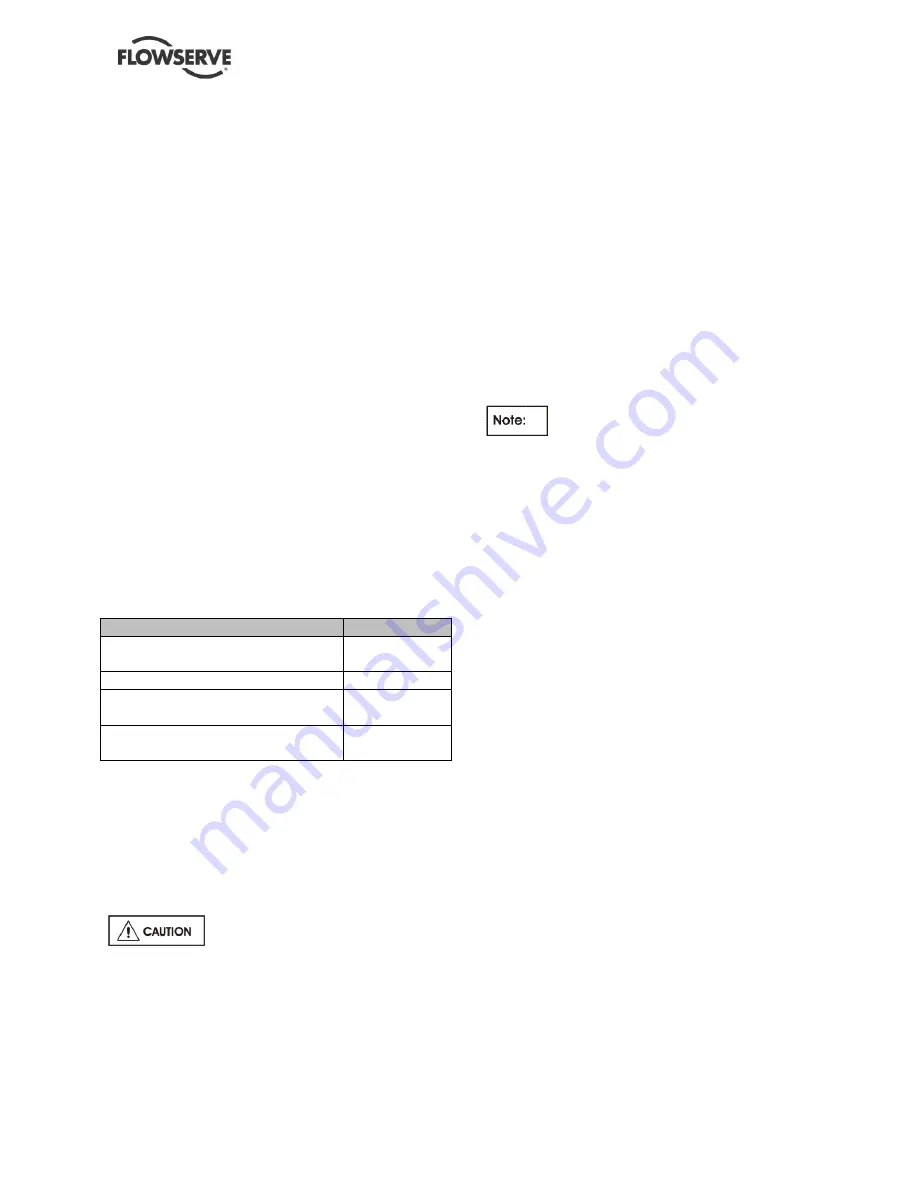
WIK USER INSTRUCTIONS ENGLISH BO2662 5/09
Page 32 of 76
5.2.2 Lube oil change recommendations
Flowserve recommends that the lube oil in the pump
be inspected periodically, at least weekly, and
changed whenever:
a) The lube oil color darkens, indicating
contamination from dirt and foreign
substances
b) The lube oil appears milky or emulsified
c) Foreign particles appear in the lube oil
As a minimum, lube oil should be changed at least
every six months.
5.2.3 Oil specifications
Straight mineral oils without additives are generally
preferred for rolling element bearing lubrication. It
should preferably be of the turbine type and not
contain free acid, chlorine, sulfur or more than a
trace of free alkali. Quality mineral oils with a
minimum Viscosity Index (VI) of 95 is recommended.
An ISO Viscosity Grade (VG) Number identifies
lubricating oils. The VG Number is the viscosity of
the oil at 38°C (100°F) in centistokes. In the majority
of instances, a turbine oil with a VG Number of 32
(nominally equivalent to SAE 10) will meet rolling
element bearing lubrication requirements (see oil
temperature).
Oil Characteristics
Saybolt Viscosity (SSU) 38°C
(100°F)
158 Seconds
Pour Point
-7°C (20°F)
Flash Point
204°C
(400°F)
Recommended ISO Viscosity
Grade (VG) Number
32
Oil Characteristics
In a majority of instances, ISO 32 (nominally
equivalent to SAE 10 turbine type oil) will meet the
above specification. Refer to lube, seal, and lube oil
console piping drawings and notes for information
pertaining to your system.
Lubricant must be compatible with all
parts requiring lubrication.
ISO 32 may be considered for continuous operating
oil temperatures between 16°C (60°F) and 49°C
(120°F), with a minimum start up temperature of 4°C
(40°F). For start-up when oil temperature is below
4°C (40°F), oil preheating is recommended.
5.2.4 Flushing and cleaning lube oil system
During work on the piping of a pump, dirt, grit, and
chips are apt to accumulate inside the piping. This
can happen to new, factory-installed piping that has
been thoroughly cleaned as well as piping on a
pump that has been in service for some time.
Therefore, to prevent bearing damage from such
matter, it is foresighted to clean and flush the lube oil
system following field work on the piping of any
pump, where the work performed involved storage,
installation, or fabrication.
Flowserve recommends the use of either flushing
procedure that is given below; however, if your
pump is equipped with auxiliary lube oil pump, its
use is preferred.
Regardless of which procedure is used to
flush the lube oil system, it will be necessary to
employ a lube oil filter in the piping, downstream of
the lube oil pump. Additionally it will be necessary to
have a differential pressure indicator across the filter.
5.2.4.1 Flushing lube oil system using auxiliary
lube oil pump
The following flushing procedure applies to a pump
that is equipped with an auxiliary lube oil pump. For
illustrations of piping and parts which are referred to
in the procedure, see lube oil piping and assembly
drawings in the back of this manual.
1) Remove inboard sleeve bearing, outboard
sleeve bearing, and thrust bearings (see section
6.7.4). Reinstall upper halves of housings, using
only half of parting flange bolts.
2) Remove reservoir cover, thoroughly clean
interior with petroleum base solvent such as
kerosene or naphtha, and wipe dry with clean,
lint free rags
3) Fill reservoir with recommended type lube oil
(see section 10.3) heated, if practicable, to 82°C
(180°F).
4) Perform first phase of flushing cycle as follows:
a) Start auxiliary lube oil pump and circulate
lube oil for 20 hours.
b) During 20-hour cycle, continuously tap entire
length of piping to loosen scale and slag.
c) During 20-hour cycle, periodically check
differential pressure indicator at filter for an
increase in differential pressure that could
indicate filter is becoming clogged. Consider
indication in relation with such factors as
capacity of filter, temperature of flush,
pressure of flush and general condition of
piping. Should consideration point to a
clogged filter shut down auxiliary lube oil