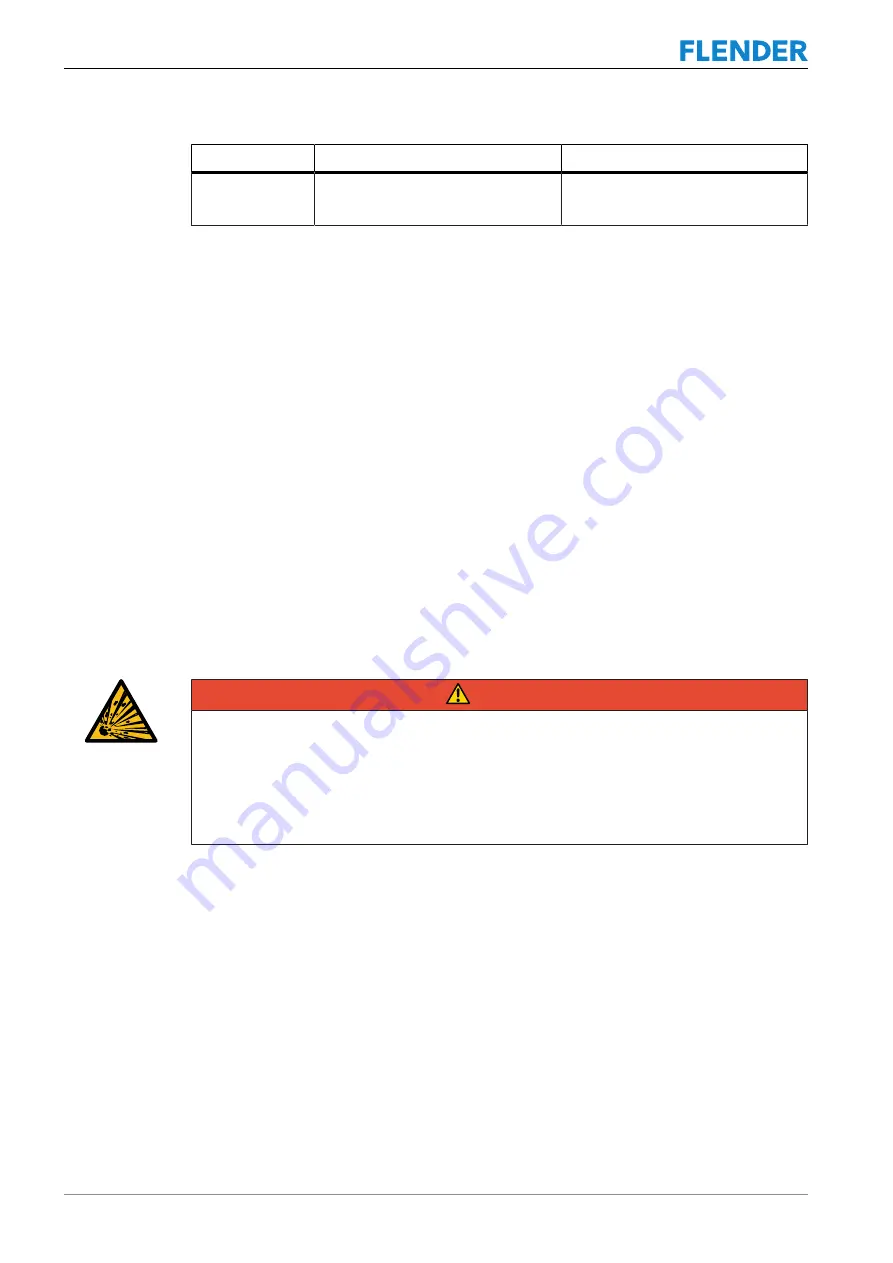
Maintenance
8.2 Maximum permissible wear
48
Edition 09/2022
M3302-01en
Model
Initial maintenance
Follow-up maintenance
EST
3 months after commissioning
1)
Every 12 months
1)
Table 8-1:
Maintenance intervals
1)
According to the Explosion Protection Directive, need only be inspected if a failure of the rubber disk
element 5 (5) and/or 6 (6) and shutdown of the drive as a result of this failure could give rise to a risk of
explosion. We recommend that the wear is checked regularly.
Shorter maintenance intervals
If necessary, set shorter maintenance intervals depending on actual wear.
8.2
Maximum permissible wear
8.2 Maximum permissible wear
Wear results in cracks on the surface of the rubber disk elements 5 (5) and/or 6 (6). To in-
spect the wear, measure the visible cracks on the surface of the rubber disk elements 5 (5)
and/or 6 (6).
If the cracks reach a length of 20 mm or a depth of 5 mm, replace the rubber disk ele-
ments 5 (5) and/or 6 (6).
8.3
Replacing wearing parts
8.3 Replacing wearing parts
DANGER
Danger due to bursting of the coupling
If you do not observe the information stipulated here regarding replacement of wearing
parts, this can lead to bursting of the coupling during operation. There is a risk of fatal in-
jury from flying fragments. Bursting of the coupling can lead to an explosion in potentially
explosive atmospheres.
•
Please observe all the stipulations concerning the replacement of wearing parts.
If the maximum permissible wear is reached, replace the rubber disk element 5 (5) or 6 (6).
For types ESD, ESDR and ESDW, replace both rubber disk elements 5 (5) and 6 (6).
The method used to replace the rubber disk elements 5 (5) and/or 6 (6) varies according to
the coupling type.
• Replace rubber disk elements 5 (5) and/or 6 (6) on types ESNR, ESDR, ESNW and
• Replace rubber disk elements 5 (5) and/or 6 (6) on types ESN and ESD (Page 49)
Summary of Contents for ELPEX-S
Page 6: ...Table of contents 6 Edition 09 2022 M3302 01en ...
Page 8: ...List of tables 8 Edition 09 2022 M3302 01en ...
Page 10: ...List of figures 10 Edition 09 2022 M3302 01en ...
Page 14: ...Introduction 1 4 Copyright 14 Edition 09 2022 M3302 01en ...
Page 22: ...Description 22 Edition 09 2022 M3302 01en Structure ...
Page 38: ...Assembling 5 3 Aligning the coupling 38 Edition 09 2022 M3302 01en ...
Page 40: ...Commissioning 40 Edition 09 2022 M3302 01en ...
Page 46: ...Operation 7 2 Fault causes and correction 46 Edition 09 2022 M3302 01en ...
Page 56: ...Service and support 9 1 Contact 56 Edition 09 2022 M3302 01en ...