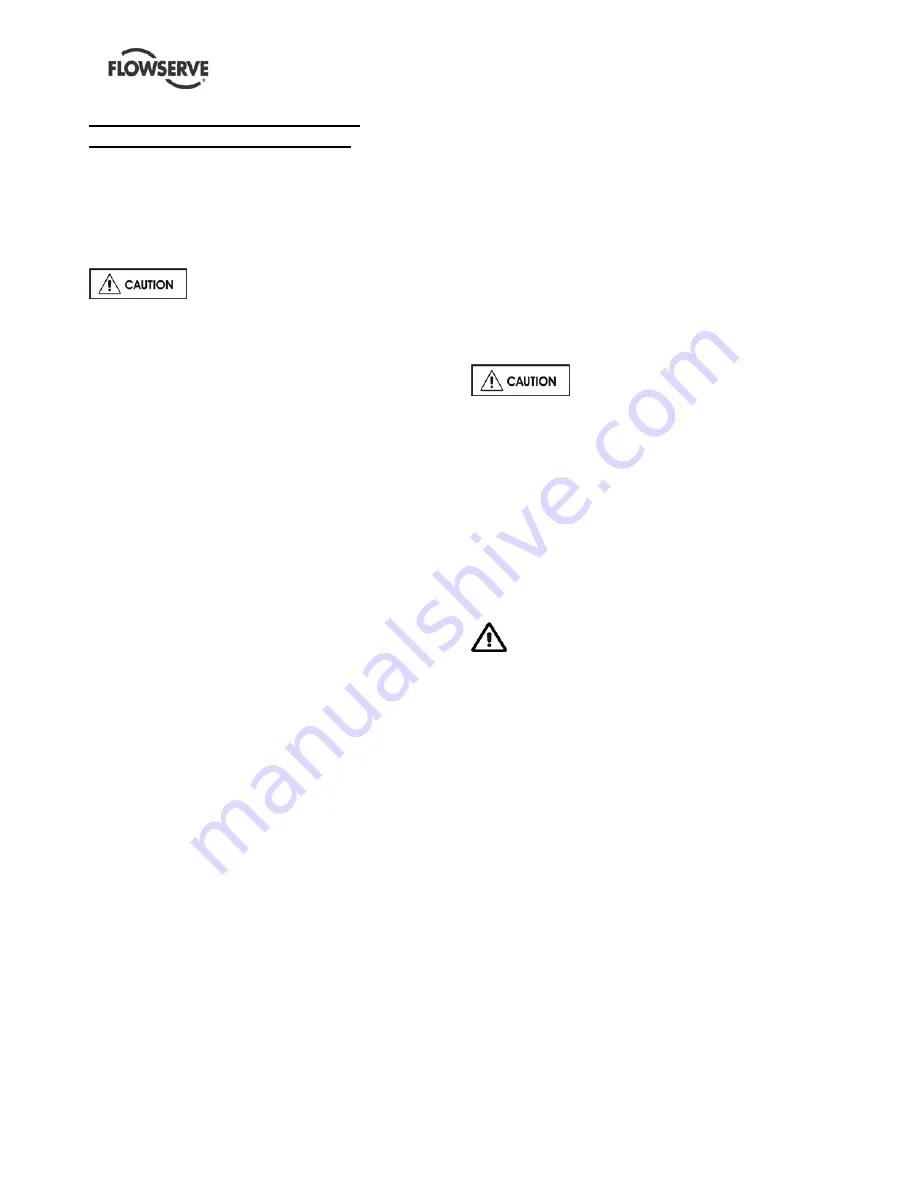
HDX USER INSTRUCTIONS ENGLISH 85392696 - 01/11
Page 23 of 60
5 COMMISSIONING, START-UP,
OPERATION AND SHUTDOWN
The following procedures are presented to outline the
most important steps involved in pump operation. Any
modification of these procedures due to particular
installation peculiarities should conform to good
engineering practices.
Never operate the pump with suction
valve closed.
Never operate the pump unless it is filled with liquid
and vented
.
Never operate the pump unless a liquid source is
available.
Never operate the pump with discharge valve closed
or below the minimum specified flow rate. If reduced
capacity operation is required on occasion, a
recirculating line should be installed according
FLOWSERVE recommendations.
Where possible avoid severe thermal shocks due to
sudden changes of liquid temperature. Warm-up the
pump at all times before start-up if the pumped liquid
is hot or subject to crystallize
Lubricate the unit prior to starting.
Do not operate the unit unless coupling guards are
bolted in place
.
Never operate the pump above the name plate
conditions.
During pump operation, keep the vent and drain
valves in closed position, to prevent any liquid from a
high pressure point flowing into a low pressure point.
Do not wipe down in the vicinity of rotating parts. If
unusual noise or high vibrations occur, secure the
pump as soon as possible.
5.1 Pre-commissioning procedure
The following steps should be followed at initial start
up and after the equipment has been overhauled:
a) Prior to installing the pump, flush the suction side
of the system to remove all deposit (slag, bolts
etc).
b) Ensure the pump and piping is clean. Before
putting the pump into operation, the piping should
be thoroughly back flushed to remove any foreign
matter which may have accumulated during
installation. Take all possible care not to
contaminate your system.
c) Install suction strainer if required. (See Section
4.6.2.1).
d) Fill the bearing housings with the appropriate oil
to the correct level. Bearing must receive a small
amount of oil prior to starting to ensure adequate
lubrication at start up. (Refer to Section 5.1.1).
e) Turn pump rotor by hand or with a strap wrench
to make sure it turns smoothly.
f) Assure that correct seal piping has been installed
and has not been damaged.
Most cartridge seals are equipped
with a spacer between the gland plate and drive
collar. This spacer must be removed before
starting unit.
g) Prior to coupling installation, bump start motor to
check for correct rotation. If rotation is not correct
refer to motor manual for appropriate connections
to change rotation (Shut down all power prior to
change).
h) Ensure coupling is correctly aligned and
lubricated, and pump and driver is satisfactorily
doweled. (Refer to Section 4.5).
The unit must not be operated unless
coupling guard is securely and completely bolted
in place. Failure to observe the warning could
result in injury to operating personnel.
i) Check torque of all bolting and the plugs for
tightness.
5.1.1 Lubrication
Lubrication of bearing is by oil circulation into the
bearing housing provided by oil ring, slinger or pure
oil mist. A constant level oiler is normally furnished
(except for pure oil mist lubrication) with the pump
unless otherwise specified.
5.1.1.1 Ball Ball Lubrication
Before filling the bearing housing reservoir, flush out
the housing thoroughly with safety solvent and a
leading grade of flushing oil, compatible with the
lubrication oil that will be used.
The oil level must be maintained at the correct level:
oil lack may cause overheating and failure of the
bearings, while exceeding the correct level can result
in leakage from the labyrinth seals. The constant
level oiler can be adjusted by changing the height of