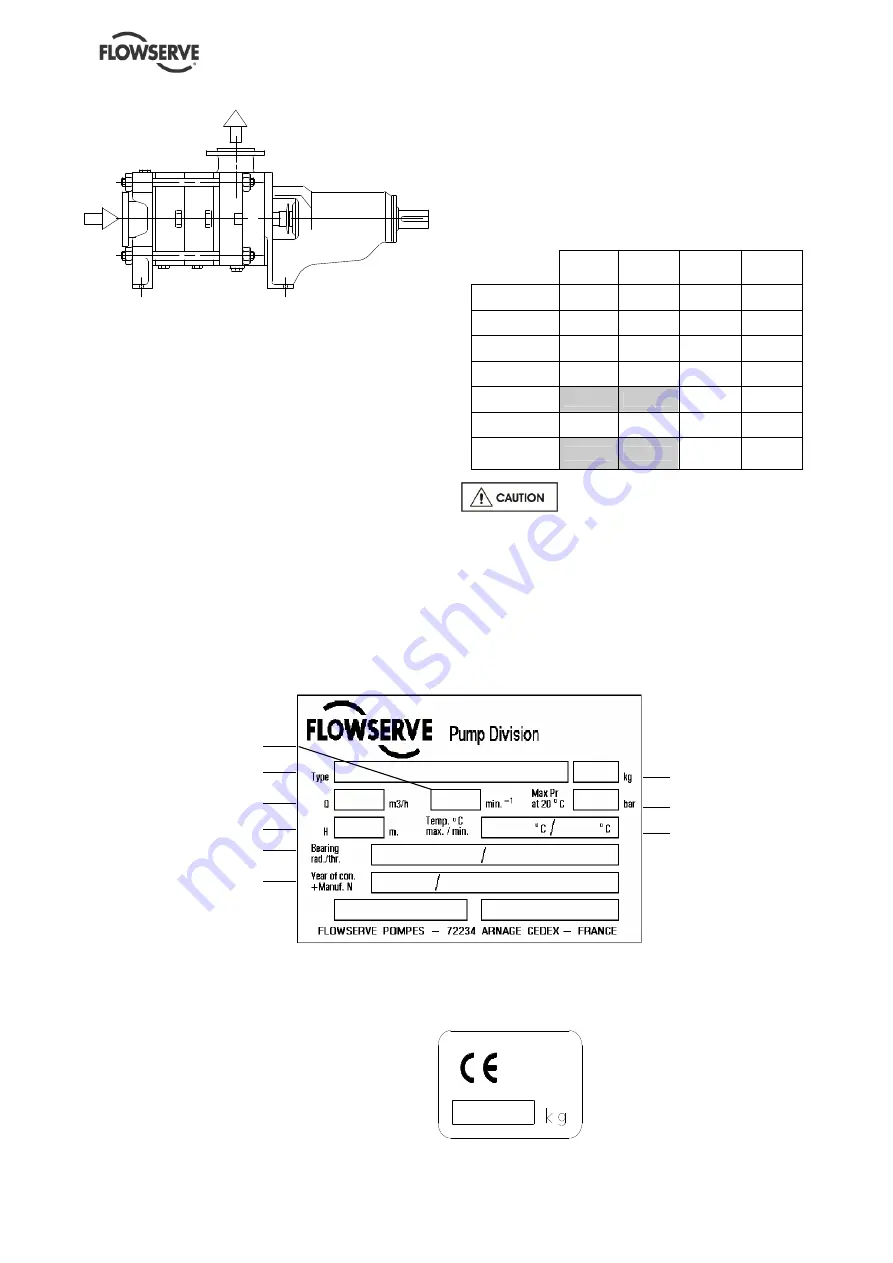
FP USER INSTRUCTIONS ENGLISH 71576286 - 07/06
Page 12 of 35
Maximum working pressure at discharge
................................................................ 25 bars
Maximum working pressure at suction.... 16 bars
except 122-152 and 202 FP.................... 10 bars
Maximum pumped fluid temperature ...... 105 °C
impeller and diffuser for
CAST IRON
or
BRONZE
.
Minimum pumped fluid temperature ....... -10 °C
Maximum ambient temperature .............. 40 °C
Maximum solid suspension ..................... 50 g/m
3
Density........................................................... 1
Viscosity .............................................. 1 mm²/s
Frequency ................. 50 Hz (1450 - 2900 min
- 1
)
................................... 60 Hz (1750 - 3500 min
- 1
)
Maximum number of stages (according to
rotation speed)
3500
min
-1
2900
min
-1
1750
min
-1
1450
min
-1
50 FP
6
7
7
7
65 FP
4
6
7
7
80 FP
3
5
6
6
100 FP
3
5
6
6
122 FP
4
5
125 FP
2
3
4
5
152 FP & 202
FP
3
4
The maximum speed is shown on the
pump nameplate.
3.2 Nomenclature
Characteristics shown on the nameplate fixed on the pump are as shown below:
Each pump is supplied with the following nameplate:
Each pump unit is supplied with the following nameplate:
Mass of the set
Pump type
Speed of rotation
Flow rate
Year of constr
Manufacture number
Head
Radial/thrust bearing
Mass
Maximum admissible
Pressure at 20 °C
Maximum / minimum
temperature