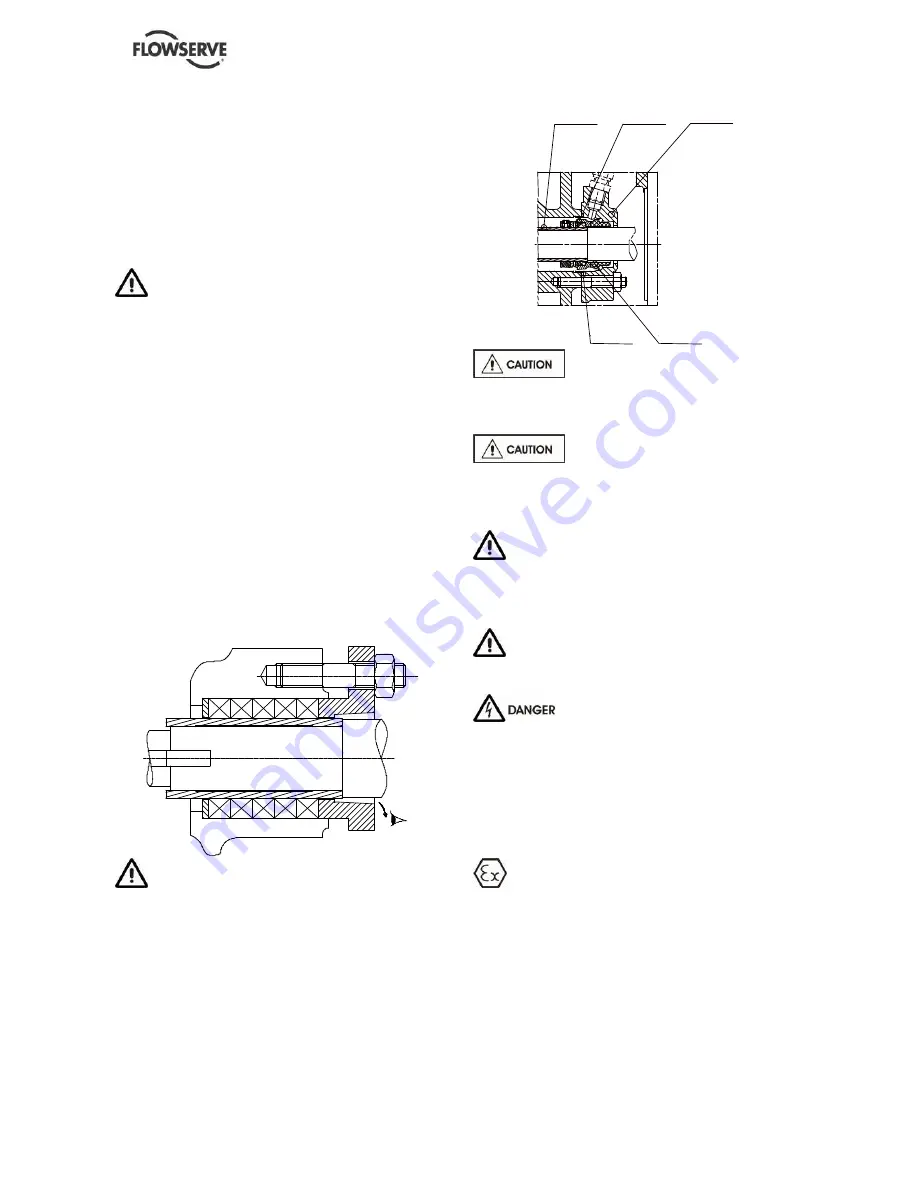
FM USER INSTRUCTIONS ENGLISH 71576526 - 03/07
Page 20 of 32
flowserve.com
5.5.2 Pump fitted with a stuffing box
If the pump has a packed gland there must be some
leakage from the gland. Gland nuts should initially
be finger-tight only. Leakage should take place soon
after the stuffing box is pressurized. If no leakage
takes place the packing will begin to overheat. If
overheating takes place the pump should be
stopped and allowed to cool before being re-started.
When the pump is re-started it should be checked to
ensure leakage is taking place at the packed gland.
When adjusting an operating stuffing box
(shield grids removed for this operation), the
operator must be very careful. Safety gloves are
compulsory and loose clothes are not allowed
(above all to the arms) to avoid being caught by the
pump shaft.
The pump should be run for ten minutes with steady
leakage and the gland nuts tightened by 10 degrees
at a time until leakage is reduced to an acceptable
level.
The temperature of the gland should be checked
after each round of tightening. If the temperature
starts to climb rapidly then back off the gland nuts
until the temperature drops down. Wait for the
temperature to stabilize before tightening again.
The leakage must not be reduced below a rate of 20
drops per minute. Bedding in of the packing may
take several hours.
Shield grids being removed during installation
of the gland packing, it must be ensured that they
are replaced as soon as this operation is completed.
5.5.3 Pump fitted with a mechanical seal
A mechanical seal ensures a seal without leakage
and does not need any adjustment. Nevertheless if a
light leakage occurs during start-up, it should
disappear after the initial running in of the friction
faces.
4213
4200
2445
4240
4610
With a mechanical seal, the
maximum temperature is limited to 80 °C (176 °F)
whatever the internal construction of the pump is
(Cast iron or Bronze).
NEVER RUN A MECHANICAL SEAL
DRY, EVEN FOR A SHORT WHILE.
SAFETY INSTRUCTIONS WHEN THE PUMP IS
RUNNING:
If hot or freezing components of the machine
can present a danger to operators, they must be
shielded to avoid accidental contact. If a 100 %
protection is not possible, the machine access must
be confined to the maintenance staff only.
If the temperature is greater than 80 °C (176
°F), a warning plate must be clearly placed on the
pump.
It is strictly forbidden to open switch
cupboards, switch boxes, or all other live electric
equipment. If it is necessary to open them in order to
take readings, to carry out tests or adjustments for
example, only a skilled technician may do them with
adapted tools. Make sure that physical protections
against electrical risks are used.
5.5.4 Bearings
If the pumps are working in a potentially
explosive atmosphere, temperature or vibration
monitoring at the bearings is recommended. If
bearing temperatures are to be monitored it is
essential that a benchmark temperature is recorded
at the commissioning stage and after the bearing
temperature has stabilized.
Record the bearing temperature (t) and the
ambient temperature (ta)
Estimate the likely maximum ambient
temperature (tb)