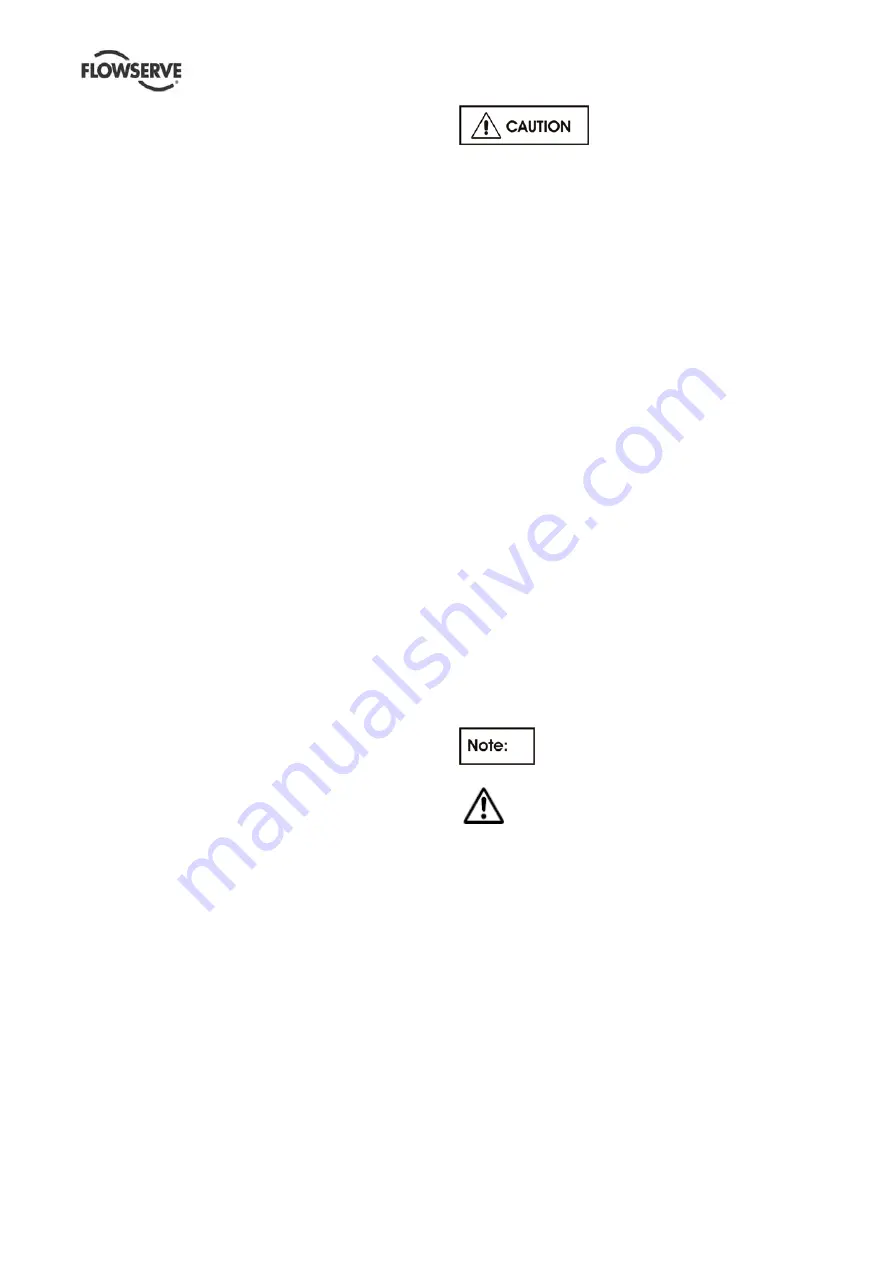
ERPN-M USER INSTRUCTIONS ENGLISH 02-08
Page 17 of 37
5.1 Precommissioning procedure
a) The bearing housing must be filled with the
indicated oil. Check also the oil level.
b) The pump must be completely filled with liquid to
avoid running dry and to guarantee a correct
performance of the pump.
c) During filling the pump shall reach the specified
temperature, so pumps for hot liquids (T > 100 °C
(212 °F)) shall be warmed up by preflushing.
d) Check the sense of rotation of the pump (Coupling
spacer dismantled).
