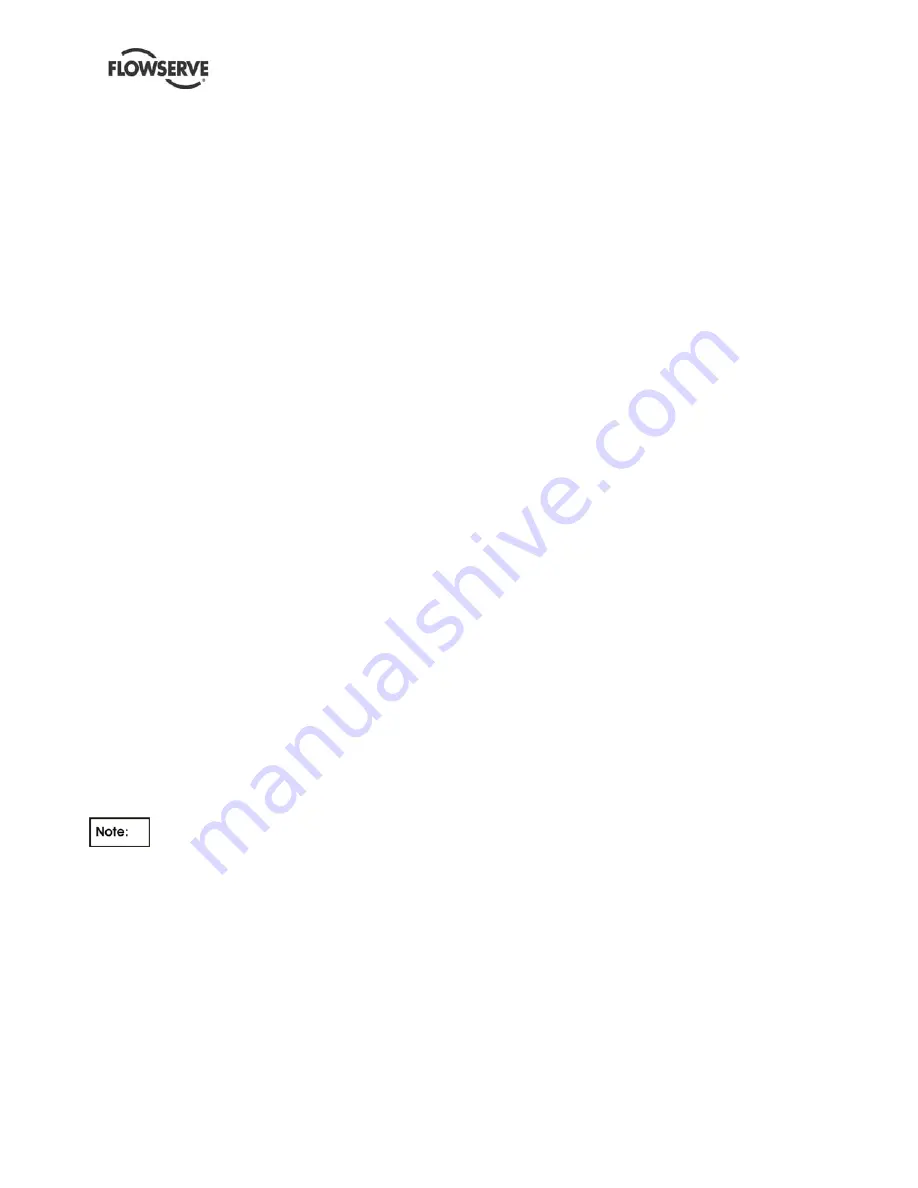
HDX USER INSTRUCTIONS ENGLISH 85392696 - 01/11
Page 35 of 60
If the pump is supplied with a constant level oiler the
oil level will be automatically maintained and as long
as oil is visible in the glass bottle there is no need to
refill. If however a sight glass has been fitted then
regular checks should be made to ensure the level is
maintained at the centre of the glass window.
Refer to section 5.1.1 for methods of oil fill, section
5.2.1 for oil grade recommendations and 5.2.4 for the
schedule and temperature limits.
6.2.6 Mechanical seals
No adjustment is possible. When leakage reaches
an unacceptable level the seal will need replacement.
6.3 Spare parts
6.3.1 Ordering of spares
Flowserve keep records of all pumps that have been
supplied. When ordering spares the following
information should be quoted:
1)
Pump serial number
2) Pump
size
3)
Part name (a)
4)
Part number (a)
5)
Number of parts required
(a) Taken from the cross section drawing stored into
the job user instruction book and only in case not
available see at section 8.
The pump size and serial number are shown on the
pump nameplate.
To ensure continued satisfactory operation,
replacement parts to the original design specification
should be obtained from Flowserve.
Any change to the original design specification
(modification or use of a non-genuine part) will
invalidate the pump’s safety certification.
If rings are ordered as repair parts after
the pump has been put into service, undersized
stationary rings or oversized impeller rings will
not be furnished unless specifically requested by
the customer.
If undersize or oversize rings are desired, the amount
of undersize or oversize required on the I.D. or the
O.D. must be stated by the customer in the repair
order
.
It is recommended as insurance against delays that
spare parts be purchased at the time the order for the
complete unit is placed or as soon after receiving the
pump as possible.
6.3.2 Storage of spares
Spares should be stored in a clean dry area away
from vibration. Inspection and re-treatment of
metallic surfaces (if necessary) with preservative is
recommended at 6 monthly intervals
6.4 Recommended spares (according to
API)
For start up purposes:
1 - set of bearings (line and thrust)
2 - sets of gaskets and o-ring
2 - wear rings set (2 ro 2 stationary)
1 - mechanical seals
1 - labyrinth set (drive and impeller end)
For normal maintenance:
1 - set of bearings (line and thrust)
2 - sets of gaskets and o-ring
2 - wear rings set (2 ro 2 stationary)
1 - mechanical seals
1 - labyrinth and deflector set
(drive and impeller end)
1 - shaft
1 - impeller
6.5 Tools required
A typical range of tools that will be required to
maintain these pumps is listed below
Readily available in standard tool kits, and dependent
on pump size:
•
Open ended spanners (wrenches) to suit up to 2”
(M 50) screws/nuts
•
Socket spanners (wrenches), up to 2” (M 50)
screws
•
Allen keys, up to 10 mm (A/F)
•
Range of screwdrivers
•
Soft
mallet
More specialized equipment:
•
Bearing
pullers
•
Bearing induction heater
•
Dial test indicator