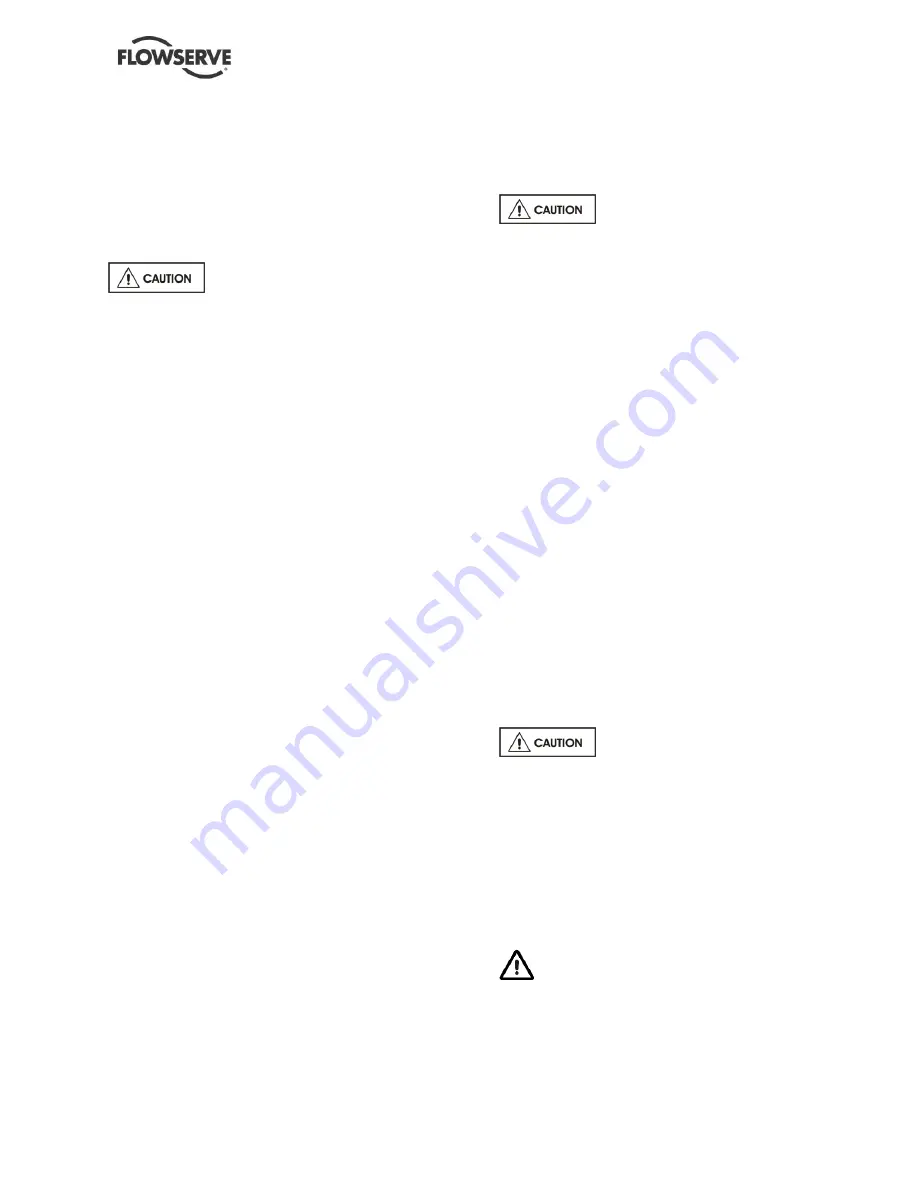
WIK USER INSTRUCTIONS ENGLISH BO2662 5/09
Page 51 of 76
2) When removing balance drum bushing [1600],
note method used by factory for retaining
bushing to casing cover [1221], if any; then
use rotary file and grind off tack welds or stake
marks, whichever is applicable, and remove
cap screws (if installed). Use jack screws in
holes provided and remove bushing [1600]
from casing cover [1221].
Failure to ensure that the inner
casing cover gasket disc spacers [3645] that were
supplied with the pump, or precise replicas, are
used in reassembly could result in improper
makeup of intermediate covers [1460], the suction
spacer casing [1130], and the discharge spacer
casing [1140], causing recirculation, erosion, and
decreased efficiency.
3) As a precaution against loss of an inner casing
cover gasket disc spacer [3645], measure
thickness of each spacer with a micrometer
and record measurements.
6.7.8 Disassembling internal assembly
The disassembly sequence is determined by shaft
design (the shaft is stepped up towards the
coupling end). All parts are removed from the free
end of the shaft [2100]. This manual offers two
methods for disassembling the internal assembly:
vertical and horizontal. The vertical method is
preferred, because it reduces the chances of
damaging the register faces of the intermediate
cover [1460].
6.7.8.1
Interference Fit Part Removal
To remove an interference fit part, proceed with
the following general procedure:
1) Before removing part, ensure that:
a) Shaft is kept smooth and clean: scratched
surfaces or dirt will further the possibility of
parts seizing to the shaft [2100]
b) Temperature of the shaft [2100] is kept
within 11°C (20°F) of ambient air
temperature by cooling it with shop air, or
by allowing it to cool in ambient air (do not
cool the shaft by any other means)
c) Shaft [2100] is lubricated with a lubricant
that is compatible with your pumpage,
such as powdery Molykote or Neolube
(graphite in isopropanol)
d) For horizontal disassembly, ensure that
the weight of the discharge spacer casing
[1140], intermediate covers [1460], or
suction spacer casing [1130] will be
supported during removal (with lifting gear,
if necessary) and that the shaft [2100] is
protected with heat-resistant gasket
material or equivalent to prevent damage
to the shaft [2100] due to dropped
components
Application of excessive heat can
cause part distortion and damage. Application of
insufficient heat can cause scouring of the parts
when attempting removal. Ensure that the part is
heated to the temperature specified in section 10.3
before removal.
2) To heat a part to its removal temperature
specified in section 10.3, proceed as follows:
a) To heat an impeller [2200], spacer sleeve,
or pressure reducing balance drum [6230]:
use a torch with a number 10 Rosebud
head and start at the outer rim of the part,
applying even heat in a continuous
circular path to the center of the part until
the part is heated to the temperature
specified in section 10.3. Keep the shaft
cool using shop air, and do not heat the
hub or skirt of an impeller [2200].
c) To heat a suction spacer casing [1130] or
intermediate cover [1460]: use a torch with
a number 10 Rosebud head and make
uniform passes around the outer surface
where the cover or spacer meets the
cover that is to be removed, keeping this
surface at the temperature given in section
10.3. Do not heat the entire outer surface,
and do not heat the cover that is to be
removed.
Do not allow the roll-and-heel bars
to slip below the cutout on the discharge spacer
casing [1140], intermediate cover [1460], or
suction spacer casing [1130], as this may damage
the sealing faces of those components.
3) When a part has been heated to its removal
temperature, use two roll-and-heel bars 180
degrees apart on the outer edge of the part to
remove it from its position with quick,
simultaneous prying motions.
Use lifting gear when moving any part
that weighs more than 22 kg (50 Ib) to prevent
personnel injury and part damage due to
dropping.
Always ensure that hot parts are handled with
soft cables or hands protected by heat-
resistant gloves to prevent personnel injury.