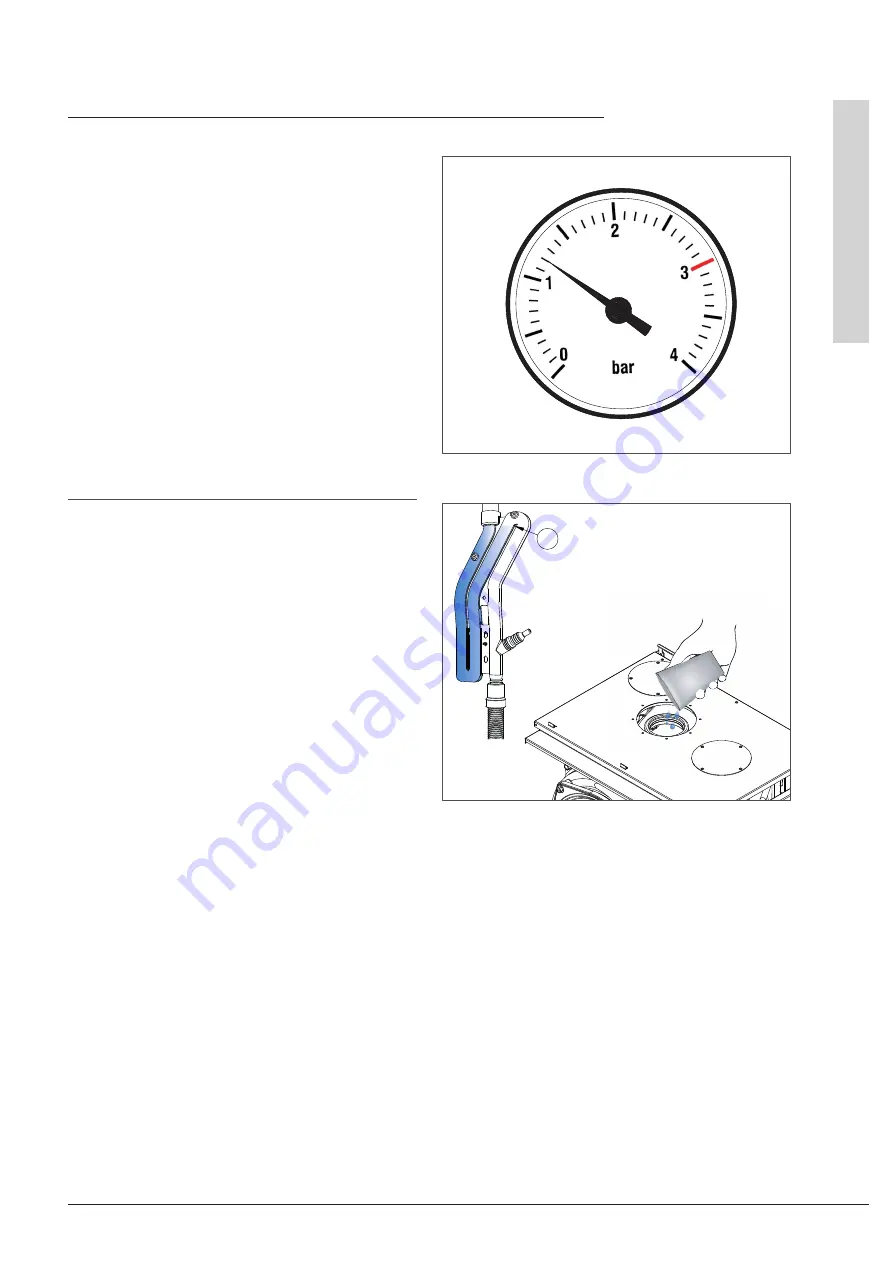
17
1. INSTALLATION
INST
ALLER
7. open the air relief valves of the radiators and
check the air removal process. When the
water starts to leak close the radiators air
relief valves.
8. if after performing these operations you
observe a decrease of the water pressure
inside the system, open once again the loading
tap “R” until the pressure gauge indicates the
value of 1.2 bar (fig. 4)
1.1.10. FILLING THE CONDENSATE
COLLECTION SIPHON
Before starting the boiler you have to fill the
condensate collection siphon in order to avoid flue
reflux through the siphon.
Fill the condensate collection siphon as follows
(see fig. 5):
› With a glass pour the water in the heat
exchanger’s flue exhaust duct outlet (see fig. 5),
up to fill the condensate trap to the highest point
“T” (fig. 5);
› Connect the dedicated flexible condensate
draining tube to a waste disposal system.
The condensate can be drained directly in
the sewerage system by inserting an easily
serviceable siphon.
T
fig. 4
fig. 5