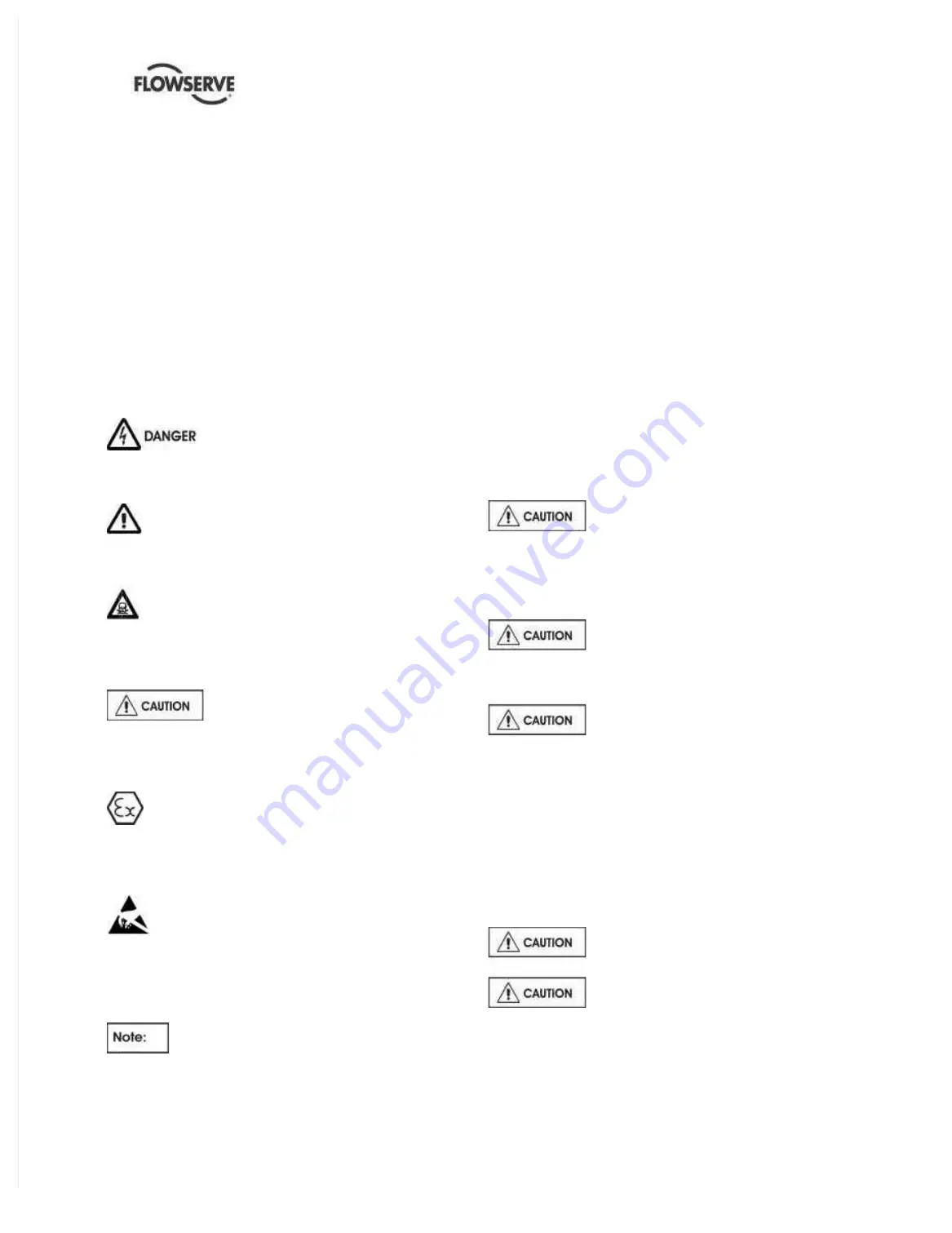
DMX/DMXD/DMXH/DMXDH USER INSTRUCTIONS ENGLISH 71569282 - 10/09
Page 4 of 60
there is any doubt as to the suitability of the
product for the application intended, contact
Flowserve for advice, quoting the serial number.
If the conditions of service on your purchase order are
going to be changed (for example liquid pumped,
temperature or duty) it is requested that the user seeks
Flowserve’s written agreement before start up.
1.6 Safety
1.6.1
Summary of safety markings
These user instructions contain specific safety
markings where non-observance of an instruction
would cause hazards. The specific safety markings
are:
This symbol indicates electrical safety
instructions where non-compliance will involve a high
risk to personal safety or the loss of life.
This symbol indicates safety instructions where
non-compliance would affect personal safety and
could result in loss of life.
This symbol indicates “hazardous substances
and toxic fluid” safety instructions where non-
compliance would affect personal safety and could
result in loss of life.
This symbol indicates safety
instructions where non-compliance will involve some
risk to safe operation and personal safety and would
damage the equipment or property.
This symbol indicates explosive atmosphere
marking according to ATEX. It is used in safety
instructions where non-compliance in the hazardous
area would cause the risk of an explosion.
This symbol indicates is used in safety
instructions to remind not to rub non-metallic surfaces
with a dry cloth; ensure cloth is damp. It is used where
non-compliance in the hazardous area would cause
the risk of an explosion.
This sign is not a safety symbol but
indicates an important instruction in the assembly
process.
1.6.2
Personnel qualification and training
All personnel involved in the operation, installation,
inspection and maintenance of the unit must be
qualified to carry out the work involved. If the
personnel in question do not already possess the
necessary knowledge and skill, appropriate training
and instruction must be provided. If required the
operator may commission the manufacturer / supplier
to provide applicable training.
Always co-ordinate repair activity with operations and
health and safety personnel, and follow all plant safety
requirements and applicable safety and health laws
and regulations.
1.6.3
Safety action
This is a summary of conditions and actions to
prevent injury to personnel and damage to the
environment and to equipment. (For products
used in potentially explosive atmospheres
section 1.6.4 also applies.)
Prevent excessive external pipe load
Do not use pump as a support for piping. Do not
mount expansion joints, unless authorized by
Flowserve in writing, so that their force, due to
internal pressure, acts on the pump flange.
Ensure correct lubrication
(See section 5,
Commissioning, startup, operation
and shutdown
.)
Start the pump with outlet valve partly
opened (Unless otherwise instructed at a specific
point in the user instructions). This is recommended
to minimize the risk of overloading at full flow and
damaging the pump at zero flow. Pumps may be
started with the valve further open only on
installations where this situation cannot occur. The
pump outlet control valve may need to be adjusted to
comply with the duty following the run-up process.
(See section 5,
Commissioning start-up, operation
and shutdown
.)
Never run the pump dry.
Inlet valves to be fully open when
pump is running. Running the pump at zero flow or
below the recommended minimum flow continuously
will cause damage to the pump and seals. Low flow
rates may cause a reduction in pump/bearing life,