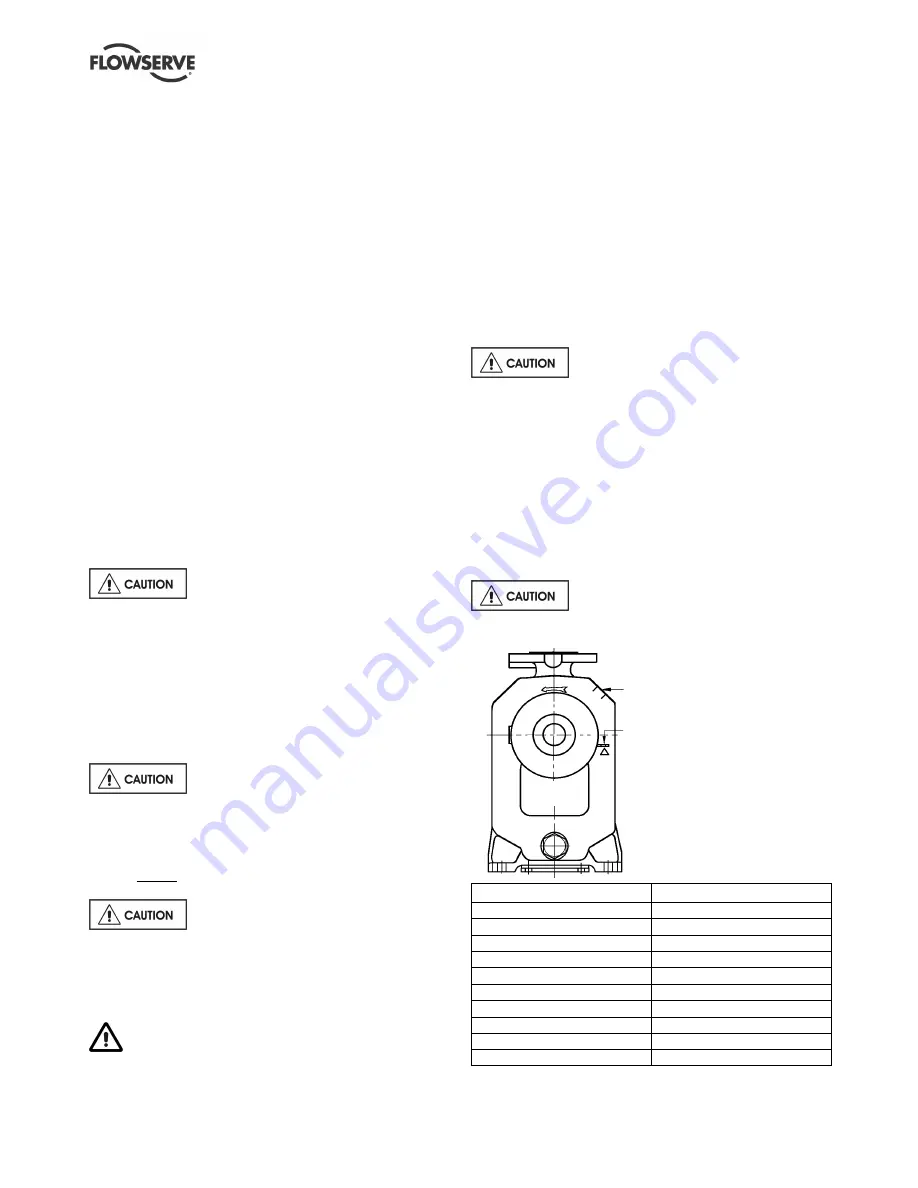
CPX, CPXR, CPXN and CPXP USER INSTRUCTIONS ENGLISH 71569117 02-10
Page 18 of 44
flowserve.com
The bearing temperature may be allowed to rise to
50 ºC (90 ºF) above ambient, but should not exceed
82 ºC (180 ºF) (API 610 limit). A continuously rising
temperature, or an abrupt rise, indicates a fault.
Pumps which handle high temperature liquids may
require their bearings to be cooled to prevent bearing
temperatures exceeding their limits.
5.2.5.2 Grease lubricated bearings
When grease nipples are fitted, one charge between
grease changes is advisable for most operating
conditions; ie 2 000 hours interval. Normal intervals
between grease changes are 4 000 hours or not
more than 6 months.
The characteristics of the installation and severity of
service will determine the frequency of lubrication.
Lubricant and bearing temperature analysis can be
useful in optimizing lubricant change intervals.
The bearing temperature may be allowed to rise to
55 ºC (99 ºF) above ambient, but should not exceed
95 ºC (204 ºF). For most operating conditions, a
quality grease having a lithium soap base and NLGI
consistency of No 2 or No 3 is recommended. The
drop point should exceed 175 ºC (350 ºF).
Never mix greases containing different
bases, thickeners or additives.
5.3 Open impeller clearance
The impeller clearance is set in the factory. This may
require adjustment because of piping attachment or
increase in temperatures. For setting instructions see
section 6.7, Setting impeller clearance.
5.4 Direction of rotation
Serious damage can result if the pump
is started or run in the wrong direction of rotation.
The pump is shipped with the coupling element
removed. Ensure the direction of rotation of the motor is
correct before fitting the coupling element. Direction of
rotation must correspond to the direction arrow.
If maintenance work has been carried
out to the site's electricity supply, the direction of
rotation should be re-checked as above in case the
supply phasing has been altered.
5.5 Guarding
Guarding is supplied fitted to the pump set.
In member countries of the EU and EFTA, it is a legal
requirement that fasteners for guards must remain
captive in the guard to comply with the Machinery
Directive 2006/42/EC. When releasing such guards,
the fasteners must be unscrewed in an appropriate
way to ensure that the fasteners remain captive.
Whenever guarding is removed or disturbed ensure
that all the protective guards are securely refitted
prior to start-up.
5.6 Priming and auxiliary supplies
5.6.1 CPX, CPXR and CPXN filling and priming
Ensure inlet pipe and pump casing is
completely full of liquid before starting continuous
duty operation.
Priming may be carried out with an ejector, vacuum
pump interceptor or other equipment, or by flooding
from the inlet source.
When in service, pumps using inlet pipes with foot
valves may be primed by passing liquid back from the
outlet pipe through the pump.
5.6.2 CPXP filling and self priming
Fill the pump with liquid to be pumped,
or compatible liquid, via the filling plug [6569.4],
before starting continuous duty operation.
Pump housing
filling hole.
When the initial fill
reaches the suction
pipe, excess liquid will
flow out of the casing.
Pump size
Initial fill litre (US gal.)
40-40CPXP125
2.5 (0.65)
80-80CPXP125
6.0 (1.50)
40-40CPXP160
3.0 (0.80)
80-80CPXP160
6.5 (1.75)
40-40CPXP200
5.0 (1.35)
65-65CPXP200
8.5 (2.25)
80-80CPXP250
12.0 (3.20)
100-100CPXP250
36.0 (9.50)
100-100CPXP315
14.8 (3.95)
150-150CPXP315
18.0 (4.80)