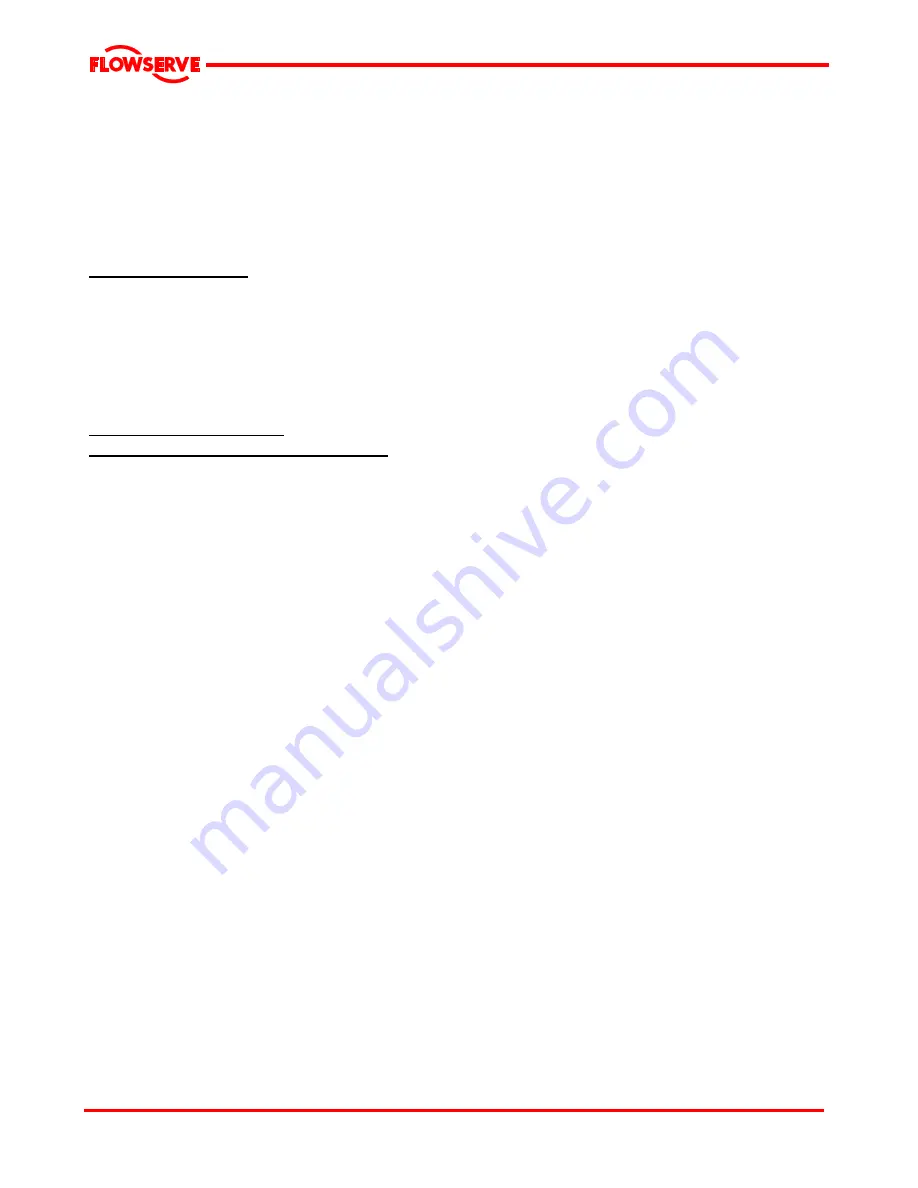
MPT USER INSTRUCTIONS ENGLISH 85392699 06-09
37 of 41
®
8.7 General Arrangement Drawing
The typical general arrangement drawing and any
specific drawings required by the Contract will be
sent to the Purchaser separately. If required, these
should be obtained from the Purchaser and
retained with this manual.
9 CERTIFICATION
Certificates determined from the Contract
requirements are provided with these instructions
where applicable. Examples are certificates for CE
marking, ATEX marking, etc. If required, copies of
other certificates sent separately to the Purchaser
should be obtained from the Purchaser for retention
with these User Instructions.
10 OTHER RELEVANT
DOCUMENTATION AND MANUALS
10.1 Supplementary Instruction
Manuals
See also the supplementary instruction manuals
supplied with this manual, e.g., for electric motors,
controllers, engines, gearboxes, sealant systems,
etc.
10.2 Change notes
If any changes, agreed with Flowserve Pump
Division, are made to the product after its supply, a
record of the details should be maintained with
these User Instructions.
Summary of Contents for MPT 20
Page 24: ...MPT USER INSTRUCTIONS ENGLISH 85392699 06 09 24 of 41 Page left intentionally blank ...
Page 38: ...MPT USER INSTRUCTIONS ENGLISH 85392699 06 09 38 of 41 NOTES ...
Page 39: ...MPT USER INSTRUCTIONS ENGLISH 85392699 06 09 39 of 41 NOTES ...
Page 40: ...MPT USER INSTRUCTIONS ENGLISH 85392699 06 09 40 of 41 NOTES ...