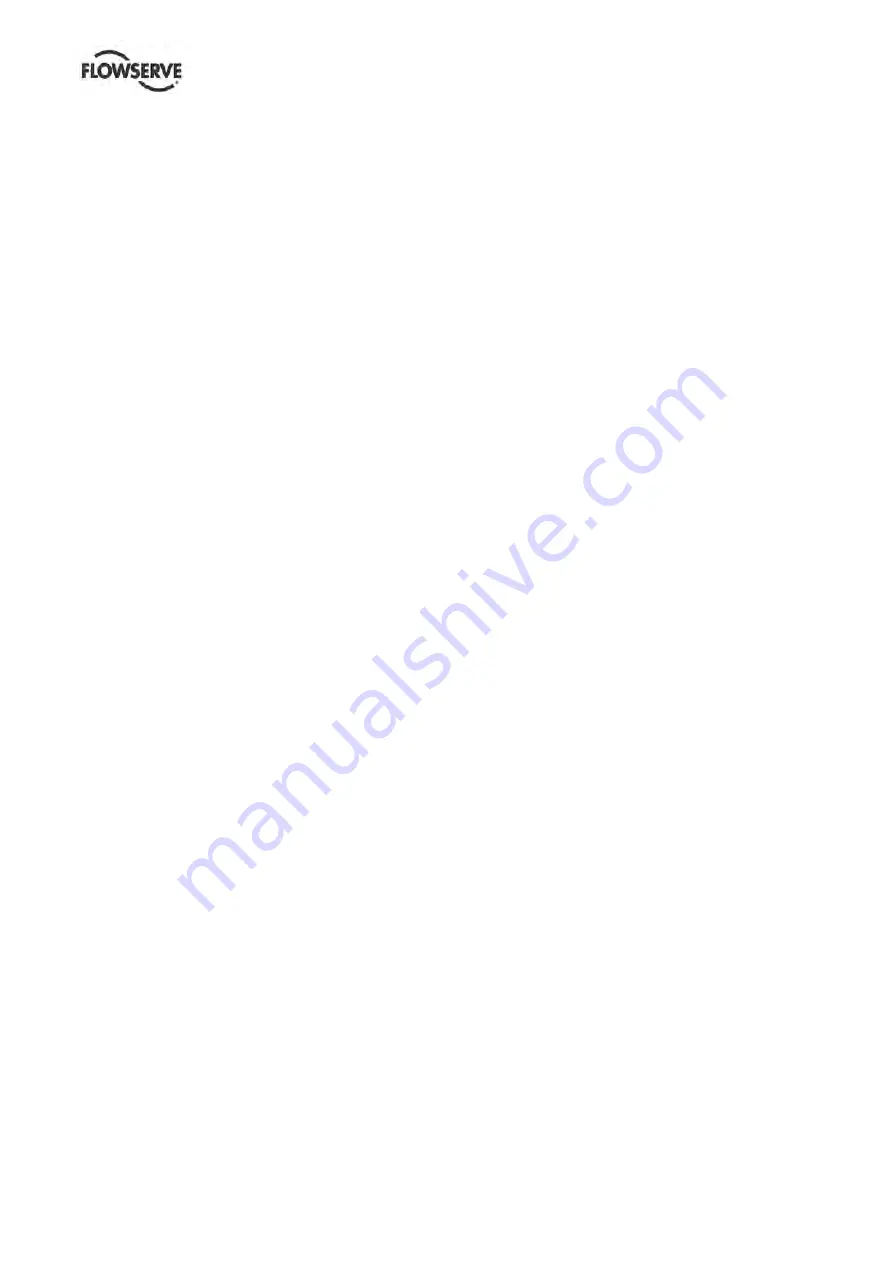
HWMA2 USER INSTRUCTIONS ENGLISH - 06/16
Page 36 of 39
10.3 Additional sources of information
Reference 1:
NPSH for Rotordynamic Pumps: a reference guide,
Europump Guide No. 1, Europump & World Pumps,
Elsevier Science, United Kingdom, 1999.
Reference
2:
Pump Handbook, 2
nd
edition, Igor J. Karassik et al,
McGraw-Hill Inc., New York, 1993.
Reference 3:
ANSI/HI 1.1-1.5
Centrifugal Pumps - Nomenclature, Definitions,
Application and Operation.
Reference 4:
ANSI B31.3 - Process Piping.