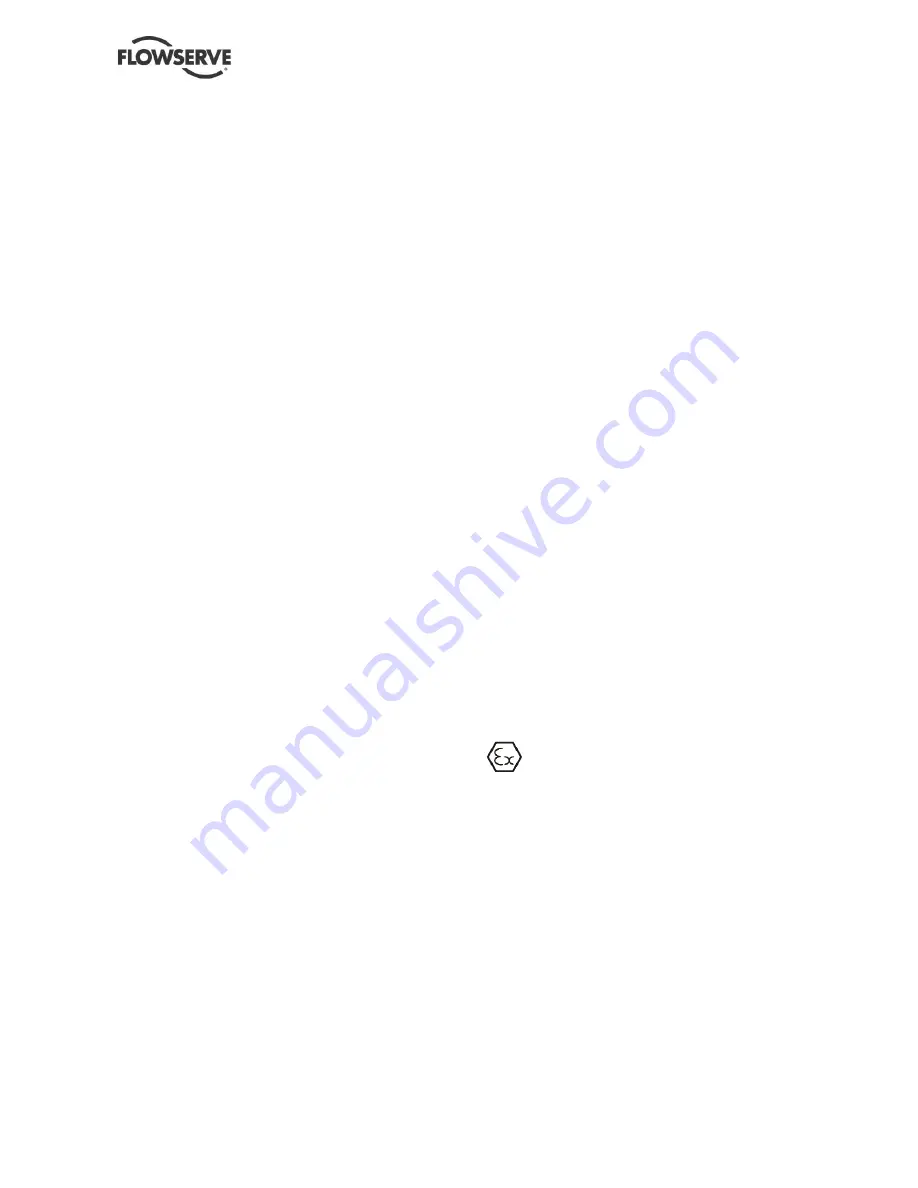
WIK USER INSTRUCTIONS ENGLISH BO2662 5/09
Page 15 of 76
3.3.3 Suction spacer casing and discharge
spacer casing.
The suction spacer casing [1130] does not
incorporate a diffuser. The discharge spacer casing
[1140] does incorporate a diffuser in the same
manner as the intermediate cover [1460] (see
Intermediate cover diffuser above).
3.3.4 Wearing rings and bushings
A renewable wearing ring [1500] is fixed in each
intermediate cover diffuser [1460], the suction
spacer casing [1130], and the discharge spacer
casing diffuser [1140]. A renewable bushing [1610]
is fixed in each intermediate cover diffuser [1460]
and the discharge spacer casing diffuser [1140].
These rings and bushings protect the intermediate
covers and casings from the washing action that is
generated by the skirt and hub of each impeller as
they spin rapidly in the pumpage (or flow). The rings
and bushings are surface-hardened.
3.3.5 Impellers
Impellers [2200] are keyed [6700.4] to the shaft
[2100] with one or two keys and have an
interference fit with the shaft. Because of hydraulic
requirements for efficiency, the pattern of the pump
suction impeller usually differs from the radial
impellers at the other stages. Normally, the pump
discharge impeller has the same pattern as the
radial impellers of the intermediate stages. The
impeller hubs and skirts are surfaced-hardened, or
fitted with surfaced hardened wearing rings.
3.3.6 Bearings
The radial load on the shaft is carried by sleeve
bearings [3020] and the axial thrust load is taken by
a Kingsbury thrust bearing [3032].
3.3.7 Shaft seals
To prevent pumpage (or flow) from leaking around
the shaft, your barrel pump is equipped with
mechanical seals. For an illustration of the seals,
see the seal manufacturer's drawing in section 10.
3.3.8 Lube oil system
Your pumps are equipped with a pressurized lube oil
system. For detailed description, see section 10.
3.3.9 Seal piping
For a description of seal piping, see PIPING
drawings in section 10.
3.3.10 Baseplates
The pump is factory mounted on a baseplate and its
driver (if furnished by Flowserve) is mounted on a
baseplate or soleplate (see Outline drawing in
section 8)
3.3.11 Drivers
For a description of drivers furnished by Flowserve,
see section 10.
3.3.12 Special tools
When a special tool is required for pump
maintenance, repair, or overhaul and is ordered with
your pump, it is normally described by Flowserve
Product Engineering drawing in section 10. Its use is
covered in the instructions for performing the
particular task for which it is designed.
3.3.13 Interference fit.
These parts are designed for an interference fit with
the shaft; that is, the parts are a few thousandth of
an inch smaller than the shaft: impellers, balance
drum, and thrust collar. When the parts are so
designed, the fit is given in inches and millimeters in
section 10.3 of this manual; appropriate handling
procedures are given in section 6.
3.4
Performance and operating limits
Refer to section 10.3.
4
INSTALLATION
Poor location and use of inadequate standards for
the preparation of the foundation adversely affect
pump life. A good foundation is particularly important
since it can be a primary factor in preventing
vibration, a major cause of wear and failure of the
pump.
Equipment operated in hazardous locations
must comply with the relevant explosion protection
regulations. See section 1.6.4
4.1
Location
When locating the pump, consideration should be
given to the following factors that bear on its
operation and maintenance.
1) Head, end, and side room necessary for
overhaul, removal, and inspection; also space
for maneuvering hoisting equipment.
2) Shortest practicable distance between source of
liquid and suction flange on pump.
3) Sufficient net positive suction head (NPSH) at
suction flange of pump.