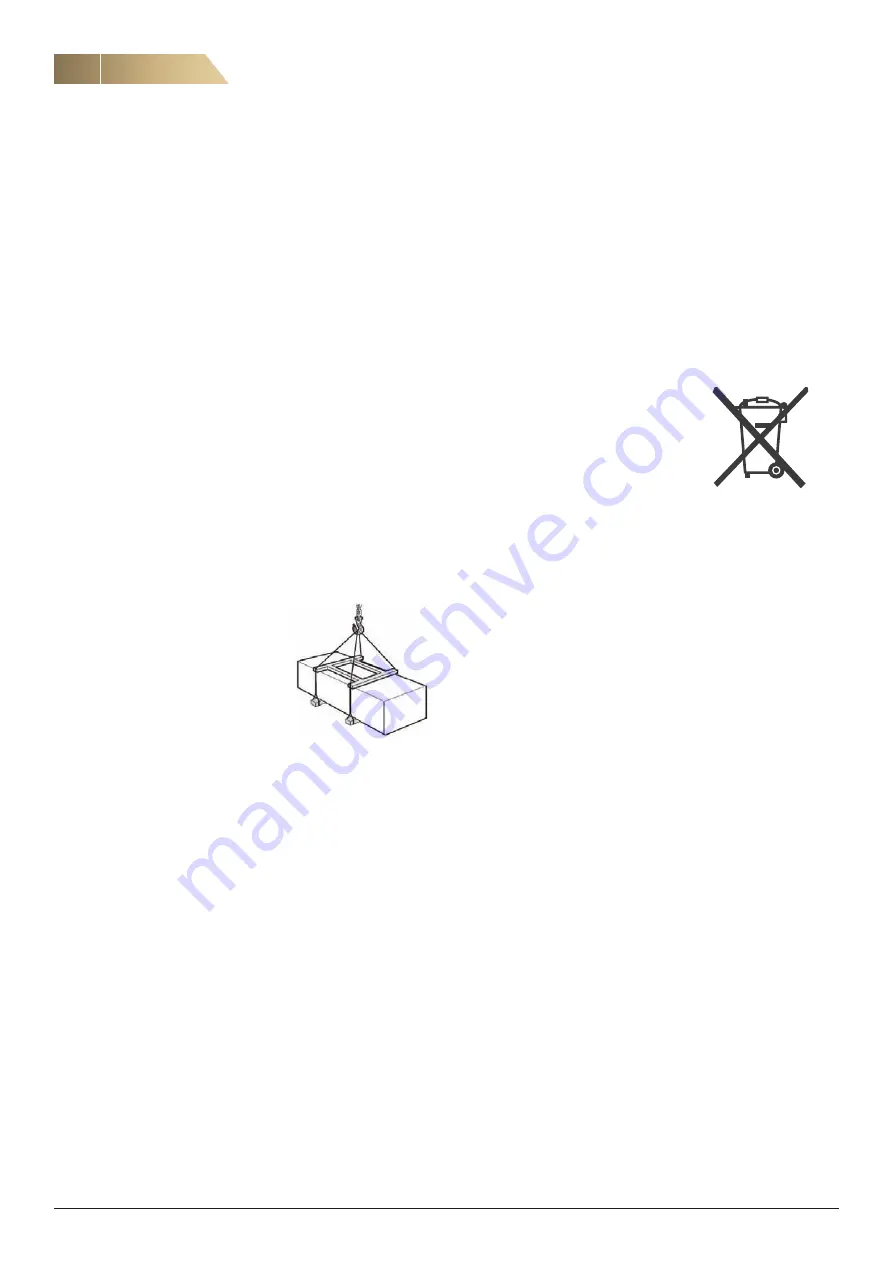
eCO Premium™ - Installation & Maintenance
4
FläktGroup DC_9604GB_20190327_R6
Specifications are subject to alteration without notice
6. GOODS RECEIPT
Each product is carefully inspected before shipping. On receipt of
goods, it is recommended that products are checked to confirm
that they have not suffered damage during transport. If damage
is found, then please report this issue to the transport forwarding
agent, who is responsible for any damage incurred during trans-
port. The usual method of packing is for products to be loaded
onto pallets and then fastened to them by means of straps. A
protective film is also generally added to minimise water ingress.
Alternatively, product may sometimes be contained with a self-
supporting cardboard carton, which is again fastened securely to
a pallet.
HANDLING AND OFF-LOADING
Before off-loading products, please ensure that the means of
transport/ lifting is suitable to accommodate to the required
weight and size capacity. It is recommended that where product
is shipped on a pallet, a forklift truck should be used.
In accordance with the 89/391/CEE
standard (and associated updates),
manual lifting is only admissible up to
a maximum weight of 20 Kg, between
floor and shoulder level.
Lift unit into position using spreaders,
ensuring you have the appropriately
rated equipment for the weight of the
unit.
7. EQUIPMENT START-UP
Before operating our product, the following checks must be made:
• Ensure that product inlet/outlet connections are free from
obstruction
• Check that all product components are securely fastened in
their associated sealing gaskets
• Manually rotate each fan impeller to ensure that it does not rub
or bind onto the fan scroll
• Ensure that any inspection or access doors are closed.
CAUTION:
If fan inlets or discharges are not connected to duct work, please
ensure that suitable protection guards are fitted before the unit is
started. Check that electrical connections have been made correct-
ly, especially the earth connection.
IMPORTANT:
Electrical connections must be made by qualified personnel.
9. DISPOSAL
Please ensure that products are dismantled
and disposed of by qualified personnel in an
environmentally friendly way, in accordance
with all relevant local and national regulations
in force.
GOODS RECEIPT, HANDLING, EQUIPMENT START-UP, DIS- AND RE-ASSEMBLY, DISPOSAL
8. DISASSEMBLY AND RE-ASSEMBLY
Before starting any disassembly or re-assembly operation, please
ensure that the product is isolated from its mains electrical sup-
ply, in order to ensure that fans cannot be run. As disassembly
and re-assembly are not part of routine maintenance, these
should be carried out by qualified personnel.
Summary of Contents for eCO Premium
Page 1: ...INSTALLATION AND MAINTENANCE MANUAL eCO PREMIUM...
Page 47: ......