9
Sander Reset
Module came out of reset. Momentary loss of power. Restart unit, check
power wiring.
10
Cool Down
If the unit gets more than 5 faults with each fault starting within 60 seconds
from the last, it will not start for 60 seconds from the last fault to allow the unit
to cool.
11
Low Battery
Low battery voltage or poor electrical connection of vehicle cable assembly.