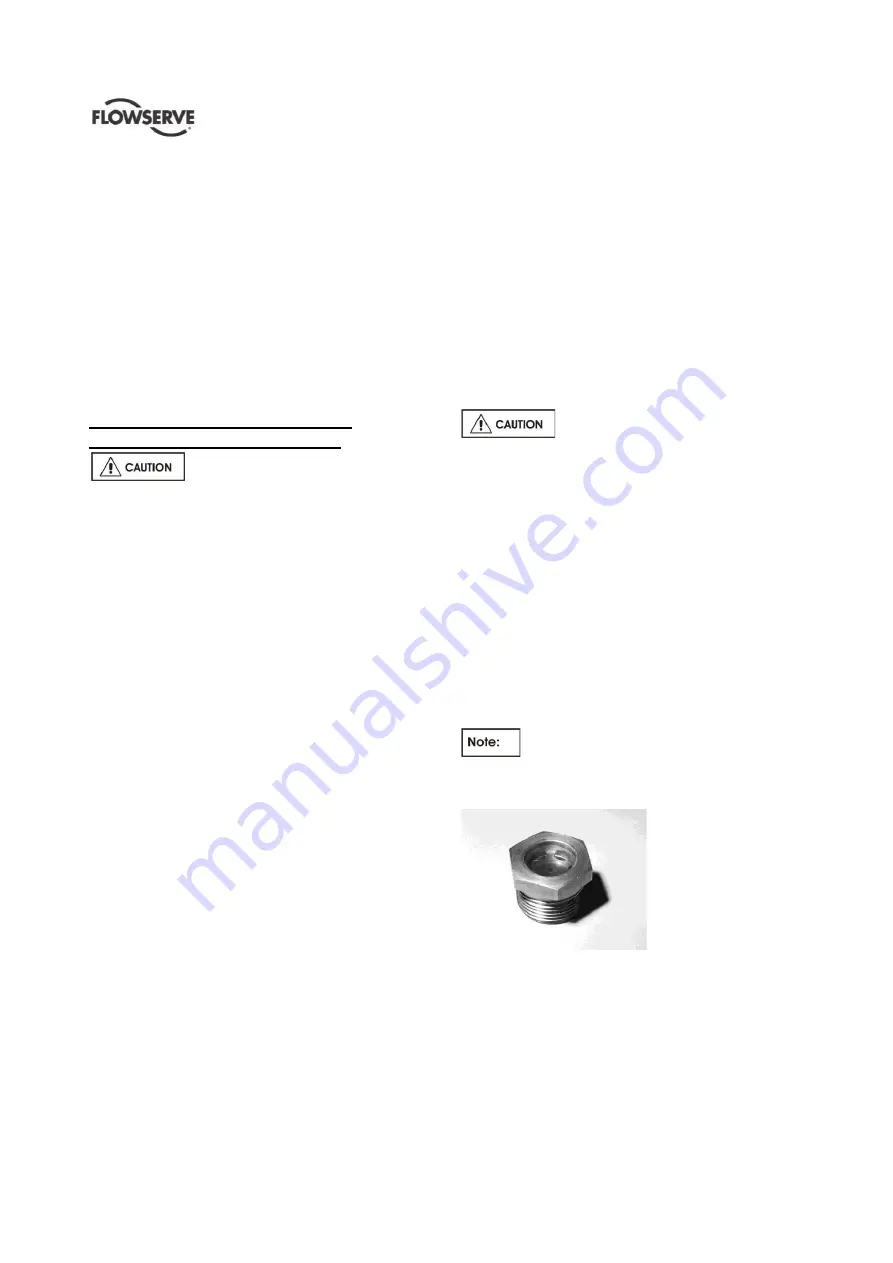
USER INSTRUCTIONS POLYCHEM GRP ENGLISH 71569132 12-04A
Page 24 of 52
flowserve.com
If there are any circumstances in which the system
can allow the pump to run dry, or start up empty, a
power monitor should be fitted to stop the pump or
prevent it from being started. This is particularly
relevant if the pump is handling a flammable liquid.
If leakage of product from the pump or its associated
sealing system can cause a hazard it is
recommended that an appropriate leakage detection
system is installed.
To prevent excessive surface temperatures at
bearings it is recommended that temperature or
vibration monitoring are carried out.
5 COMMISSIONING, START-UP,
OPERATION AND SHUTDOWN
These operations must be carried
out by fully qualified personnel.
5.1 Pre-commissioning procedure
5.1.1 Pre start-up checks
Prior to starting the pump it is essential that the
following checks be made. These checks are all
described in detail in section 6,
Maintenance
.
Pump and motor properly secured to the
baseplate
All fasteners tightened to the correct torque
Coupling guard in place and not rubbing
Rotation check. (See section 5.4.)
This is absolutely essential
Impeller clearance setting
Shaft seal properly installed
Seal support system operational
Bearing lubrication
Pump instrumentation is operational
Pump is primed
Rotation of shaft by hand
As a final step, in preparation for operation, it is
important to rotate the shaft by hand to be certain that
all rotating parts move freely, and that there are no
foreign objects in the pump casing.
5.2 Pump lubricants
5.2.1 Oil bath
Oil bath is available on all product lines with the
exception of the In-line pump. The standard bearing
housing bearings are oil bath lubricated and are not
lubricated by Flowserve. Before operating the pump,
fill the bearing housing to the center of the oil sight
glass with the proper type oil. (See figure 5-2 for
approximate amount of oil required - do not overfill.)
On the Mark 3A design, an optional oil slinger is
available. The oil slinger is not necessary; however,
if used, it provides an advantage by allowing a larger
tolerance in acceptable oil level. Without an oil
slinger, the oil level in the bearing housing must be
maintained at ±3 mm (±
1
/
8
in.) from the center of the
sight glass. The sight glass has a 6 mm (¼ in.) hole
in the center of its reflector. The bearing housing oil
level must be within the circumference of the center
hole to ensure adequate lubrication of the bearings.
See figure 5-3 for recommended lubricants.
DO NOT USE DETERGENT OILS.
The oil must be free of water, sediment, resin, soaps,
acid and fillers of any kind. It should contain rust and
oxidation inhibitors. The proper oil viscosity is
determined by the bearing housing operating
temperature as given in figure 5-4.
To add oil to the housing, clean and then remove the
vent plug [6521] at the top of the bearing housing,
pour in oil until it is visually half way up in the sight
glass [3856]. Fill the constant level oiler bottle [3855],
if used, and return it to its position. The correct oil
level is obtained with the constant level oiler in its
lowest position, which results in the oil level being at
the top of the oil inlet pipe nipple, or half way up in
the sight glass window. Oil must be visible in the
bottle at all times.
On ANSI 3A™ power ends there is no
constant level oiler. As stated above, proper oil level
is the center of the “bull’s eye” sight
glass [3856].
(See figure 5-1.)
Figure 5-1
In many pumping applications lubricating oil becomes
contaminated before it loses its lubricating qualities or
breaks down. For this reason it is recommended that
the first oil change take place after approximately 160
hours of operation, at which time, the used oil should
be examined carefully for contaminants. During the
initial operating period monitor the bearing housing
operating temperature.