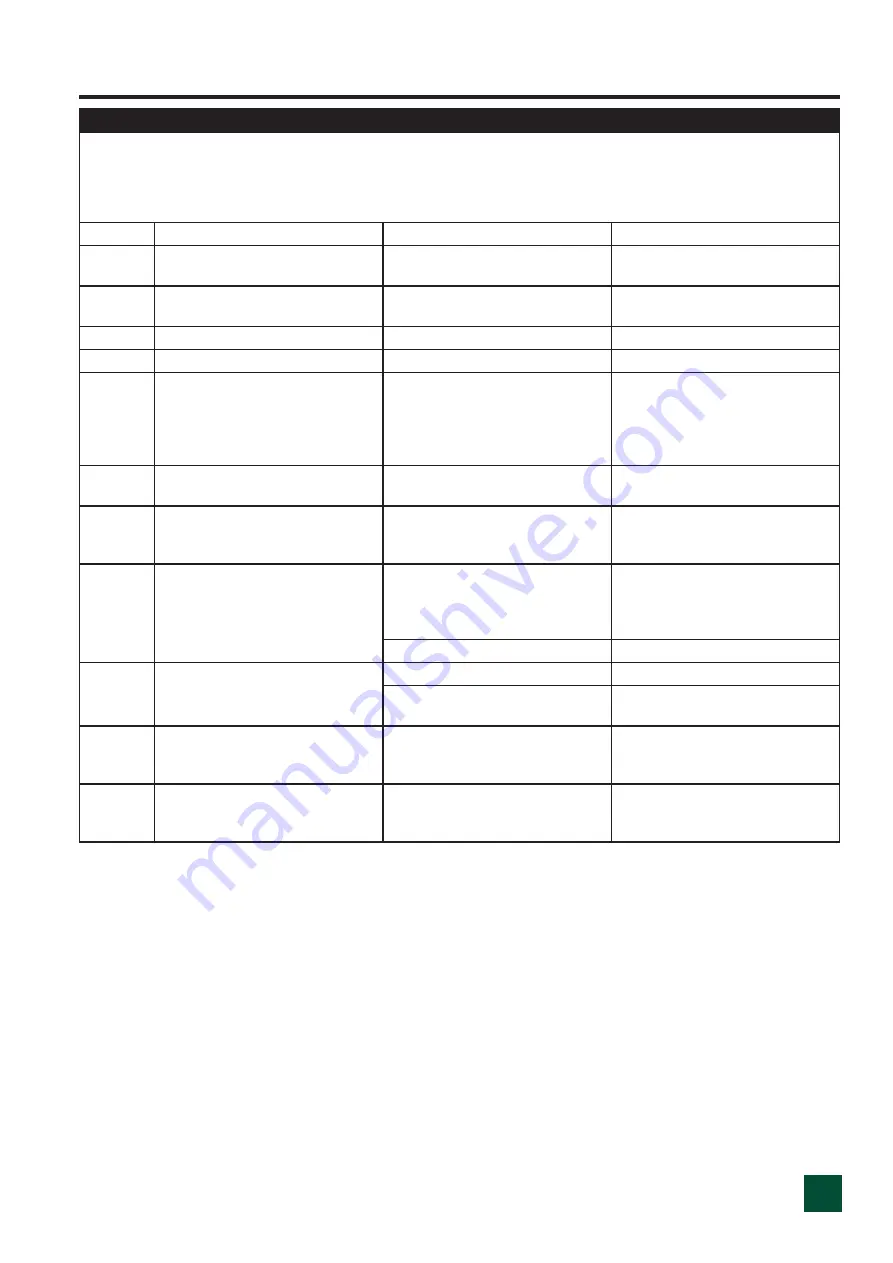
30
1300 353 986
flextool.com.au
Troub
leshooting (Er
ror Codes)
The machine controller detects a wide variety of faults or errors. Diagnostic information can be obtained on the 3100R fuel gauge display where an error code in the format
“Err ##”. The troubleshooting chart below describes the error code faults and their possible causes. Whenever a fault is encountered the first action should be to turn off the ignition
and push in the E-stop button. Then pull out the E-stop button and turn the ignition back on to see if the fault clears. This is the RESET procedure: If the error code does not clear
after the machine RESET, turn off the ignition switch and remove the 35-pin connector. Check the connector for correction or damage, clean it if necessary, and reinsert it. If the
error is still seen then the wiring and connections on the machine should be checked for breakages or loose connections. The table below should be used as a reference once the
above checks have been carried out.
Error Code
Symptom
Possible Problem
Solution
1
HW fail-safe
Motor fault voltage (hardware failure)
Motor voltage does not correspond to
throttle request?
Check for short in motor or motor wiring.
10
Main brake driver over current.
Short circuit or overloaded controller
driver?
Check brake controller driver. Reference
Curtis controller owner's manual.
15
Main current dropped.
Main contactor failed to open?
Clean the contactor switch.
17
Main contactor welded.
Main contactor fault / failed to close?
Replace contactor.
33
Supervisor DIR check fault.
Program issue?
If fault is on an external signal, check
that signal first. If no problem with
the external signal, likely indicates an
internal controller fault. Reference Curtis
controller owner's manual
34
External supply fault.
Under voltage?
Check control wiring circuit,
potentiometer wiring in particular.
36
EM-brake driver open drain.
Hold voltage set at 90%?
Check brake electrical connectors.
Check continuity. Replace motor brake
if failed.
54
Pre-charge failed/fault.
Low battery voltage?
Check battery voltage. 25V (11/12V per
battery) is good condition, 22V (9/10V
per battery) or lower is bad battery
condition.
Short circuit on traction motor outputs?
80
HPD sequencing
HPD fault present > 10 seconds.
Misadjusted throttle?
Adjust. See maintenance section.
Broken throttle potentiometer or throttle
mechanism?
Replace.
92
Traction motor open / not connected.
Controller cannot see the motor.
Short circuit in the motor?
Check the resistance across the motor
leads.
99
Undervoltage cutback.
Battery voltage < undervoltage
threshold?
Check connection at battery or controller.
Check no corrosion on the battery
terminals.
Quick checks if no reading on the fuel gauge and the machine does not operate:
1. Check 10-amp ignition fuse located on the backside of the control panel. Reference 'Electronic Component Locator" drawing.
2. Check 100-amp main fuse*located on the backside of the control panel. Reference 'Electronic Component Locator" drawing.
2. When changing the 100-amp fuse, ensure that the positive battery cable is fully disconnected. Electrical maintenance should be carried out
by a qualified person.
ERROR CODES