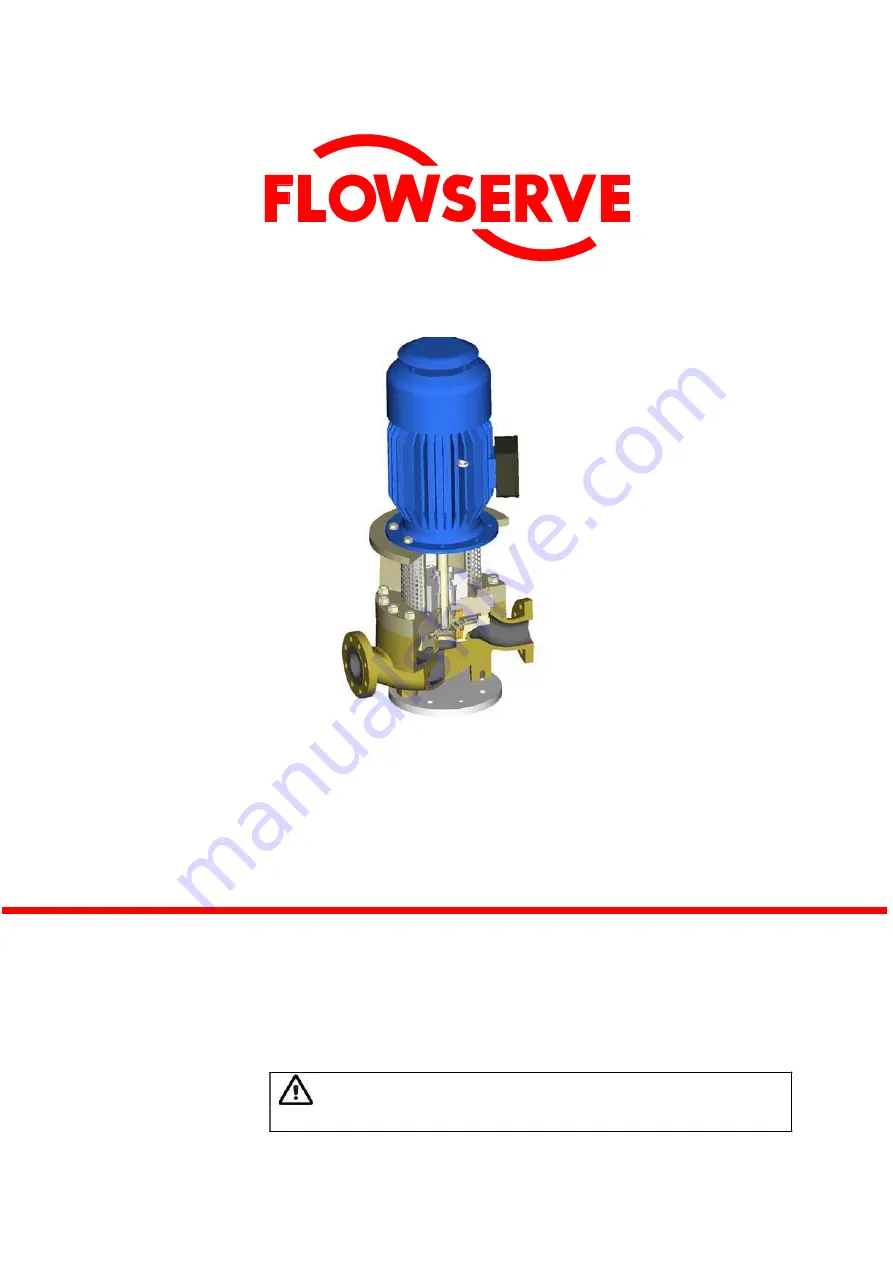
®
Pump Division
Type:
PVML
CENTRIFUGAL PUMPS
USER INSTRUCTIONS:
INSTALLATION, OPERATION, MAINTENANCE
PCN=00079591, ed. 01-05
(E)
These instructions should be read prior to installing,
operating, using and maintaining this equipment.
Компания ПромХимТех
-
официальный дистрибьютор
насосов
Flowserve
Тел
. 8 800 250-01-54