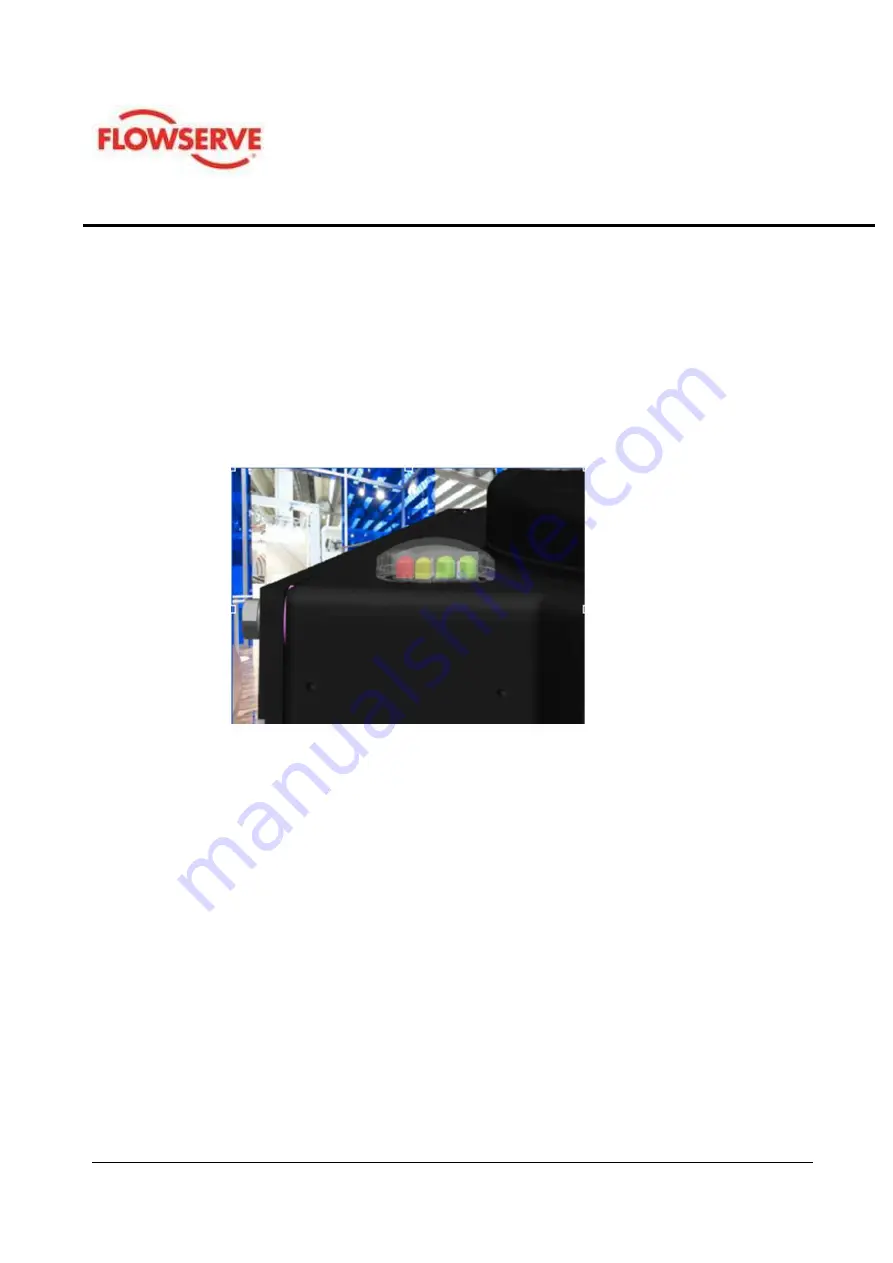
56
Flowserve US Inc.
SIHI
dry
dry
dry
dry
Standard
Standard
Standard
Standard M Series
Dry Running Vacuum Pump
Issue Date: November 21, 2016 Copyright:
FLOWSERVE SIHI Pumps Rev 1
9.4 Operation Indicator
The Indicator signals are provided from the electronics as 24Volt logic signal. W ith a suitable control
panel these signals can be displayed. The following signals will be made:
One Green – turning/standby/stopping
Two Green – Vacuum Operation
One Green & One Yellow – Start-up rotor diagnosis
Two Green & One Yellow – Warning
One Green & One Red – Failure Stopping
One Red - Failure Stop
Figure 19: Operating Indicators
Operation (green): Signals a rotating pump ready for operation.
Warning (yellow): Signals trouble or indicates the state of the rotor diagnosis.
Failure (red): Signals that a failure or defect has occurred, the pump will be stopped or is already at standstill.
Cleaning (yellow): Signals that the pump is in the cleaning phase.
Vacuum operation (green): The suction valve is opened and the pump is in the pumping phase.
Summary of Contents for SIHI dry Standard H Series
Page 82: ......