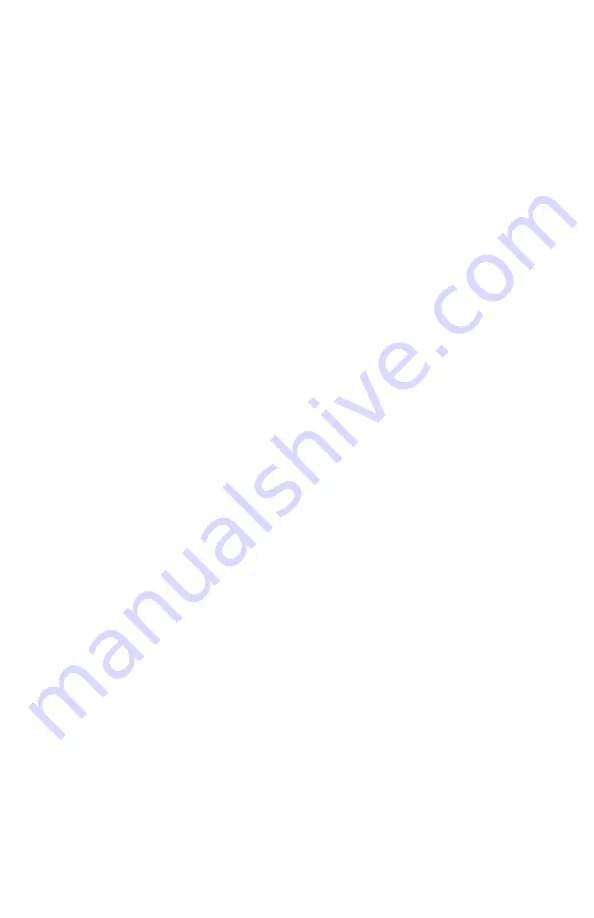
5
A typical backpressure of 5 to 50 PSI
(0.34 to 3.4 bar) will prevent cavitation.
Create backpressure by installing a
control valve on the downstream side
of the meter at the proper distance de-
tailed above.
Foreign material in the liquid being
measured can clog the turbine’s rotor
and adversely affect accuracy. If this
problem is anticipated or experienced,
install screens to filter impurities from
incoming liquids.
Models 1/2 in., 3/4 in. and 1 in.:
Maximum Particulate Size
Inches:
0.005
Microns:
125
Mesh:
120
Standard Sieve:
125
μ
m
Alternative Sieve:
No. 120
Models 1
-
1/2 in. and 2 in.:
Maximum Particulate Size
Inches:
0.018
Microns:
500
Mesh:
35
Standard Sieve:
500
μ
m
Alternative Sieve:
No. 35
To ensure accurate measurement, re-
move all air from the system before
use.
Threaded Connections
1. To protect against leakage, seal all
threads with an appropriate sealing
compound. Make sure the sealing
compound does not intrude into the
flow path.
2. Make sure the arrow on the outlet is
pointed in the direction of the flow.
3. Tighten the turbine onto the fittings.
Use a wrench only on wrench flats.
Note:
If connecting to new male
threads, burrs and curls can ad-
versely affect accuracy. Correct
the problem prior to turbine in-
stallation.
Verify accuracy after connections are
complete. See Operation section.
ANSI Flange Connection
Use a gasket between the meter flange
and mating flange. Determine the ma-
terial of the gasket based on the oper-
ating conditions and type of fluid.
Note:
Do not over tighten the flange
bolts. This may cause the gas-
ket to be compressed into the
flow stream and may decrease
the accuracy of the meter. See
ANSI flange specification sec-
tion for flange installation dia-
gram.
Verify accuracy after connections are
complete. See Operation section.
Tri-Clover
®
Flange
Connection
1. Make sure the arrow on the outlet is
pointed in the direction of the flow.
2. Insert a gasket between the meter
fitting and the mating fitting. Deter-
mine the gasket material based on
the operating conditions and the
type of fluid used.
3. Fasten with the appropriate clamp.
Tighten clamp to manufacturer’s
specifications.
Verify accuracy after connections are
complete. See Operation section.
Summary of Contents for G2
Page 23: ...23 NOTES ...