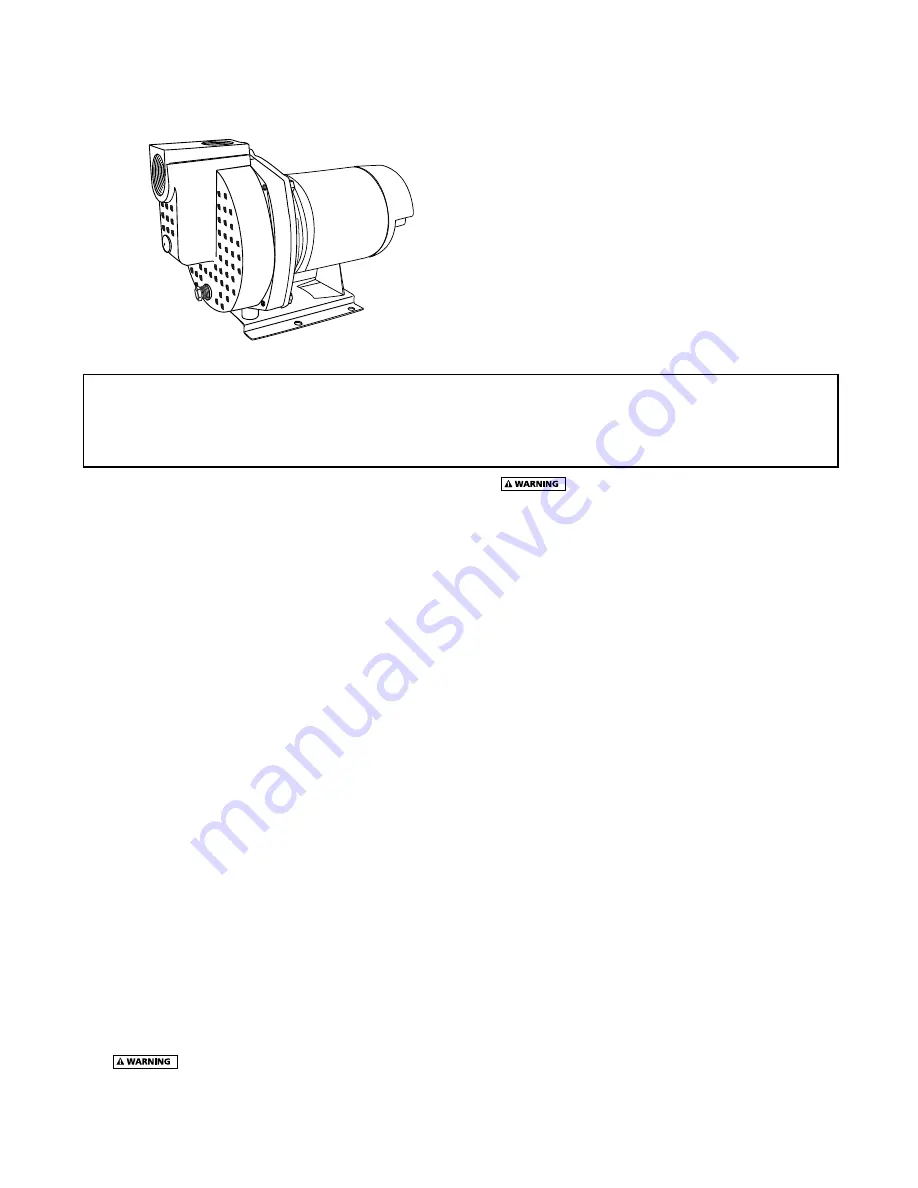
1
© Copyright 2018. All rights reserved.
GENERAL SAFETY INFORMATION
1. Follow all local electrical and safety codes, as well
as the National Electrical Code (NEC) and the
Occupational Safety and Health Act (OSHA).
2. Replace damaged or worn wiring cord
immediately.
3. Do not kink power cable and never allow the cable
to come in contact with oil, grease, hot surfaces, or
chemicals.
4. Protect the power cable from coming in contact
with sharp objects.
5. Be careful when touching the exterior of an
operating motor - it may be hot enough to be
painful or cause injury.
6. Make certain that the power source conforms to
the requirements of your equipment.
7.
Always disconnect power source before
performing any work on or near the motor or
its connected load.
If the power disconnect point
is out-of-sight, lock it in the open position and tag
it to prevent unexpected application of power.
Failure to do so could result in fatal electrical
shock.
8. Do not handle the pump with wet hands or when
standing in water as fatal electrical shock could
occur. Disconnect main power before handling
unit for
ANY REASON!
9. Unit must be securely and adequately electrically
grounded. This can be accomplished by wiring the
unit to a ground metal-clad raceway system or by
using a separate ground wire connected to the bare
metal of the motor frame or other suitable means.
10.
RISK OF ELECTRIC SHOCK.
These
pumps have not been investigated for use in swim-
ming pool areas.
11.
This product contains chemicals known
to the State of California to cause cancer and birth
defects or other reproductive harm.
NOTE: Pumps with the “UL” Mark and pumps with the
“US” mark are tested to UL Standard UL778.CSA certified
pumps are certified to CSA Standard C22.2 No. 108.
LOCATION
1. Pump can be located at the well or can be offset
some distance away from the well. For best
performance it should be located as close to the
well as possible.
2. Location can be in the basement, a pit below
ground, or in a pump house above ground.
3. Ventilation and drainage must be provided to
prevent damage from moisture to the motor and
pressure switch.
4. The pump and all piping must be protected from
freezing.
5. Pump and pipe line must be drained when not in
use if there is any danger of freezing.
WELL CONDITIONS
1. Wells should be pumped clean of all sand and
foreign matter before installing the pump or
damage may result to the operating parts.
2. The well must be able of supplying enough water
to satisfy the capacity of the pump and water
needs. The water level must not draw down below
the maximum rated suction lift of the pump or loss
of capacity and prime will result.
SUCTION LIMITATIONS
1. Shallow well installation is satisfactory where the
suction lift is less than 25 feet. Suction lift is the
vertical lift plus losses due to friction loss.
2. Suction lift varies depending upon elevation
(altitude) and water temperature.
OWNERS GUIDE TO INSTALLATION AND OPERATION
READ THESE INSTRUCTIONS CAREFULLY
Read these installation instructions in detail before installing your pump. Be sure to check the following:
1. Be certain the motor is connected for the correct line voltage being used (check motor nameplate).
2. Be certain the pump is completely primed before starting. Otherwise damage may occur to the seal.
Every pump is tested before leaving the factory, and its performance depends largely on the installation.
SPJ, ELJ SERIES
CENTRIFUGAL,
IRRIGATION
PUMP
133264 D
IL0175