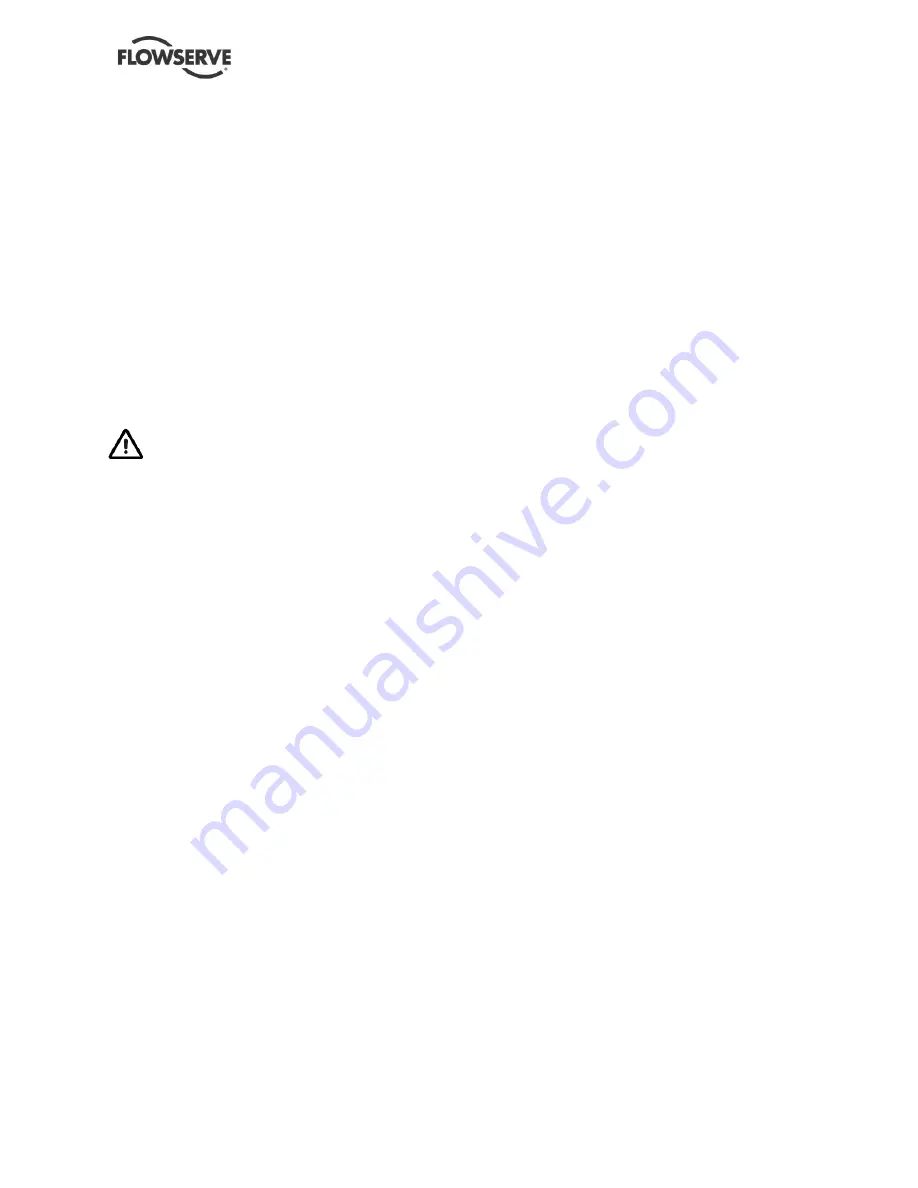
WIK USER INSTRUCTIONS ENGLISH BO2662 5/09
Page 54 of 76
lifting the shaft out of the V-blocks using one
hoist on each strap or one hoist and a
spreader bar. The shaft must be stored on a
flat, solid surface, or wooden blocks, at least
150 mm (6 in.) above a metal or concrete
surface.
6.8
Part cleaning, inspection, and repair
This subsection identifies conditions that
commonly impair the serviceability of parts, which,
if not corrected could also impair operation and
sometimes cause major damage. During your
inspection, should you require additional
information about a condition or repair which is not
covered here, contact your nearest Flowserve
Service Department (see section 6.2.1)
6.8.1
Cleaning
Petroleum solvents, alcohol, acetone and
other such chemicals are injurious to health
and may ignite from a spark; make certain that
they are used only in a well ventilated place,
away from heat, flame, and sparks.
You should clean the casing [1100] and all metal
parts with acetone, alcohol, a steam cleaner that
uses demineralized water and approved chemicals,
or a petroleum solvent such as naphtha or
kerosene; ensure that the cleaning agent used is
compatible with the pumped liquid.
Bearing housing components should be cleaned
with a solvent such as naphtha or kerosene and
dried with instrument air. To remove gasket
sealant from bearing housings, carefully peel old
film from parting surfaces. Use a plastic knife, or
equivalent material that is softer than carbon steel.
Clean parting surfaces with denatured alcohol or
acetone.
6.8.2 Inspection and repair
6.8.2.1 General
1) Verify that all parts are free of gouges, burrs,
scratches, excessive wear, and any other
imperfections. Replace worn or damaged
parts.
2) Ensure that all parts are free from dirt,
deposits, or old gasket material. Perfectly
clean and smooth surfaces are required. Any
part from which deposits cannot be removed
must be replaced.
3) All replacement parts must be obtained from
the original equipment manufacturer to ensure
proper tolerances and fit. It is unlikely that a
field shop can machine the contour of a part to
the close tolerance that is required to assure
that the part, and in turn the assembly, will
meet its design function.
6.8.2.2 Main lube oil pump
To perform any maintenance on the lube oil pump,
see its manufacturer's instructions in the section
10.
6.8.2.3 Bearings
The thrust bearing shoes, base ring halves, and
sleeve bearing halves must be replaced in sets.
6.8.2.4 Mechanical seal
6.8.2.4.1
Disassembling Seal Unit
After the seal unit has been removed from the
pump, disassemble it in accordance with the seal
manufacturer's installation and assembly drawing
in the section 10.
6.8.2.4.2
Inspection and Repair
Inspect, clean, and replace seal parts in
accordance with the seal manufacturer's
installation and assembly drawing in section 10.
Before installing the seal unit, visually inspect:
1) Shaft for cleanliness, nicks, excessive wear,
burrs, and galling.
2) Seal housing for cleanliness and damage;
gasket surfaces for nicks, scratches and burrs.
6.8.2.4.3
Assembling Seal Unit
After inspecting, cleaning and replacing parts in
the seal unit, assemble it in accordance with the
seal manufacturer's installation and assembly
drawing in section 10.
6.8.2.4.4
Replacing Seal Housing Bushing
Should the pump incorporate a stuffing box
bushing [4132] or throat bushing and one or both
sustain deep gouges, scoring, or distortion,
proceed with replacement as follows:
1) If the bushing is part of a seal housing, then
ensure the seal housing is removed from the
pump prior to removing bushing.
2) Depending on factory-method of retaining
bushing, use rotary file and grind off tack
welds or grind off stake marks and remove set
screws.
3) Use aluminum drift (or equivalent) and knock
out bushing.
4) Subcool new bushing in dry ice to shrink it;
then bottom bushing square in bore of parent
part by using aluminum drift and mallet to
strike evenly around circumference of bushing.