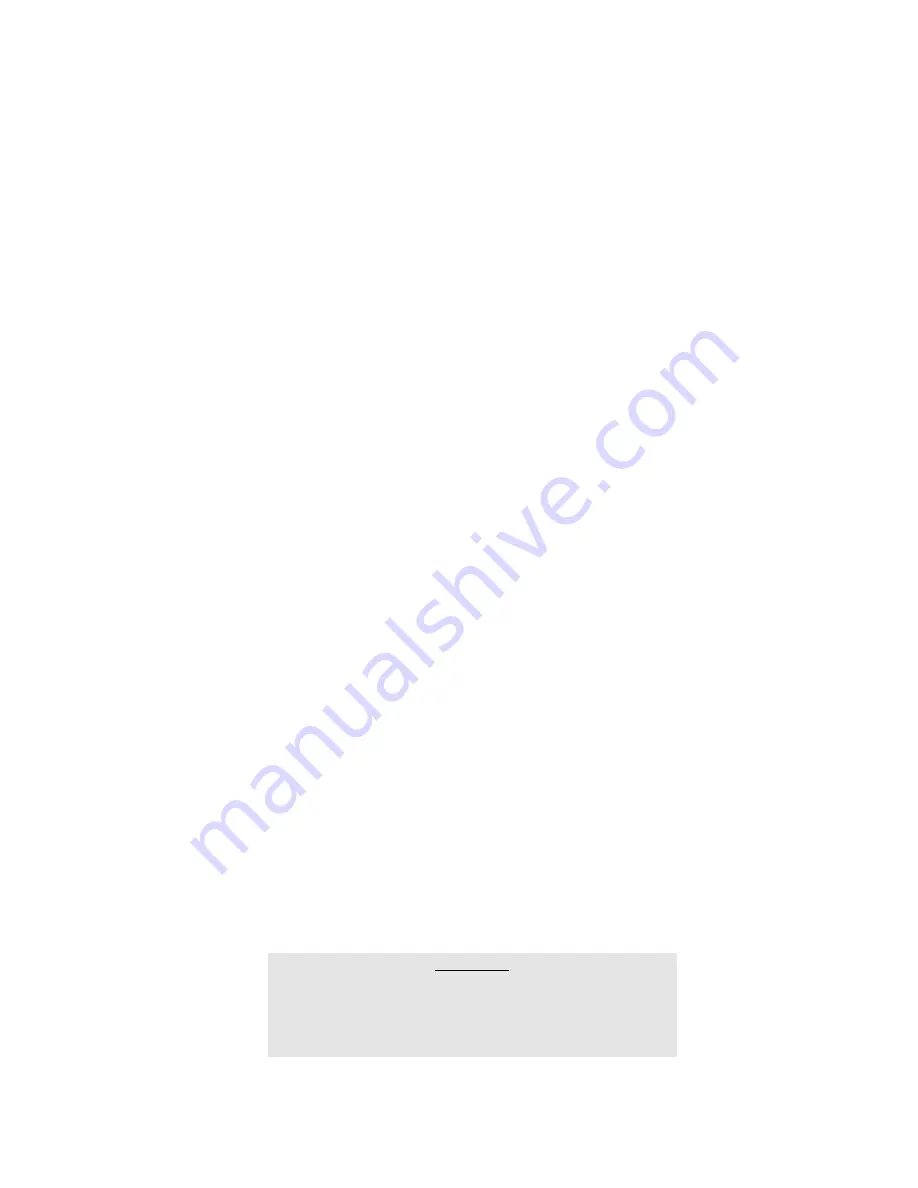
IJ PUMP OPERATION AND MAINTENANCE MANUAL
2-3
BO2660-01
2.1.3.2 Soleplate-Mounted Barrel Pump
There are two sets of four cardinal points that can be used to lift the combined weight of barrel pump,
cradle and soleplates. Their positions are physically defined by holes in each corner of the cradle and
by holes in each pump foot. Complete the set of instructions below (step 1 or step 2) that is applicable
to your circumstance.
1. When using apparatus (see NOTE preceding LIFTING above) and four cardinal points of
cradle to lift combined weight or to lift just pump and cradle:
a. install clevis in hole at each corner of cradle,
b. attach chain (or cable) to each clevis,
c. attach hoist to apparatus and take up slack,
d. verify that cables will not cut into pump, lagging, piping, panels, etc.,
e. establish that hoist is over center of gravity, then
f. hoist unit and dispose of it.
2. When using four cardinal points of pump, to lift combined weight, pump and cradle, or just
pump:
a. remove lagging (if installed) exposing pump feet,
b. install clevis in hole in each pump,
c. attach hoist to cables and take up slack,
d. verify that cables will not cut into pump panels, piping, etc. Remove any items that will
be damaged or protect items with wood blocks,
e. establish that hoist is over center of gravity, then
f. hoist unit (or pump) and dispose of it.
NOTE
With pump and cradle mounted on soleplates (after
soleplates have been secured to the foundation and, when
applicable, grouted) see that pump and equipment are
undamaged and that items that had been removed for lifting
of pump have been reinstalled (see INSTALLING NOZZLE
EXTENSIONS AND GROUTING).
2.1.3.3 Multistage Internal Assembly: Barrel Pump
When the multistage internal assembly is going to storage, handle it as described under STORAGE.
Comply with the following procedure for uncrating and subsequent handling:
CAUTION
Do not lift internal assembly by shaft or by eyebolts in
diffuser-covers. Do not attempt to remove assembly from
shipping crate without first removing sides and ends of
container. Failure to comply could result in bent shaft.
Summary of Contents for IJ
Page 2: ...IJ PUMP INSTALLATION OPERATION MAINTENANCE ...
Page 3: ......
Page 5: ...IJ PUMP OPERATION AND MAINTENANCE MANUAL BO2660 01 iv ...
Page 11: ...IJ PUMP OPERATION AND MAINTENANCE MANUAL BO2660 01 x ...
Page 13: ...IJ PUMP OPERATION AND MAINTENANCE MANUAL BO2660 01 xii ...
Page 17: ...IJ PUMP OPERATION AND MAINTENANCE MANUAL BO2660 01 xvi ...
Page 25: ......
Page 35: ...IJ PUMP OPERATION AND MAINTENANCE MANUAL BO2660 01 2 10 Figure 2 1 Foundation Bolt ...
Page 65: ......
Page 79: ......
Page 83: ......