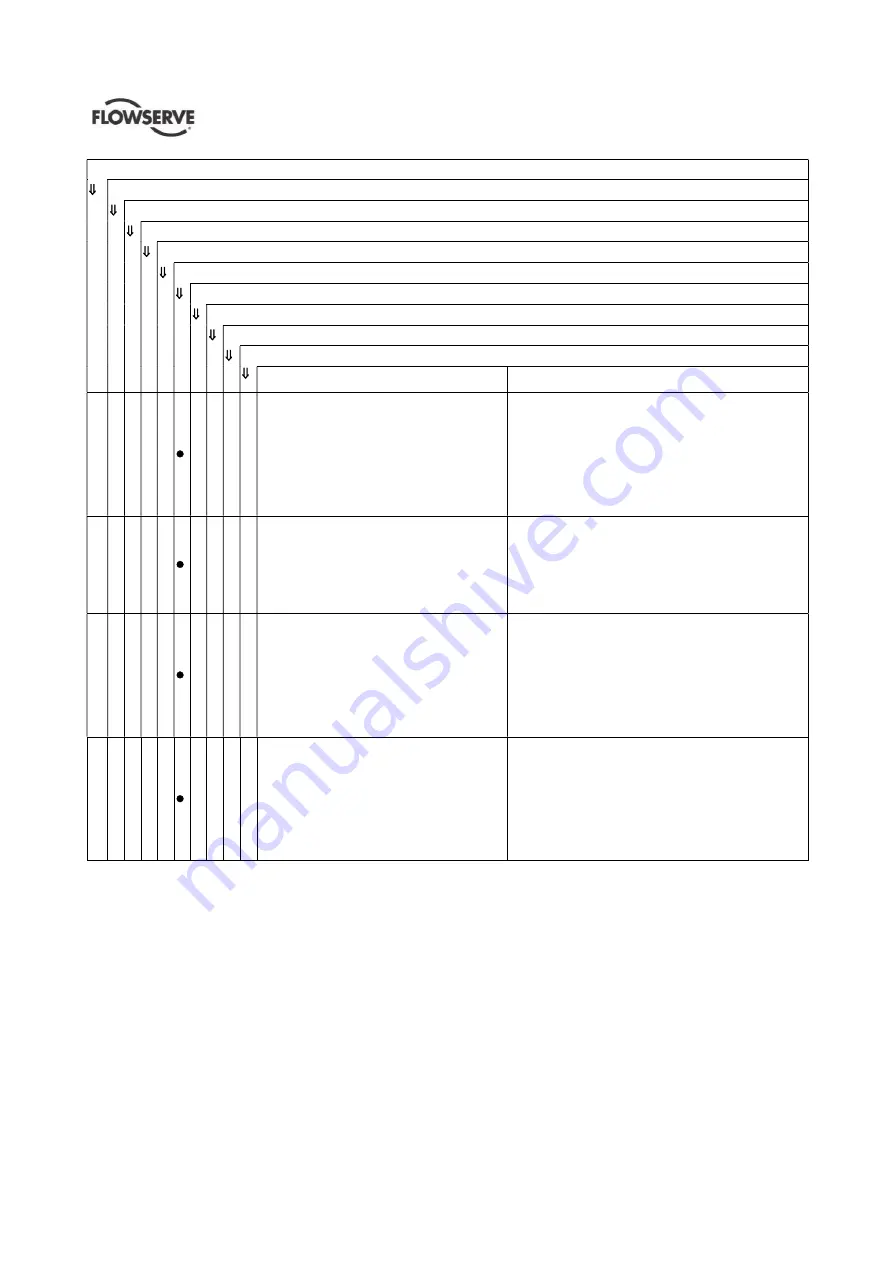
USER INSTRUCTIONS POLYCHEM GRP ENGLISH 71569132 12-04A
Page 47 of 52
flowserve.com
Pump not reaching design flow rate
Pump not reaching design head (TDH)
No discharge or flow with pump running
Pump operates for short period, then loses prime
Excessive noise from wet end
Excessive noise from power end
PROBABLE CAUSES
POSSIBLE REMEDIES
Thrust overload on bearing identified by flaking
ball path on one side of the outer race or in the
case of maximum capacity bearings, may
appear as a spalling of the races in the vicinity
of the loading slot. (Please note: maximum
capacity bearings are not recommended in
Mark 2I pumps.) These thrust failures are
caused by improper mounting of the bearing or
excessive thrust loads.
Follow correct mounting procedures for bearings.
Misalignment identified by fracture of ball
retainer or a wide ball path on the inner race
and a narrower cocked ball path on the outer
race. Misalignment is caused by poor mounting
practices or defective drive shaft. For example,
bearing not square with the centerline or
possibly a bent shaft due to improper handling.
Handle parts carefully and follow recommended mounting
procedures. Check all parts for proper fit and alignment.
Bearing damaged by electric arcing identified
as electro- etching of both inner and outer ring
as a pitting or cratering. Electrical arcing is
caused by a static electrical charge emanating
from belt drives, electrical leakage or short
circuiting.
1. Where current shunting through the bearing cannot be
corrected, a shunt in the form of a slip ring assembly
should be incorporated.
2. Check all wiring, insulation and rotor windings to be
sure that they are sound and all connections are properly
made.
3. Where pumps are belt driven, consider the elimination
of static charges by proper grounding or consider belt
material that is less generative.
Bearing damage due to improper lubrication,
identified by one or more of the following:
1. Abnormal bearing temperature rise.
2. A stiff cracked grease appearance.
3. A brown or bluish discoloration of the
bearing races.
1. Be sure the lubricant is clean.
2. Be sure proper amount of lubricant is used. The
constant level oiler supplied with Durco pumps will
maintain the proper oil level if it is installed and operating
properly. In the case of greased lubricated bearings, be
sure that there is space adjacent to the bearing into
which it can rid itself of excessive lubricant, otherwise the
bearing may overheat and fail prematurely.
3. Be sure the proper grade of lubricant is used.