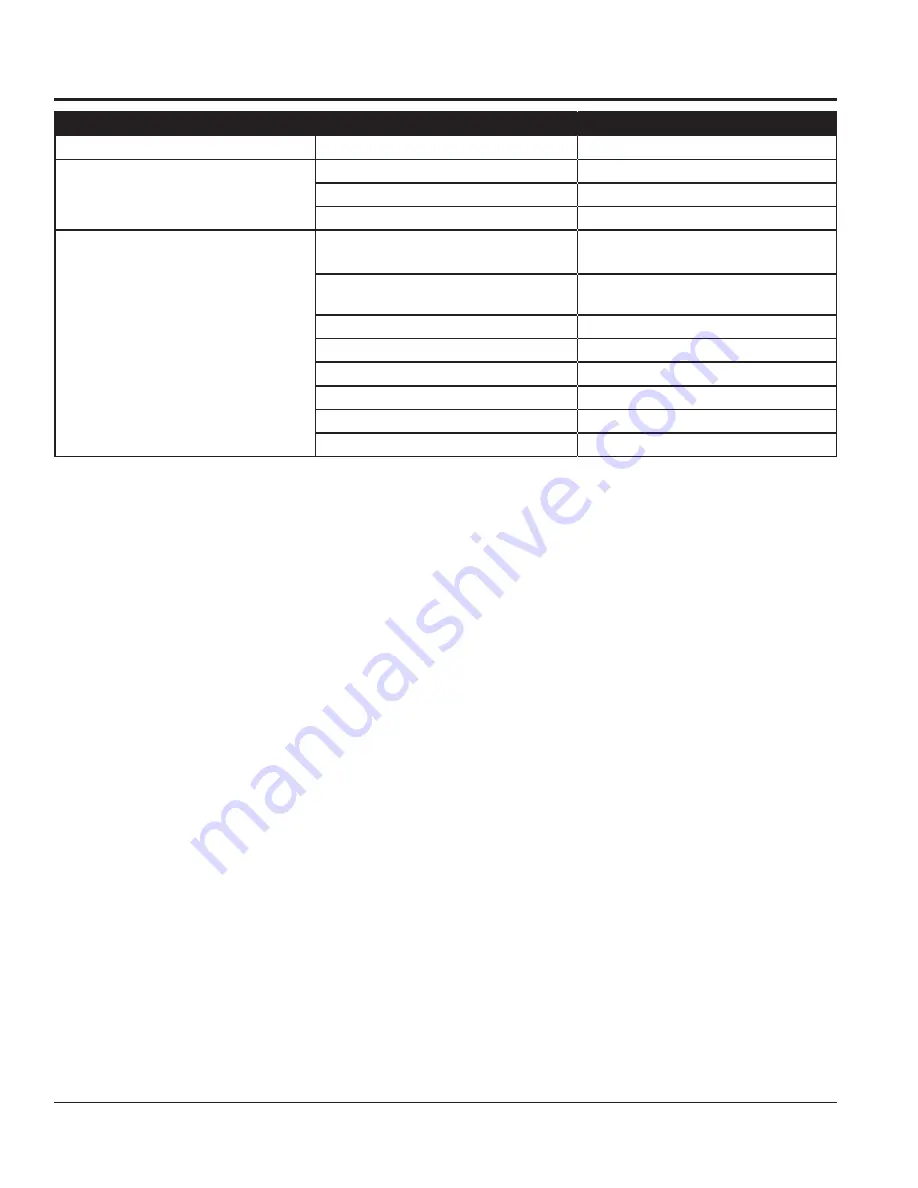
PAGE 48 — EHHNK5 RIDE-ON TROWEL • OPERATION MANUAL — REV. #3 (05/03/21)
TROUBLESHOOTING (ENGINE)
Troubleshooting (Engine) - continued
Symptom
Possible Problem
Solution
Low engine power output and low speed,
black exhaust smoke.
Air fi lter blocked?
Clean or replace air fi lter.
Incorrect valve clearances?
Adjust valves per engine specifi cation.
Malfunction at injector?
See engine manual.
Engine overheats.
Too much oil in engine crankcase?
Drain off engine oil down to uppermark on
dipstick.
Entire cooling air system contaminated/
blocked?
Clean cooling air system and cooling fi n
areas.
Fan belt broken or elongated?
Change belt or adjust belt tension.
Coolant insuffi cient?
Replenish coolant.
Radiator net or radiator fi n clogged with dust? Clean net or fi n carefully.
Fan, radiator, or radiator cap defective?
Replace defective part.
Thermostat defective?
Check thermostat and replace if necessary.
Head gasket defective or water leakage?
Replace parts.