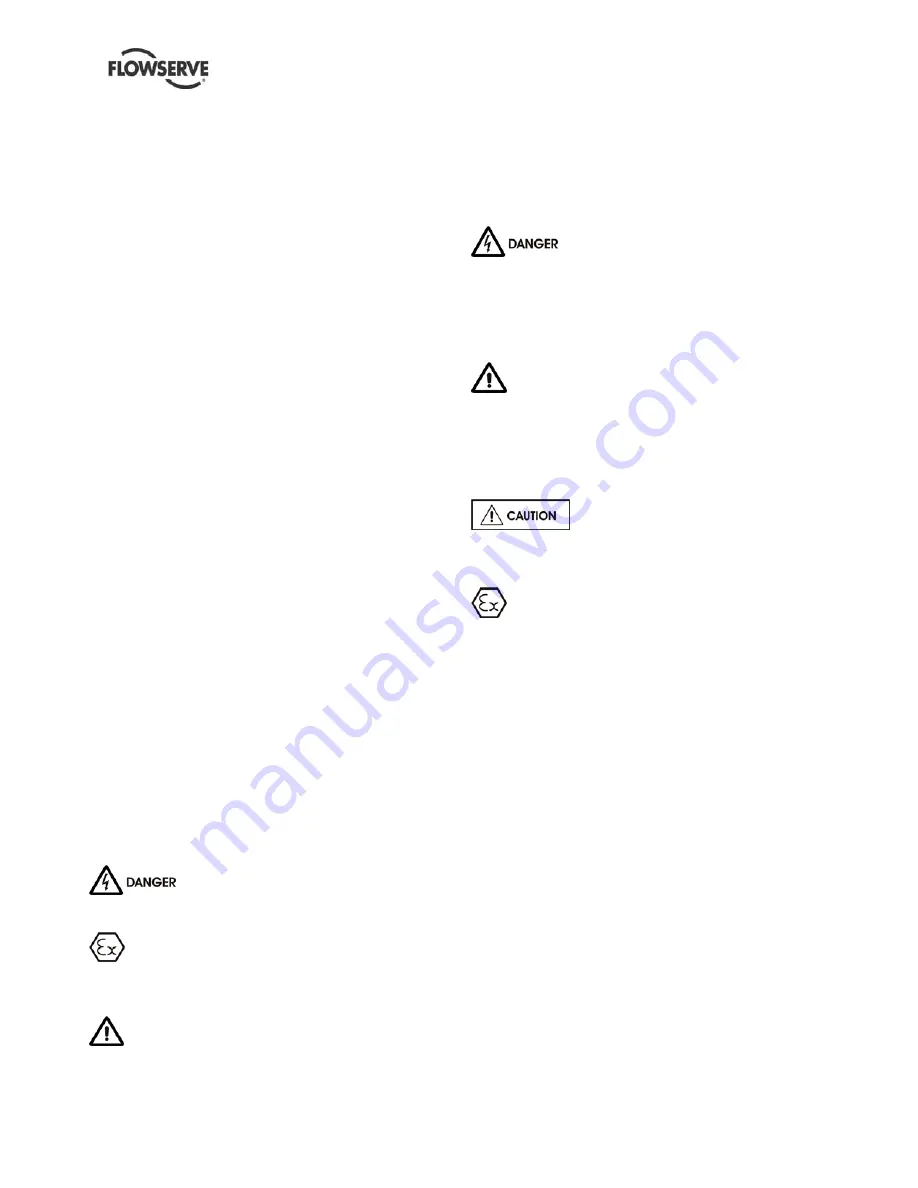
HDX USER INSTRUCTIONS ENGLISH 85392696 - 01/11
Page 22 of 60
should be provided with cooling only if required by the
operating conditions
4.6.5 Pumps fitted with mechanical seals
Single seals requiring re-circulation will normally be
provided with auxiliary piping from pump casing
already fitted. Symbols which FLOWSERVE work on
seal connections are as follows:
Q - quench
F - flush
D - drain
outlet
BI
-
barrier fluid in
BO
-
barrier fluid out
Single seals which require external flushing or
auxiliary quench must be connected to a specific
supply.
Double seals require a barrier liquid compatible with
the pumped liquid.
With back-to-back double seals, the barrier liquid
should be at a minimum pressure of 2 bar above the
maximum pressure on the pump side of the inner
seal. The barrier liquid pressure must not exceed
limitations of the seal on the atmospheric side. For
toxic service the barrier liquid supply and discharge
must be in a safe area.
For specific information refer to the mechanical seals
manufacturer’s instructions.
4.6.6 Final checks
Check the tightness of all bolts in the suction and
discharge pipework. Check also the tightness of all
foundation bolts and auxiliary lines.
4.7 Final shaft alignment check
After connecting piping to the pump, rotate the shaft
several times by hand to ensure there is no binding
and all parts are free.
Recheck the coupling alignment, as previously
described, to ensure no strain on coupling is due to
pipe. If pipe strain exists, correct piping.
4.8 Electrical connections
Electrical connections must be made by
a qualified Electrician in accordance with relevant
local national and international regulations.
It is important to be aware of the EUROPEAN
DIRECTIVE on potentially explosive areas where
compliance with IEC60079-14 is an additional
requirement for making electrical connections.
It is important to be aware of the EUROPEAN
DIRECTIVE on electromagnetic compatibility when
wiring up and installing equipment on site. Attention
must be paid to ensure that the techniques used
during wiring/installation do not increase
electromagnetic emissions or decrease the
electromagnetic immunity of the equipment, wiring or
any connected devices. If in any doubt contact
Flowserve for advice.
The motor must be wired up in
accordance with the motor manufacturer's
instructions (normally supplied within the terminal
box) including any temperature, earth leakage,
current and other protective devices as appropriate.
The identification nameplate should be checked to
ensure the power supply is appropriate.
A device to provide emergency stopping must
be fitted.
If not supplied pre-wired to the pump unit, the
controller/starter electrical details will also be supplied
within the controller/starter.
For electrical details on pump sets with controllers
see the separate wiring diagram.
See section 5.3, Direction of rotation
before connecting the motor to the electrical supply
4.9 Protection systems
The following protection systems are
recommended particularly if the pump is installed in a
potentially explosive area or is handling a hazardous
liquid. If in doubt consult Flowserve.
If there is any possibility of the system allowing the
pump to run against a closed valve or below
minimum continuous safe flow a protection device
should be installed to ensure the temperature of the
liquid does not rise to an unsafe level.
If there are any circumstances in which the system
can allow the pump to run dry, or start up empty, a
power monitor should be fitted to stop the pump or
prevent it from being started. This is particularly
relevant if the pump is handling a flammable liquid.
If leakage of product from the pump or its associated
sealing system can cause a hazard it is
recommended that an appropriate leakage detection
system is installed.
To prevent excessive surface temperatures at
bearings it is recommended that temperature or
vibration monitoring are carried out. See sections
5.7.4 and 5.7.5.