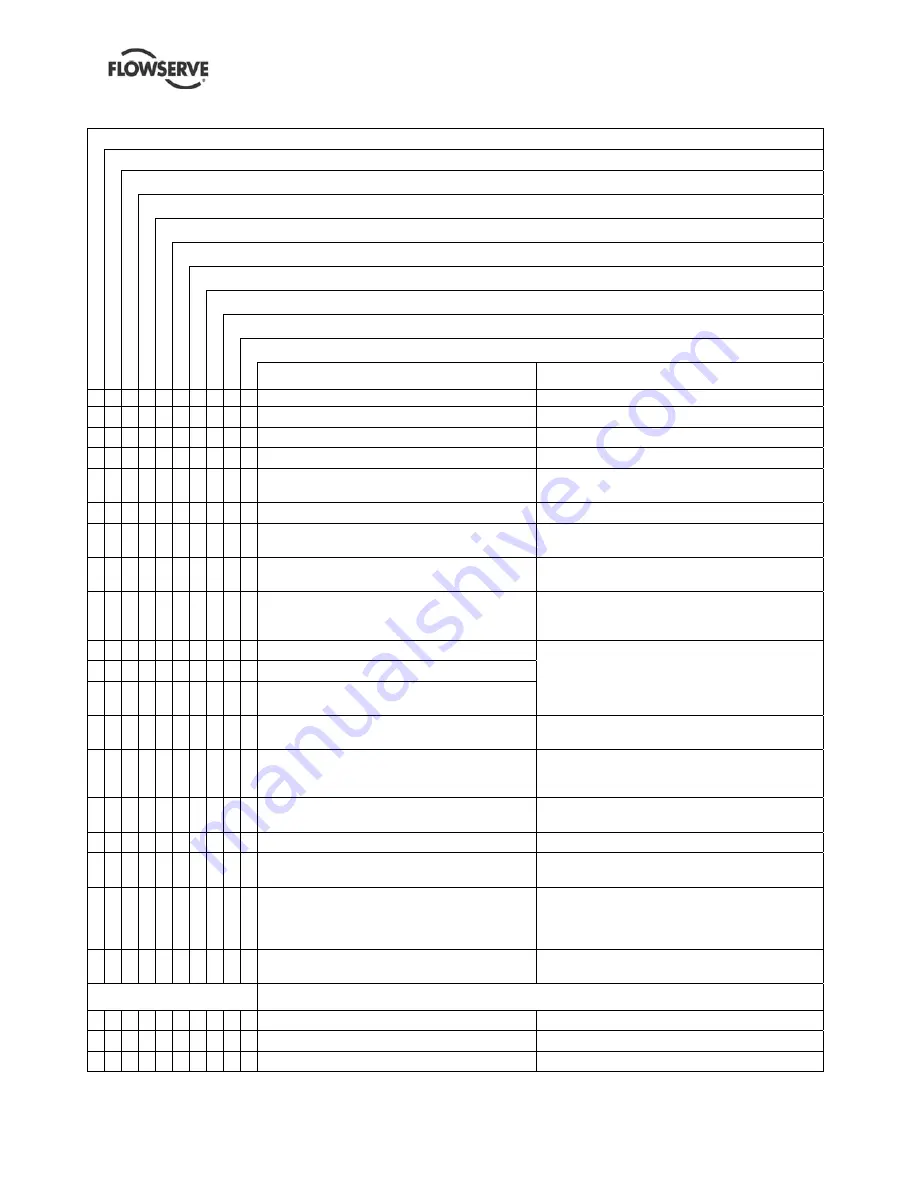
HPXM USER INSTRUCTIONS ENGLISH 14983571 - 03/11
Page 39 of 48
FAULT SYMPTOM
P u m p o ve r h e a ts a n d s e i z e s
⇓
⇓
B e a r i n g s h a ve s h o r t l i f e
⇓
⇓
P u m p vi b r a t e s o r i s n o i s y
⇓
⇓
M e c h a n i c a l s e a l h a s s h o r t l i f e
⇓
⇓
M e c h a n i c a l s e a l l e a k s e x c e s s i ve l y
⇓
⇓
P u m p r e q u i r e s e x c e s s i ve p o w e r
⇓
⇓
P u m p l o s e s p r i m e a ft e r s ta r t i n g
⇓
⇓
I n s u f f i c i e n t p r e s s u r e d e ve l o p e d
⇓
⇓
I n s u f f i c i e n t c a pa c i t y d e l i v e r e d
⇓
⇓
P u m p d o e s n o t d e l i ve r l i q u i d
⇓
⇓
PROBABLE CAUSES
POSSIBLE REMEDIES
CONSULT FLOWSERVE.
z z z
z
Rotating part rubbing on stationary part internally.
Check and CONSULT FLOWSERVE, if necessary.
z z z z z
Bearings worn
Replace bearings.
z
z z
Wearing ring surfaces worn.
Replace worn wear ring/surfaces.
z
z z
Impeller damaged or eroded.
Replace or CONSULT FLOWSERVE for improved
material selection.
z
Leakage under sleeve due to joint failure.
Replace joint and check for damage.
z z z
Mechanical seal improperly installed.
Check alignment of faces or damaged parts and
assembly method used.
z z z
Incorrect type of mechanical seal for operating
conditions.
CONSULT FLOWSERVE.
z z z z z
Shaft running off centre because of worn bearings
or misalignment.
Check misalignment and correct if necessary. If
alignment satisfactory check bearings for excessive
wear.
z z z z z
Impeller out of balance resulting in vibration.
z z z
Abrasive solids in liquid pumped.
z z
Internal misalignment of parts preventing seal ring
and seat from mating properly.
Check and CONSULT FLOWSERVE.
z z
Mechanical seal was run dry.
Check mechanical seal condition and source of dry
running and repair.
z z
Internal misalignment due to improper repairs
causing impeller to rub.
Check method of assembly, possible damage or
state of cleanliness during assembly.
Remedy or CONSULT FLOWSERVE, if necessary.
z z z
Excessive thrust caused by a mechanical failure
inside the pump.
Check wear condition of impeller, its clearances and
liquid passages.
z z
Excessive grease in ball bearings.
Check method of regreasing.
z z
Lack of lubrication for bearings.
Check hours run since last change of lubricant, the
schedule and its basis.
z z
Improper installation of bearings (damage during
assembly, incorrect assembly, wrong type of
bearing etc).
Check method of assembly, possible damage or
state of cleanliness during assembly and type of
bearing used. Remedy or CONSULT
FLOWSERVE, if necessary.
z z
Damaged bearings due to contamination.
Check contamination source and replace damaged
bearings.
C. MOTOR ELECTRICAL PROBLEMS
z
z
z z
Wrong direction of rotation.
Reverse 2 phases at motor terminal box.
z
z
Motor running on 2 phases only.
Check supply and fuses.
z z
z
Motor running too slow.
Check motor terminal box connections and voltage.