Sense of rotation is clockwise viewed to the drive
end of the pump.
e) Check the readiness of all auxiliary systems
(flushing sys., lubrication sys.,...) for start up.
f)
All pipe work, including the internal and the
auxiliary pipe work, must be connected correctly
and must be absolutely tight. Check the tightness
of all connections of the auxiliary pipe work. The
suction valve must be open, the discharge valve
shall be closed.
g) Turn the pump by hand, if required with the help of
a lever, to check the free rotation of the rotor. The
rotor must turn uniformly and noiselessly. Some
resistance may be felt due to friction in bearings
and seals.
h) Check the readiness of the driver for start up. Refer
to the manual of the driver (preheating for
explosion proof E-motor).
5.2 Pump Lubricants
5.2.1 Lubrication
The bearing housing shall be filled with proper
lubricating oil prior to start up. If the pump will be
started after a longer storage period, the bearing
housing should be first flushed and cleaned with
gasoline. It is not necessary to remove the
preservation oil as this will mix up thoroughly with the
lubrication oil.
Lubrication is provided by the pumping effect of the
rotating ball bearings. Maintaining the correct oil level
(middle of the oil sight glass) ensures that the lower
ball bearing is covered with oil.
As option a
1
/
2
” NPT connection for a purge oil mist
lubrication is provided (refer to General Arrangement
Drawing).
For recommended lubricating oils refer to the
lubrication table 5.2.6
5.2.2 Purge oil mist lubrication
For preventing, that dirt or humidity get into the bearing
housing, this pump is equipped with a
1
/
2
” NPT
connection for air or nitrogen supply.
Also at standstill the air or nitrogen supply shall be
maintained.
The pressure shall be between
0.01 bar (0.14 psi) and 0.02 bar (0.29 psi)
, otherwise
you have to consider an oil leckage and as a result a
bearing damage .
The supplied air or nitrogen shall be clean and dry.
5.2.3 Oil change
After first start up, the oil shall be changed after 200
service hours.
Every further oil change shall take place after about
2000 service hours or at least every 6 month.
To change the oil use the following procedure:
a) Remove the reservoir (for some type of oilers you
must loose a fixing screw or lock nut, refer to
section 5.2.4
Oil level
).
b) Open the oil drain on the bearing housing to
remove the oil.
c) Close the oil drain and fill in Oil through the oiler
until the oil level reaches the bottom of the sight
glass.
d) Fill the reservoir and put it quickly to the body of the
oiler. Observe the level in the reservoir. It will
decrease until the required oil level is reached
(middle of the sight glass). Ensure that enough oil
remains in the reservoir.
e) If necessary, the oil level can be adjusted by
referring to section 5.2.4
Oil level
.
5.2.4 Oil level
The correct oil level is in the middle of the oil sight glass
and shall be checked when pump is not in operation.
Periodically check if the lubricating oil is mixed with any
condensed water. Careful opening of the oil drain
during a stop of the pump will show any water.
Use a spirit level to check the horizontal
alignment of the bearing housing.
A too high oil level will result in higher bearing
temperatures and therefore poorer lubrication.
5.2.4.1 Adjusting of ADAMS Constant Level Oiler
This design of Constant Oiler prevents the flooding of
the bearing by means of the positive setting in the
Oiler, thus maintaining the correct oil level at all
times. When these Oilers are used on Ball or Roller
bearings, the installation is the same as described
below, excepting that the oil level in the bearing
should never cover more than maximum above inside
diameter of the outer race at its lowest point.