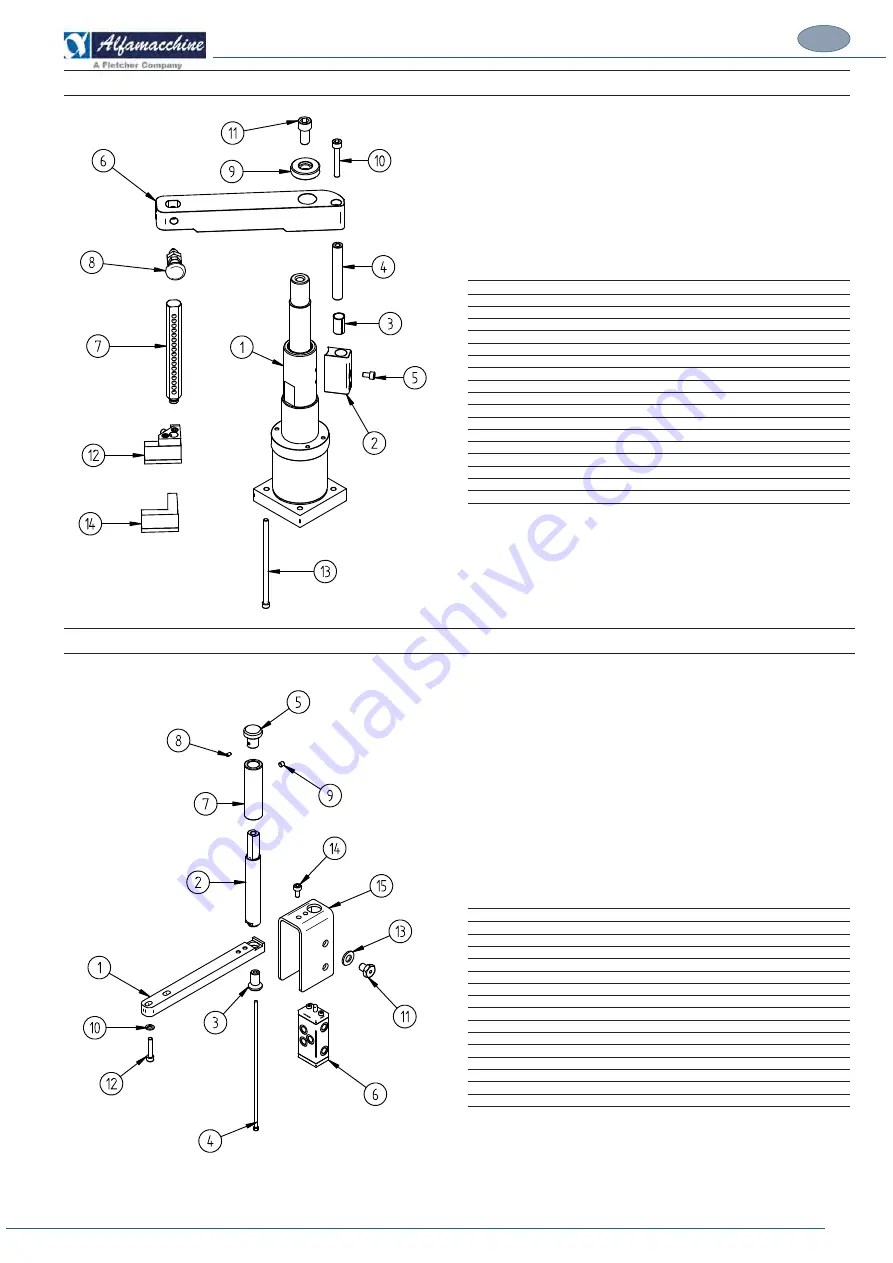
57
TRANSLATION OF THE ORIGINAL INSTRUCTIONS (Keep for future reference)
Document Code
Rev.
Date saved
Date printed
U400 INSTRUCTIONS
01
02/10/2015
02/10/2015
EN
TABLE 3 - VERTICAL CLAMP INSTALLATION
POS. CODICE
DESCRIZIONE
1 M22100002 COLONNA
COMPLETA
2 M30100038 ARRESTO
BRACCIO
3
753420016
BOCCOLA D14 L25
4 M30100044 PERNO
ANTIROTAZIONE
BRACCO
5 710100072 VITE
TCEI
M6x10
6 M30100018 BRACCIO
7
334000100
ASTA BLOCCAGGIO VERTICALE
8 753320010 POMELLO
BLOCCAGGIO
9 336100120 RONDELLA
ARRESTO
10 710100120 VITE
TCEI
M8x50
11 710100190 VITE
TCEI
M12x25
12
242230300
SUPPORTO PORTA - TAMPONE ANGOLARE
13 710100067 VITE
TCEI
M6x140
14 397100005 PORTA-TAMPONE
MAGNETICO
-
397100001
TAMPONE INTERCAMBIABILE NERO
-
397100002
TAMPONE INTERCAMBIABILE GIALLO
-
397100003
TAMPONE INTERCAMBIABILE AZZURRO
TABLE 4 - CONTROL LEVER ASSEMBLY
POS. CODICE
DESCRIZIONE
1
M30100017
LEVA MOVIMENTO SLITTA
2 M30100051 PERNO
LEVA
3
366210020
VITE FISSAGGIO PERNO LEVA
4
331500060
ASTA COMPLETA PULSANTE
5 363710020 BOTTONE
PULSANTE
6 732290001 VALVOLA
PULSANTE
7 336500090 BOCCOLA
PULSANTE
8 714300063 GRANO
M4x6
9 714300015 GRANO
M6x6
10 718100003 RONDELLA
M6
11
M30100053
VITE SUPPORTO VALVOLA
12 710100080 VITE
TCEI
M6x30
13 718100005 RONDELLA
M10
14 710100073 VITE
TCEI
M6x12
15
M29000005
CARTER SUPPORTO VALVOLA