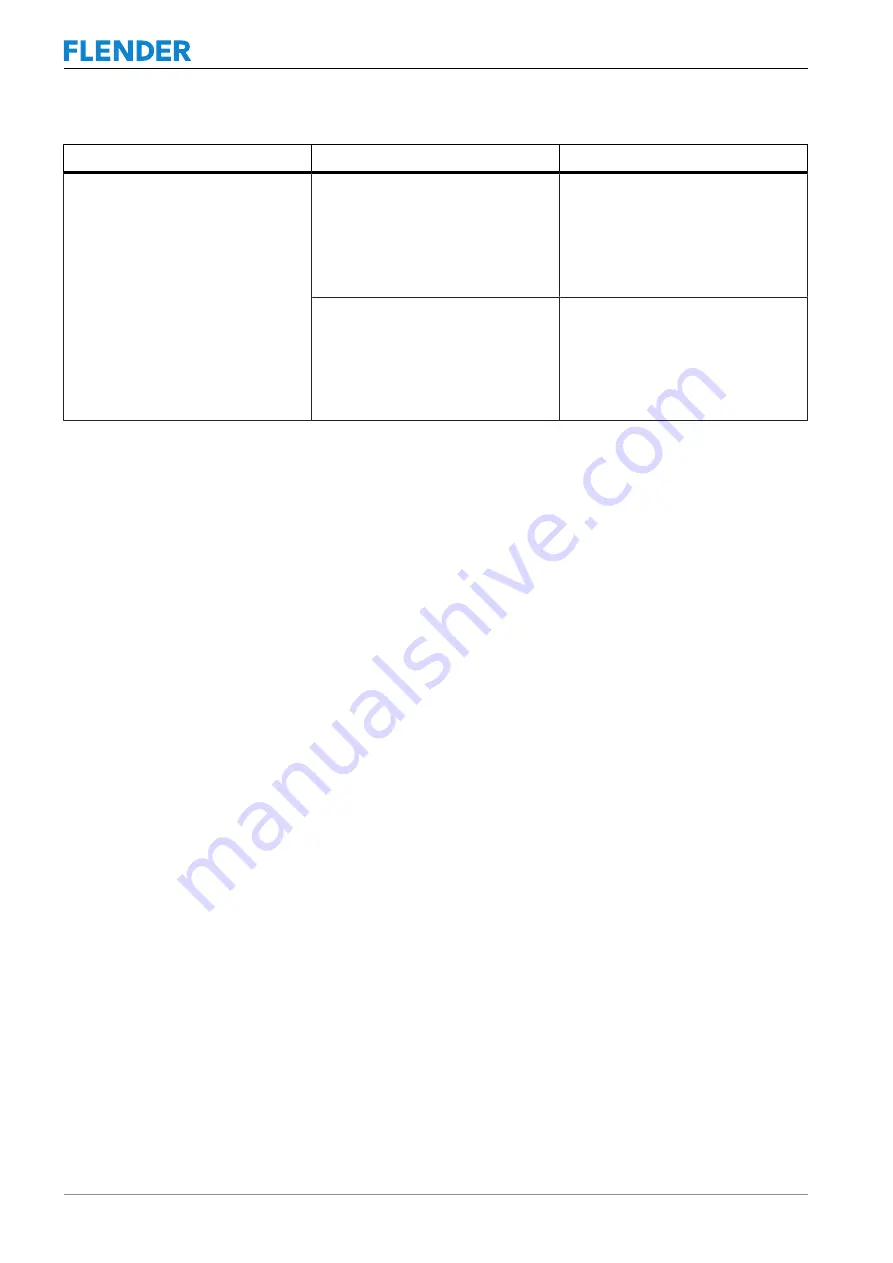
Operation
7.2 Fault - causes and correction
M3302-01en
Edition 09/2022
43
Fault
Cause
Rectification
Presence of vibration
Incorrect assembly of the coupling.
Check the possible causes given in
sections Assembly-related causes
(Page 43) and Specific assembly-re-
lated and maintenance-related causes
(Page 44).
Reassemble the coupling in accord-
ance with these instructions.
Please observe all the stipulations and
requirements given in chapter Assem-
bling (Page 27).
Incorrect maintenance of the coupling.
Check the possible causes given in
sections Maintenance-related causes
(Page 44) and Specific assembly-re-
lated and maintenance-related causes
(Page 44).
Please observe all the stipulations and
requirements given in chapter Mainten-
ance (Page 47).
Table 7-1:
Table of faults
7.2.2.2
Possible causes
7.2 Fault - causes and correction
7.2.2.2.1
Unsuitable coupling
7.2 Fault - causes and correction
• Important information on the description of the drive unit and the environment were not
available when the coupling was chosen.
• System torque too high and/or torque dynamics not permissible.
• System speed too high.
• Application factor not selected correctly.
• Chemically aggressive environment not taken into consideration.
• Coupling not suitable for the ambient temperature.
• Diameter and/or assigned fit of the finished bore not permissible.
• Width across corners of the parallel keyways greater than the width across corners of
the parallel keyways in accordance with DIN 6885/1 for the maximum permissible bore.
• Shaft-hub connection incorrectly sized.
• Maximum permissible load conditions not taken into consideration.
• Maximum permissible overload conditions not taken into consideration.
• Dynamic load conditions not taken into consideration.
• Coupling and the machine and/or drive train form a critical torsional, axial or bending vi-
bration system.
7.2.2.2.2
Assembly-related causes
7.2 Fault - causes and correction
• Damaged parts installed.
• Shaft diameter outside the stipulated tolerance range.
• Coupling parts interchanged and hence not assigned to the specified shaft.
• Stipulated locking elements to prevent axial movements not installed.
• Stipulated tightening torques not adhered to.
• Screws inserted dry or greased.
Summary of Contents for ELPEX-S
Page 6: ...Table of contents 6 Edition 09 2022 M3302 01en ...
Page 8: ...List of tables 8 Edition 09 2022 M3302 01en ...
Page 10: ...List of figures 10 Edition 09 2022 M3302 01en ...
Page 14: ...Introduction 1 4 Copyright 14 Edition 09 2022 M3302 01en ...
Page 22: ...Description 22 Edition 09 2022 M3302 01en Structure ...
Page 38: ...Assembling 5 3 Aligning the coupling 38 Edition 09 2022 M3302 01en ...
Page 40: ...Commissioning 40 Edition 09 2022 M3302 01en ...
Page 46: ...Operation 7 2 Fault causes and correction 46 Edition 09 2022 M3302 01en ...
Page 56: ...Service and support 9 1 Contact 56 Edition 09 2022 M3302 01en ...