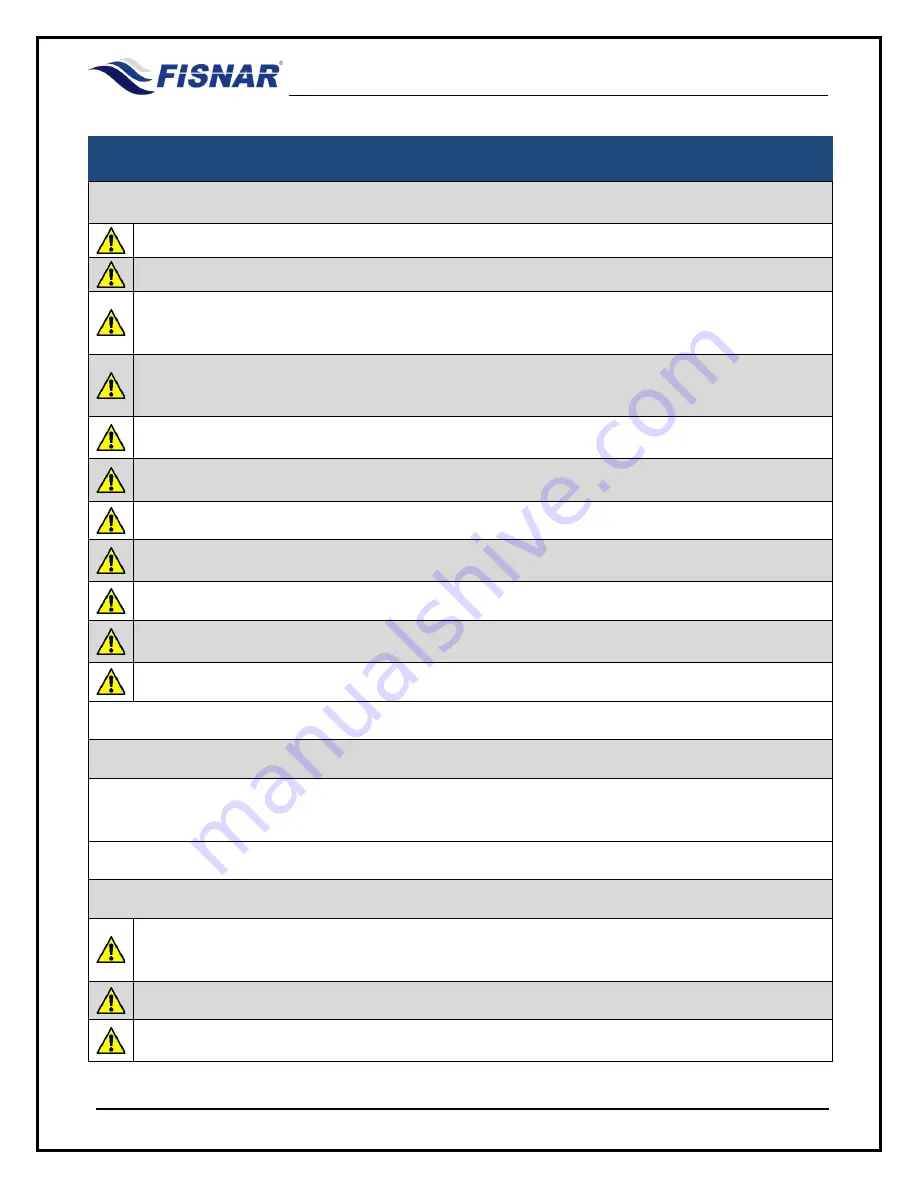
F1300N.2 Rotary Table Operating Manual
© 2022 Fisnar
- 4 -
F1300N.2 Rev 01
General Precautions
Do not operate the machine in excess of its maximum ratings / settings.
Make sure the machine is connected to a properly grounded power source.
Make sure that the input air supply is clean and dry. A 5 micron air filter/regulator
(item number 560567) is supplied and recommended to use, so as to ensure the
input air supply is clean and dry.
If Cyanoacrylates adhesives or other moisture sensitive fluids are being used,
an inline coalescing filter (item number 560779C) must be installed to maintain
dispensing system performance.
The fluid being dispensed may be toxic and / or hazardous. Refer to the Material
Safety Data Sheet for proper handling and safety precautions.
Do not smoke or use near an open flame when flammable materials are being
dispensed.
Do not expose the machine directly to sunlight.
Avoid cleaning the machine with aggressive solvents – neutral detergents are
preferred.
Do not touch any moving parts while the rotary table is running.
Loading and unloading of parts must be done when the rotary table is not
moving.
Changing of tooling must be done with the power source disconnected.
EU & UK Safety Requirement
To meet the conformity requirements of the European Community (CE) Machinery
Safety Directive (2006/42/EC) or UK (UKCA) Machinery (Safety) Regulations 2008 this
machine must be placed in an appropriate safety enclosure prior to production use.
F1300N.2 Malfunction
If the machine malfunctions, shut down the machine immediately. This can be
done by either pushing the power switch at the back of the unit into the off
position or disconnecting the power cord.
Isolate pneumatic air supply to the controller.
Identify the cause of machine malfunction and fix accordingly before switching
back on.
SAFETY
Summary of Contents for F1300N.2
Page 1: ...F1300N 2 Rotary Table Operating Manual info fisnar com www fisnar com ...
Page 55: ...F1300N 2 Rotary Table Operating Manual 2022 Fisnar 55 F1300N 2 Rev 01 SPARE PARTS LIST ...
Page 57: ...F1300N 2 Rotary Table Operating Manual 2022 Fisnar 57 F1300N 2 Rev 01 MACHINE DRAWING ...
Page 59: ...F1300N 2 Rotary Table Operating Manual 2022 Fisnar 59 F1300N 2 Rev 01 TURNTABLE DRAWING ...
Page 63: ...F1300N 2 Rotary Table Operating Manual 2022 Fisnar 63 F1300N 2 Rev 01 NOTES ...